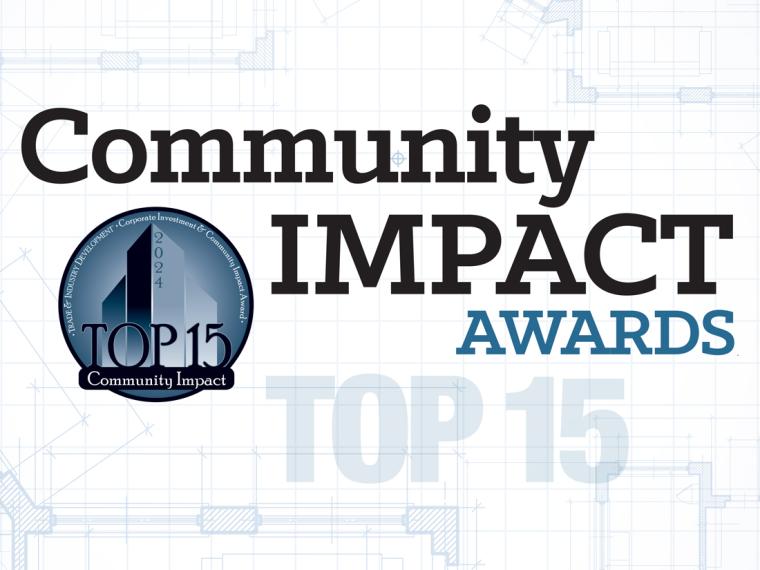
Nothing boosts a community better than a new investment. New projects create jobs and opportunities, change blighted property into a prosperous going concern, and often result in improvements in infrastructure and education for the area. While a majority of economic development is valued for being high-cost projects that infuse significant capital, smaller projects – the right project in the right area at the right time – can have an even bigger impact, particularly for economically underserved communities.
The location of a new facility or the expansion of an existing one can have a profoundly positive effect on the people who live, work and run businesses in an underserved area, even if the investment is modest. For the 18th annual CiCi Awards for Community Impact, Trade & Industry Development is recognizing 15 projects announced in 2023 that demonstrate how site selection can make a large difference in a community, providing jobs and opportunities.
The collective capital investment of our 15 winning projects totals about $3.5 billion, and these initiatives will create and/or retain more than 6,100 direct jobs. While these numbers may seem small compared to the projects on the Corporate Investment side, these smaller initiatives are helping to stabilize communities in need of employment and infrastructure improvement. Also, many community leaders emphasize that the addition or expansion of a business will help to attract similar businesses and even more investment and create thousands more indirect jobs.
Following are some of the inspirational stories behind our 2024 CiCi Community Impact winners. None of these projects, of course, would have been possible without the hard work of community leaders, local and state economic developers, along with the visionaries at the companies themselves.
Epsilon Advanced Materials
Brunswick County, North CarolinaLast year, Epsilon Advanced Materials, Inc., a company that provides synthetic graphite used in electric vehicle batteries, announced plans to build its first manufacturing facility in the U.S. in Brunswick County, North Carolina, creating 500 jobs. The India-based company will invest $649.9 million at the Mid-Atlantic Rail Industrial Park for its newest facility.
Epsilon Advanced Materials (EAM), a subsidiary of Mumbai-based Epsilon Carbon Private Limited, was established in 2018 to develop and manufacture high-performance graphite used for anode components in lithium-ion batteries. Graphite anode materials deliver desirable properties in batteries, such as fast charging, long cycle life and safety. The technology has proven its scalability to mass production, positioning the company to meet the rapidly growing demand for renewable energy storage.
The EAM project has been awarded funds from North Carolina’s Job Development Investment Grant (JDIG), a performance-based, discretionary incentive program that provides cash grants directly to a company when the company creates jobs and invests in the state. Grants are awarded only in competitive recruitment or retention situations. Over the course of the 12-year term of the JDIG grant, the project is estimated to grow the state’s economy by $1.3 billion. The North Carolina Department of Commerce led the state’s support for the company during its site evaluation and decision-making process.
Although wages will vary depending on the position, the average salary for the new positions will be $52,264. The current average wage in Brunswick County is $46,464.
In addition, because Epsilon chose a site in Brunswick County, which is classified by the state’s economic tier system as Tier 3, the company’s JDIG agreement also calls for moving $1.14 million into the state’s Industrial Development Fund – Utility Account. The Utility Account helps rural communities finance necessary infrastructure upgrades to attract future business. Even when new jobs are created in a Tier 3 county such as Brunswick, the new tax revenue generated through JDIG grants helps other economically challenged communities elsewhere in the state.
“Epsilon Advanced Materials’ investment in North Carolina shows that our state is continually a top location for the electric vehicle and battery sector and a leader in the clean energy economy,” said Christopher Chung, CEO of the Economic Development Partnership of North Carolina (EDPNC). “We are proud our accessible infrastructure, highly educated workforce and state and local partnerships have attracted another innovative company such as Epsilon Advanced Materials.”
Joby Aviation
Montgomery County, Ohio
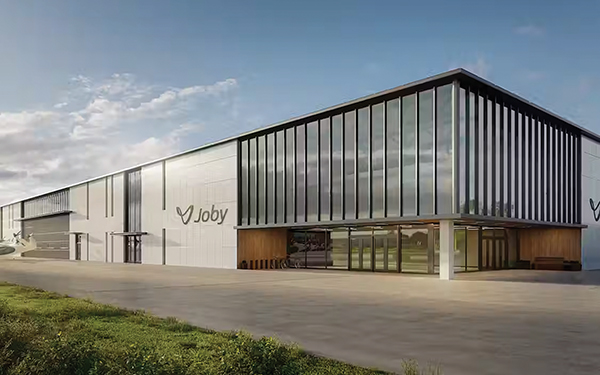
Air travel is a significant contributor to pollution: both the gaseous kind as well as noise pollution in urban and suburban areas. Technology is making a dent in the problem, however: California-based Joby Aviation, Inc. has announced plans to begin producing electric vertical take-off and landing (eVTOL) aircraft designed to transport a pilot and four passengers at speeds of up to 200 mph, with a maximum range of 100 miles and a revolutionary quiet noise profile that is barely audible against the backdrop of cities.
The company plans to operate these aircraft as part of aerial ridesharing networks in cities and communities around the world beginning in 2025, building on partnerships it has developed with Delta and Uber.
In September 2023, the company announced that it will build a scaled aircraft production facility in Dayton, Ohio with a capital investment of $477.5 million. Joby plans to build a facility capable of delivering up to 500 aircraft per year at the Dayton International Airport, supporting up to 2,000 jobs. The 140-acre site the company has chosen has the potential to support significant further growth over time, providing enough land to build up to two million square feet of additional manufacturing space. Construction of the scaled Ohio facility is expected to start this year and be completed in 2025. Joby plans to use existing nearby buildings to begin near-term operations.
The State of Ohio, JobsOhio and local political subdivisions have offered incentives and benefits of up to $325 million to support the development of the facility, while Joby plans to invest up to $500 million as it scales operations at the site. Joby also revealed that it has been invited by the U.S. Department of Energy to submit a Part II Application for financing under the Title XVII Loan Guarantee Program, which provides access to low-interest loans for clean energy projects and would support the scaling of the facility.
“We’re building the future of aviation right where it all started, in Dayton, Ohio,” said JoeBen Bevirt, Founder and CEO of Joby. “The Wright Brothers harnessed revolutionary technology of their time to open up the skies, and we intend to do the same — this time, bringing quiet and emissions-free flight that we hope will have an equally profound impact on our world.
ProKidney
Guilford County, North CarolinaProKidney Corp. is a late clinical-stage cellular therapeutics company focused on chronic kidney disease. The company, which is headquartered in Winston-Salem, North Carolina, was founded in 2018 after more than a decade of research. Its REACT (REnal Autologous Cell Therapy) protocol is a first-of-its-kind, patented, proprietary therapy with the potential to preserve kidney function in patients at high risk of kidney failure. ProKidney’s approach utilizes a patient’s own kidney cells in the treatment process.
In 2023, ProKidney announced plans to build a new biomanufacturing facility in Guilford County, North Carolina that will create up to 330 jobs. The $485 billion investment includes $25.5 million for closing on the facility in Greensboro to prepare for future commercial manufacturing of REACT. The company’s project in Guilford County will establish a 210,000 square-foot manufacturing facility that will feature multiple breakthroughs in the manufacturing automation, supply chain and medical delivery of cellular therapy products.
ProKidney chose the site in Guilford County – not far from its headquarters – to take advantage of the breadth of biotechnology talent in the state, which has been carefully cultivated by the state and regional development groups as a way of growing North Carolina’s biotechnology industry. The North Carolina Department of Commerce led the state’s support for the company during its site evaluation and decision-making process.
“As a former executive in the biotech industry, I’m proud to see North Carolina’s continued leadership in this industry, which means so much for both our economy and for people’s health and wellbeing,” said North Carolina Commerce Secretary Machelle Baker Sanders.
“We never take for granted the importance of a strong, well-trained workforce to keep us ahead of the pack. As our First in Talent strategic plan makes clear, we’ll continue to invest in our people and the educational systems that create opportunities for everyone.”
The project will offer significantly higher paying jobs than the regional average. Although wages will vary depending on the position, the average salary for the new positions at the facility are estimated to be $74,636. The current average wage in Guilford County is $57,190.
ProKidney’s project in North Carolina will be facilitated, in part, by a Job Development Investment Grant (JDIG) approved by the state’s Economic Investment Committee. Over the course of the 12-year term of the grant, the project is expected to grow the state’s economy by $1.7 billion. Using a formula that predicts new tax revenues generated by the 330 new jobs, along with a company investment of $485 million, the JDIG agreement has authorized the potential reimbursement to the company of up to $5,132,700, spread over 12 years, provided targets are met.
Huber Engineered Woods
Noxubee County, Mississippi
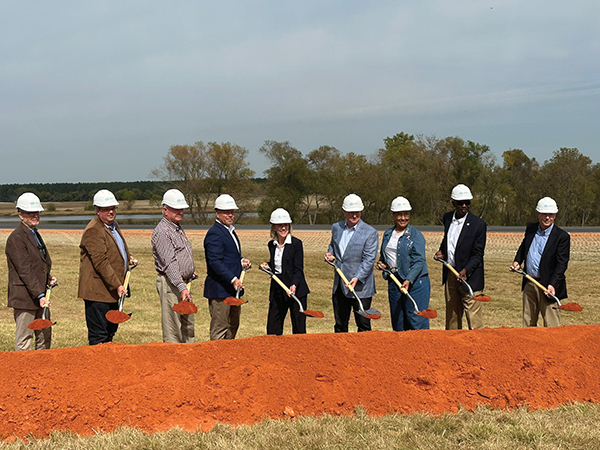
In June of 2023, building products manufacturer Huber Engineered Woods LLC (HEW), a subsidiary of J.M. Huber Corporation, announced plans to build a new oriented strand board (OSB) facility in Noxubee County, Mississippi. The $418 million plant is expected to increase the company’s production of innovative ZIP System and AdvanTech structural panels. The manufacturing facility is will provide more than 150 direct new jobs to Noxubee County and surrounding areas, while offering a sustainable solution to use abundant smaller diameter timber in the region, a move that will benefit landowners, businesses and residents.
The Shuqualak location will be HEW’s sixth mill in the U.S. The new mill will expand HEW’s current production footprint, which is comprised of five facilities located in Georgia, Maine, Tennessee, Oklahoma and Virginia. HEW’s manufacturing operations support the growing needs of single-family, multi-family and commercial builders along with select industrial materials markets. Product distribution is supported through a nationwide network of building products dealers and distributors.
The new facility will produce HEW’s panel products that have improved the way homes and multi-family projects achieve air and water management in roof, wall and subfloor assemblies. It will be located on approximately 550 acres and will feature some of the most advanced processes and technologies available for manufacturing operations. The facility will be designed to minimize its environmental footprint, maximize energy and water efficiency and optimize the use and yield of raw material inputs.
To help secure the project, the Mississippi Development Authority (MDA) certified the company for the Advantage Jobs Rebate Program, which is designated for eligible businesses that create new jobs exceeding the average annual wage of the state or county in which the company locates or expands.
“After considering multiple locations for what will be our most efficient and sustainable facility, we have decided to invest in and partner with Shuqualak, Mississippi, and the broader Noxubee County region,” said HEW President Brian Carlson. “We are excited to provide new jobs to the area and will build a world-class workforce by leveraging the diverse talent in the surrounding communities. In line with our commitment to sustainability and environmental stewardship, we have already started our permitting process in Mississippi. We look forward to continuing to work in partnership with state, local and tribal stakeholders as we move forward to ensure our facility provides long-term benefits to the community.”
Nel Hydrogen
Wayne County, Michigan
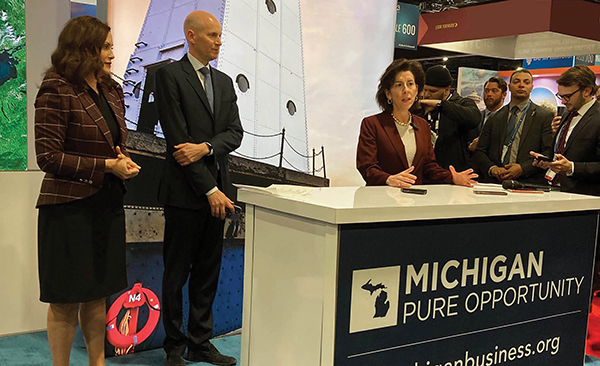
In January 2023, Michigan’s Governor Whitmer met with European companies during her first economic investment mission to Norway and Switzerland, which focused on attracting job-creating business investments, particularly in Michigan’s next-generation of automotive manufacturing and clean energy independence ecosystem.
The visit paid off: in September 2023, Norwegian hydrogen company Nel Hydrogen announced plans to build a new gigafactory in Plymouth Township, Michigan. The automated gigafactory, which will support the development of electrolyzer technology for green hydrogen production, will create more than 500 jobs and represents a total investment of more than $400 million into the local community. The announcement builds on Michigan’s leadership in advanced manufacturing and clean energy.
Through electrolysis, hydrogen can be produced from water and renewable energy; as the most abundant and lightest element in the universe, hydrogen can play a significant role in accelerating Michigan’s clean-energy transition away from fossil fuels.
The project will be supported in part by a $10 million Michigan Business Development Program grant. The MSF board also approved a 15-year, 100-percent State Essential Services Assessment Exemption Request, valued at up to $6.25 million, in support of the project.
The new 507,000-square-foot manufacturing facility will be used to manufacture Proton Exchange Membrane and Alkaline hydrogen electrolyzers and is expected to be a full greenfield build constructed specifically for Nel Hydrogen.
Nel Hydrogen considered several states across the country before choosing Michigan for its new manufacturing facility. At the time of the May announcement, Nel Hydrogen CEO Håkon Volldal said the company chose Michigan thanks to the engagement from Governor Whitmer, in addition to what the state could offer, from its highly skilled workforce and financial incentives to the collaboration among the state’s universities, research institutions and strategic partners.
“Plymouth Charter Township is an ideal location for Nel,” said Volldal. “Here, we have access to a highly educated workforce, universities and research institutions, and we are close to our collaborating partner, General Motors. In addition, the government and the authorities of Michigan have provided a very attractive financial support package for us.”
Viega, LLC
Portage County, Ohio
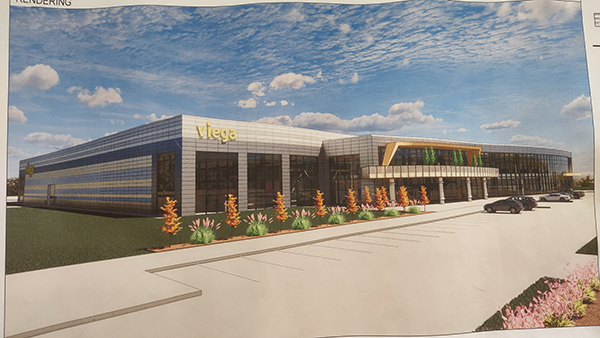
In its first-ever economic development incentive agreement with a manufacturer, Shalersville, a tiny town of 5,245 people located in Portage County, Ohio, landed a foreign direct investment project from German-based pipe and valve manufacturer Viega, LLC. Multiple incentive tools were layered together to create an attractive package to secure the project, despite competition from sites in Virginia, Pennsylvania and Kansas. In total, more than $265 million in investment is planned, representing the largest single investment in Portage County in decades.
The company recently broke ground on the first of several phases for its complex. Viega will begin by constructing a new 180,000-square-foot manufacturing facility with 41 jobs. Phase II will create a distribution center and Phase III will create an experience center to showcase its product line to customers and train them on proper use. In total, the company plans to build between 800,000 to 1,000,000 square feet of new industrial space and create more than 100 jobs by 2030. Leadership plans to invest in technology are expected to make the entire facility 100 percent carbon neutral by 2035, including a potential metal foundry.
What helped Shalersville attract the project was some intensive research on workforce skills and availability. While Shalersville is small and rural, the site boasts immediate access to Interstate 80. With this transportation amenity, the Township was able to demonstrate that a trained workforce for their exact six-digit NAICS code already existed and could commute to the facility within a half hour. By using data from the Bureau of Labor Statistics, the team demonstrated how Greater Cleveland Metro had the third highest concentration of metal valve and pipe fitting manufacturing workers in the U.S. They further proved that there was ample slack in the labor market in nearby bigger cities like Cleveland, Akron and Youngstown so that Viega could hit the ground running.
As a result of a partnership with the neighboring City of Streetsboro, Shalersville will now be able to collect income tax from Viega and approximately 100 employees. The Viega announcement has also shifted attitudes about the future of Shalersville. A majority of the residents left the township daily to commute to Akron or Cleveland for work, but now have options to work where they live. In addition, the project’s new, green infrastructure will allow Viega to meet its goal of being carbon neutral by 2035.
Additionally, the closing of an FDI project has helped to kickstart an interest in the remaining acreage of the Turnpike Commerce Center. A one million-square-foot industrial speculative building is nearing completion and will house additional employers who are attracted to excellent access to the interstate and quality workforce.
“Securing Viega’s investment was a monumental task,” said Patrick O’Malia, the Economic Development Director of the JEDD. “We faced competition from several states and had to bring in a lot of partners to help create the right incentive package that was acceptable to both the company and the elected officials who were very new to tax abatement.”
Bauducco Foods
Pasco County, Florida
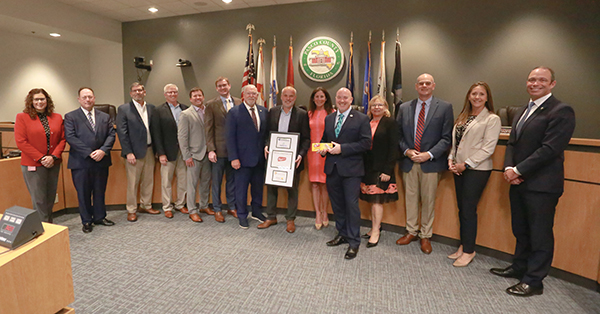
Bauducco is a Brazilian multinational company established in 1950 by an Italian immigrant. It is now one of the fastest growing cookie companies in the U.S., manufacturing baked food products such as biscuits, wafers and breads. The Bauducco brand is sold in all 50 states and has five manufacturing plants in Brazil, with the capacity to produce more than 400,000 tons of baked goods annually with over 8,000 employees worldwide.
Its newest project, in Pasco County, Florida, will see the construction of a new $233 million state-of-the-art facility that will ultimately create over 600 new jobs. The company reviewed 160 sites in seven states before it chose Pasco County. Enterprise Florida, now SelectFlorida, and the Florida Department of Transportation’s trade mission to Brazil in early 2023 helped fortify Florida as the state of choice for Bauducco by demonstrating a favorable business climate, well-developed transportation infrastructure, reliable supply chain and robust history in the agricultural industry.
The project is noteworthy due to the partnership between government and private partners to secure the investment. Local government and partners, including Duke Energy, invested significant resources, time and financial support into the Zephyrhills Airport Industrial Park Ready Site to create an industrial-ready property that offered significant benefits to Bauducco.
Bauducco is bringing manufacturing jobs to an area of the community where residents typically had to leave the county for employment. The company, its partners and state agencies indicated they are all committed to developing and maintaining a long-term relationship to continue to help Bauducco grow and succeed in its new home. Company CEO, Stefano Mozzi, stated that he and his team will be very engaged in the community and that they are encouraged by all the support they have received thus far.
“Creating a site readiness program isn’t new in the economic development world; however, what is crucial to making the program successful is having all of your partners and property owners working together with the same mission of creating new opportunities for our community,” noted Bill Cronin, President and CEO of the Pasco EDC. “The Ready Sites Program has become successful thanks to those public/private partnerships and the commitment and trust of the property owners to market their land for industrial development. We look forward to continuing to grow our relationship with Bauducco and welcoming them home to Pasco County.”
According to an economic modeling report completed by Tampa Bay Regional Planning Council, in addition to the 600 planned new jobs, there will be an indirect/induced employment number of 494 jobs, a gross county product of $72.1 million, an output of $149.9 million and personal income of $38.5 million.
Richardson International
Shelby County, Tennessee
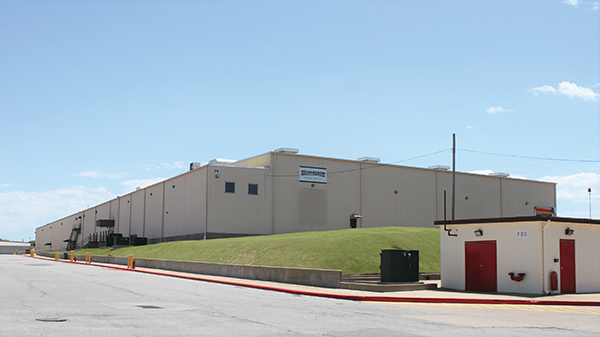
Agriculture and food processing company Richardson International announced plans in 2023 to undertake a transformative project in Memphis that exemplifies the company’s commitment to innovation, sustainability and community support. The company, headquartered in Winnipeg, Manitoba, is Canada’s largest agribusiness with more than 3,000 employees, and already has a presence in Memphis. In 2019, Richardson International expanded its operation in the city with the strategic acquisition of Wesson Oil.
The centerpiece of Richardson’s newest project is a $220 million investment aimed at upgrading and modernizing its Wesson Oil plant located in Midtown Memphis. The multiphase initiative, which will create 100 new jobs and retain 105, involves replacing the existing refinery at 1351 Williams Avenue with a state-of-the-art facility that will significantly enhance production and refining capacity. The new refinery aligns seamlessly with Richardson’s mission to meet customer demands and address the burgeoning global need for vegetable oil.
What sets the project apart is not only its scale but also its dedication to responsible and sustainable business practices. The modernization efforts are expected to drive improved efficiencies, resulting in substantial reductions in water, energy and wastewater volumes. Richardson’s commitment to sustainability aligns with contemporary business values, making it a standout candidate for recognition in award categories that prioritize environmental responsibility.
Richardson International’s investment in Memphis is not just a business endeavor; it is a testament to the company’s long legacy of community support, said the company. Darrel Sobkow, the Executive Vice President of Richardson International, expressed pride in the company’s history of investing in and supporting communities. Pending approval of local programs, Richardson International is poised to contribute to the growth of the Greater Memphis region, committing to maintaining its manufacturing and distribution presence in the U.S.
The area’s status as a global logistics leader, coupled with its concentration of advanced manufacturing companies, positions Memphis as an ideal location for Richardson’s ambitious project. The Greater Memphis Chamber, represented by President and CEO Ted Townsend, celebrated the investment by Richardson International, recognizing the company’s international stature and contribution to the Digital Delta region’s development. (The Digital Delta refers to an eight-county, tristate region dedicated to technology-driven development, advanced companies, diverse human capital and future-ready infrastructure.)
“EDGE’s economic incentives continue to be the tipping point for companies considering expansion,” said Al Bright, Board Chair, Economic Development Growth Engine for Memphis and Shelby County (EDGE). “When Richardson contacted us about this possible growth opportunity, EDGE was eager to offer our assistance in making this important investment possible, securing quality jobs for over 100 employees and a commitment by the company to support minority and women business enterprises.”
Samkee Corp.
Macon County, Alabama
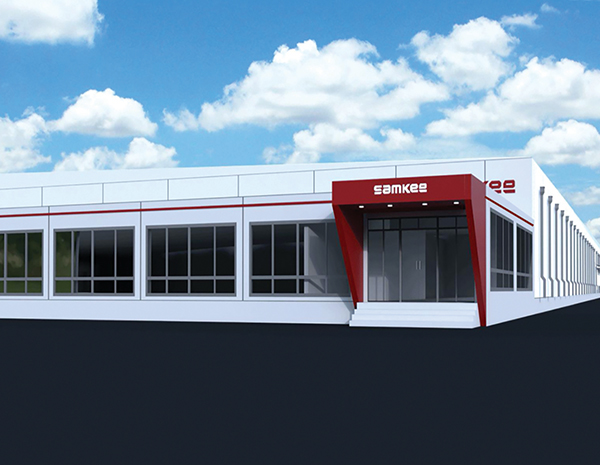
Since 2015, foreign companies have invested over $2 billion in growth projects in Alabama’s rural counties, with auto-related projects accounting for a large share of the total. Samkee Corp., a major South Korean automotive supplier, announced plans in early 2023 to invest $128 million to open its first U.S. factory in Alabama through a project that will create 170 jobs in Tuskegee, providing a significant economic boost for Macon County.
The new manufacturing facility will be located in the Tuskegee Commerce Park, where Samkee will become the city’s first auto parts manufacturer, and will serve as a Tier 1 supplier to Hyundai Motor Co. The new jobs will pay an average wage of just over $20 an hour, according to the Alabama Department of Commerce.
Samkee’s manufacturing plant is expected to have a significant economic impact on rural Macon County, according to an analysis by the Center for Business and Economic Research (CBER) at the University of Alabama. The center’s analysis has predicted that the Samkee factory will generate $140.2 million in annual economic output in Macon County, contributing over $37 million to the county’s GDP while also generating $1.3 million per year in taxes.
Founded in 1978, Samkee specializes in high-pressure die-cast aluminum components, including parts for engines, transmissions and electric vehicles, along with alloys. The company currently operates factories in South Korea and China, and now Alabama.
Joe Turnham, director of the Macon County Economic Development Authority, said local support for the project includes site work in Tuskegee Commerce Park, upgrades to the water and sewer system, and the installation of a new power substation.
“Samkee appreciated the local assets, spirit of cooperation and friendship developed over time with Macon County,” said Turnham. “We have strived with our stakeholders in a team effort to meet Samkee’s needs. We will remain partners going forward to see that they have a successful construction and manufacturing launch and future growth in the North American market. This is obviously a big win for our community and its citizens.”
Brenda Tuck, Rural Development Manager for the Alabama Department of Commerce, noted that Samkee’s investment project signals that the state’s rural counties remain a magnet for foreign direct investment, particularly within the auto industry.
Star Scientific
Bernalillo County, New Mexico
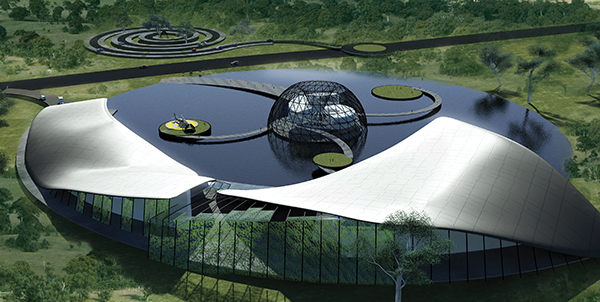
Star Scientific is the company responsible for the development of the patented HERO catalyst, a chemical catalyst that rapidly turns hydrogen and oxygen into industrial-scale heat without burning the gases or generating greenhouse gases. The only other output from this process is pure water. The use of this technology instead of a coal-fired boiler within an existing power plant would cut emissions.
In October 2023, Star Scientific Ltd. Global Group Chair Andrew Horvath announced that the Australia-based green hydrogen research and development company had chosen Albuquerque, New Mexico as the location for its first North American operation.
The $100 million project is expected to create more than 200 jobs at the complex, which will include 7 to 10 buildings for administration, design, testing, manufacturing as well as laboratory research. The New Mexico facility will be Star Scientific’s first manufacturing facility in North America and will expand the company’s global manufacturing footprint, which currently includes facilities in Australia and Switzerland.
The New Mexico facility will mirror the facility in Australia and will serve customers in the U.S., Canada and, initially, South America. The technology produced at this facility will be used for off-grid power, desalination and heavy industrial production where high temperatures are needed. In addition, the company will continue development of greenhouse-gas-free process-heat systems for industry and stand-alone power systems while continuing research on other projects.
As part of the negotiations, the New Mexico project stakeholders took a whole-of-government approach to manufacturing, logistics, higher education and research that outlined the important role of hydrogen in the state’s future. The New Mexico stakeholders also highlighted planned and ongoing investments in workforce housing, education incentives and lifestyle and leisure infrastructure.
Star Scientific negotiated with the state Economic Development Department for an incentive package that would include assistance from the Job-Creation Fund under the Local Economic Development Act (LEDA) as well as assistance for job training. Once operating, Star Scientific would also qualify for manufacturing tax credits and for hiring high-wage workers.
“From the very earliest conversations, the officials in New Mexico outlined their long-term commitment to hydrogen and the benefits of their state for a company such as Star Scientific,” said Star Scientific Ltd. Global Group Chair Andrew Horvath. “We were impressed by their whole-of-government approach to manufacturing, logistics, higher education and research and their vision for the role that hydrogen will play in their future. We were equally impressed that they had holistically planned important human details such as housing for families who will work at our facility, education incentives for their children and lifestyle and leisure infrastructure. There is also an infectious ‘can do’ attitude which appeals to us as Australians very much.”
Manner Polymers
Jefferson County, Illinois
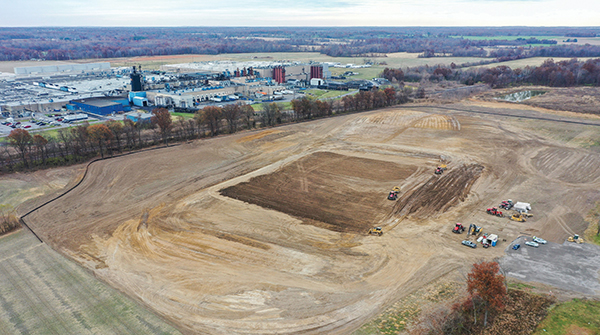
Image courtesy of Steve Murphy, Murphy Drone Services
Bolstered by a Reimagining Energy and Vehicles in Illinois (REV Illinois) incentive package, Manner Polymers announced plans in 2023 to invest $54 million and create more than 60 jobs in the Southern Illinois Region. Manner Polymers is one of North America’s largest flexible PVC compounders.
Manner Polymers’ new state-of-the-art facility will manufacture a wide array of PVC compounds, including automotive PVC compounds for use in electric vehicles and components for solar panels. The facility will be powered by a 15-acre solar field located on-site. The company’s new 80,000 square-foot Illinois facility will feature the most advanced manufacturing control systems available, with production expected to begin in the fall of 2025. Once in full operation, the new facility will increase the company’s production capacity by 100 million pounds, further strengthening the domestic supply chain for a variety of industries.
The City of Mount Vernon is known for its manufacturing and logistics specialties. Although home to a massive Continental Tire manufacturing facility that boasts over 100 acres under one roof and employs people from 176 different area codes, the city is relatively small at just under 15,000 people. Located precisely at the intersection of two of Southern Illinois’s busiest interstates (64 and 57) Mount Vernon has a daytime population that often swells to much larger.
In such a small community, the project’s rippling impact will be felt throughout the entire region. Not only will the company bring jobs to the area but the economic impact will influence the hiring of many more in related fields. Manner Polymers will be using Milano Railway Logistics — located about one mile north of the new plant — for its transloading needs. As a result, Milano will be hiring additional employees. Truck drivers and other employees will also be required. In addition, Mount Vernon expects to see an increase in banking deposits, healthcare/insurance needs and real estate purchases. While the region acknowledges that $54 million is not a jaw-dropping investment, its impacts will be felt widely in such a rural area.
Incentives by state and local economic development groups included improvement and extension of Fountain Place Drive, property tax abatement as well as sales tax waivers. The City of Mount Vernon established an Enterprise Zone within the city; and the site of the new manufacturing facility is located within this zone, allowing for further economic incentives.
“We extend our sincere gratitude to Manner Polymers for choosing Jefferson County as the location for their expansion. Their commitment to excellence and innovation has a direct and positive impact on our community,” said Tony Iriti, Executive Director of JCDC.
SanMar Corporation
Hanover County, Virginia
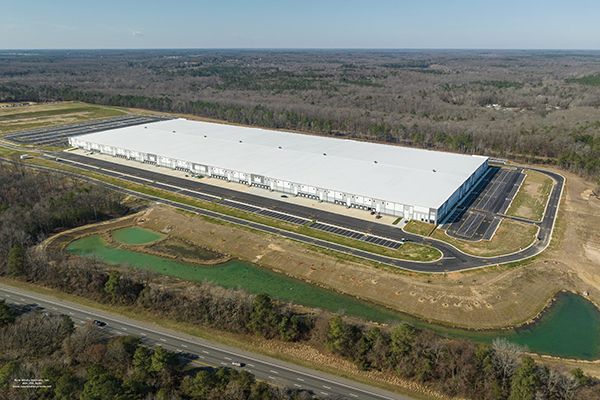
In March of 2023, SanMar Corporation, a supplier of wholesale accessories and apparel, announced plans to invest at least $50 million to establish a distribution operation in the East Coast Commerce Center in Hanover County. The 1.1 million-square-foot speculative distribution building will be SanMar’s largest operation, becoming the flagship center for the company’s East Coast distributions. Virginia successfully competed with North Carolina for the project, which will create up to 1,000 new jobs when the facility reaches full capacity.
The company contacted local officials in 2022 as they were interested in the already under-construction 1.1 million square-foot building at East Coast Commerce Center (ECCC). The Hanover economic development team met with Marty Lott, SanMar’s founder, and Jennifer Larson, the company’s HR Director, who were also looking at a similar-sized building under construction in North Carolina. Hanover East Coast Commerce Center was much further ahead. Before this meeting, SanMar had already engaged with The Port of Virginia as they wanted to shift significant volume to the mid-Atlantic.
SanMar worked closely with county staff over the next few months to ensure the building was operational. They also worked closely with other partners like Verizon for telecommunications and Virginia Natural Gas for heating. These issues were resolved, and the company signed a lease for the building.
The current population of Hanover is 105,537, with a total labor force of 57,163 (67.1 percent of the population). Creating 1,000 jobs will be a significant economic boost for a community of Hanover’s size. The economic impact of SanMar Corporation’s investment is nearly three times the jobs the company is creating. Indirect jobs are expected to total 1,124 and induced jobs will total 729 for a cumulative employment of 2,854. Cumulative labor income is nearly $228 billion with more than $469 billion in value added and nearly $810 billion in cumulative output.
“Whenever we look at a facility, of course we’re looking at logistics and the labor market, but we’re also really looking at the community and the culture, and the people who will be working in the building,” said SanMar CEO Marty Lott. “When we came here, we knew right away that this is a place we wanted to be. As we met and talked with people in the area, we knew this could be a great fit for us and for our future growth. We couldn’t be more excited to be here — to fill up this building, to build our team here, and to make this a home for a really long time.”
Independence Foods LLC
Buchanan County, Iowa
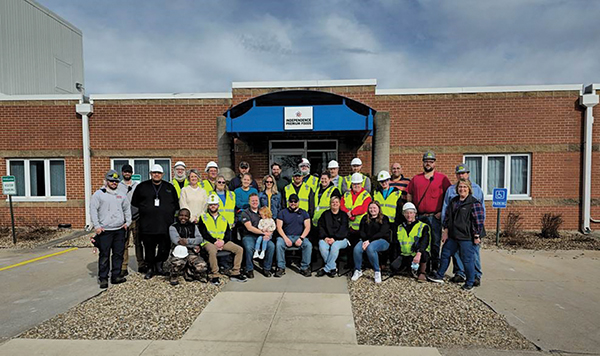
Image courtesy of Independence Foods
Nothing transforms a community more than a new venture quickly taking the place of a manufacturing facility that has closed, resulting in layoffs. Newly formed company Independence Foods LLC announced in late 2023 that it plans to revamp an existing facility in Independence, Iowa to manufacture a wide range of food products. The company purchased an existing pet food facility in the region and plans to make upgrades to accommodate new production capabilities and requirements. The project represents a capital investment of $14.8 million and is expected to create 229 jobs incented at a qualifying wage of $25.90 per hour.
The project was awarded $1.5 million in direct financial assistance through Iowa’s High Quality Jobs (HQJ) program as well as $300,000 in infrastructure and tax abatement incentives. Independence Foods worked with the Iowa Economic Development Authority, Buchanan County Economic Development Commission and the City of Independence to establish the project.
The project is truly a fairytale story for the community, region and state. The closing of General Mills’ Blue Buffalo facility would have had detrimental impacts – the WARN notice filed with the State of Iowa reported 211 employee layoffs.
Only a few months after the closure announcement, Independence Foods LLC was created, and filled a huge gap, recovering the previously lost jobs and occupying the food manufacturing space that was left behind. Food production is one of Iowa’s key strengths in advanced manufacturing.
“This transformative move not only marks a strategic business decision but also symbolizes the adaptive spirit of Independence,” noted Independence Mayor Brad Bleichner at the time of the announcement. “We welcome Independence Premium Foods with open arms, recognizing their commitment to repurpose and reinvigorate a facility with a storied history. This venture not only adds economic value but also reinforces our town’s resilience and ability to evolve. We are excited about the prospects of collaboration and growth as we embrace this exciting chapter in Independence’s journey.”
Boogook Georgia, LCC
Macon-Bibb County, Georgia
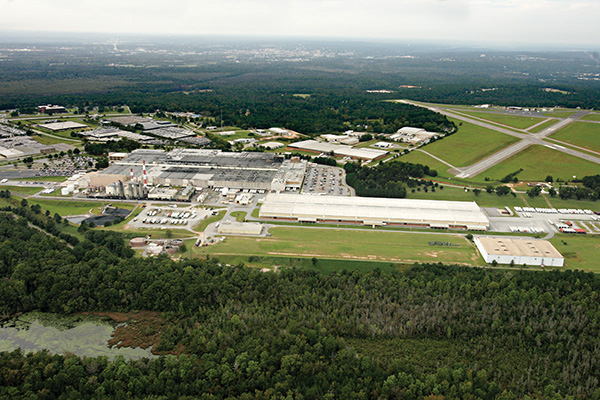
Image courtesy of CBRE
Boogook Georgia, LLC is a subsidiary of Boogook Industries Co., LTD, headquartered in Ulsan, South Korea. The company is a global leader in the automotive tube industry, specializing in automotive parts and materials that carry fluids within vehicle systems.
The company announced in 2023 that it is investing $6.8 million plus an additional $300,000 in leasehold improvements to support its operations in Macon-Bibb County. The company’s direct foreign investment enhances the automobile supply market in the Southeast, greatly augmenting the need for Korean automotive parts to manufacturers in the region. Boogook Georgia will be breathing new life into a massive industrial building that sat vacant in Macon for about 15 years.
The two million-square-foot property at 2600 Weaver Road long sat empty as previous owners tried unsuccessfully to find a single tenant to take over the plant. With its first facility in the U.S., Boogook Georgia’s investment into space at the former Brown and Williamson cigarette plant is a testament to the revitalization of the area.
Upon its opening later this year, Boogook Georgia will bring 80 full-time jobs, with further job growth anticipated in the future. These employment opportunities will provide the local community with professional roles in the automotive sector, spanning management, manufacturing, assembly, quality assurance and delivery functions that offer competitive paying jobs and careers in the automotive industry.
Having Boogook Georgia in Macon-Bibb County — the heart of the state — allows the distribution and utilization of products much more quickly than supply chain demands could accommodate in recent years.
Boogook Georgia LLC’s first U.S. facility breathes new life into the region, increasing the competitiveness and accessibility of the automotive industry statewide by specializing in steel and nylon tube manufacturing, making fluid-carry systems for brake, fuel, steering and exhaust lines. As Hyundai ramps up construction on its $5.5 billion electric-vehicle factory just off Interstate 16 near Savannah, the Macon-based Boogook Georgia plant sits two miles from that interstate. Hyundai and Kia are global customers of Boogook Georgia’s parent company, Boogook Industries Co. Ltd., and Boogook Georgia are positioned to provide diversified products and services for these automotive industry giants and others, strengthening the automotive industry presence in Central Georgia.
“The decision by Boogook to locate to Macon reinforces the importance and value of growing our automotive industry partners in the region,” said Stephen Adams, Executive Director of the MBCIA. “Middle Georgia is an extremely attractive and competitive area for these companies, and we’re excited to see how this industry becomes a key player in our future economic and job growth.”
The Shops at Sharp End
Boone County, Missouri
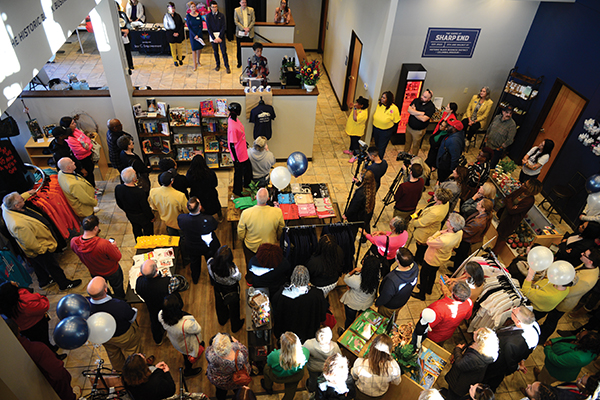
Columbia, Missouri’s Sharp End business district was a thriving business district from the early 1900s to the 1960s. It included restaurants, shops, meeting halls, barber shops, bars and more, making it a cultural heart of the area’s Black community. Sharp End was demolished in the 1960s in the name of “urban renewal.” The area proposed for “renewal” excluded houses on the north side (owned and occupied by whites), but included houses on the south side, occupied by Black families. Sharp End was part of this area.
Now, a new retail incubator called “The Shops at Sharp End” is slated to become a transformative project with a clear vision to create a collaborative space for innovative businesses while actively reducing barriers for underrepresented entrepreneurs. Its commitment to diversity, equity and inclusion, coupled with a comprehensive program offering workshops, mentoring and access to resources, distinguishes it as a community-driven initiative. Given the history of the Sharp End and the way it can change the lives of entrepreneurs, the initiative’s tagline is: Honor the Past – Shop the Future.
By aiming to enhance the local entrepreneurial climate, retain businesses and prioritize minority enterprises, the project not only contributes to economic growth but also fosters a thriving, inclusive community.
The project involves about $70,000 in one-time costs for development, with ongoing costs designated for lease and utilities, scholarships, staff and equipment and marketing and promotion. It was led by the Regional Economic Development Inc. (REDI), which is providing infrastructure improvements, equipment and retail display purchases as well as leases and utilities. Central Missouri Community Action (CMCA) will act as retail manager for staffing, and the Downtown CID will provide marketing, branding and promotion to drive customers to the space.
The number of jobs created through this project is ongoing because it focuses on reducing barriers to entry for low-to-moderate-income individuals and minoritized populations. These individuals can start new retail enterprises, while becoming financially viable, freestanding and successful business owners.
The implementation timeline spans from immediate actions such as space renovations and equipment purchases to long-term plans for transitioning the program to a permanent agency for ongoing operations. The project’s impact on the region is anticipated to be substantial, contributing to a thriving local economy, job creation and the development of a more diverse and vibrant retail sector.
“From the moment we began talking about this idea, people were excited, supportive and invested in making this opportunity happen so we could grow entrepreneurs in our area,” said Nickie Davis, executive director of the District Downtown CID. “When people learned about why we chose the Sharp End, a historic Black business district, they knew we were doing something important for the community.” T&ID
Related Agencies
- Economic Development Partnership of North Carolina
- JobsOhio
- Greensboro Chamber of Commerce
- Noxubee County Economic and Community Alliance
- Michigan Economic Development Corporation
- Portage County Department of Economic Development
- Pasco Economic Development Council
- Greater Memphis Chamber
- Macon County Economic Development Authority
- Albuquerque Economic Development
- Jefferson County Development Corporation, IL
- Buchanan County Economic Development Commission
- Macon Bibb County Industrial Development Authority
- Columbia Regional Economic Development Inc.