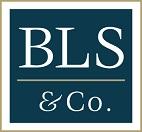
The global economic indicators that led the Boston Consulting Group (BCG) to predict a shift of manufacturing operations from China to the U.S., otherwise known as “reshoring,” are seemingly coming to fruition. The BCG study Made in America, Again, completed in 2011, concluded that for many goods destined for North American consumers, the economics for manufacturing in the U.S. would ultimately become competitive to China, reaching a “tipping point” around 2015.
The study predicted that in many cases, companies in the following sectors would shift production back from China or choose to locate new investments in the U.S.:
-
Transportation goods
-
Computers and electronics
-
Fabricated metal products
-
Machinery
-
Plastics and rubber
-
Appliances and electrical equipment
-
Furniture.
So, what’s the rationale for reshoring? Higher wage rates in China and increasing costs for global transportation of goods mean shrinking price advantages for producing products overseas. Being closer to U.S. customer markets means production can react faster to changing consumer preferences, fulfill orders faster and speed development of new products.
Today, costs to ship ocean freight from China to the U.S. are higher than ever, with further rate hikes on the horizon. Delivery times also have been jeopardized by both natural and man-made risk factors. The longshoremen’s union strike at the Port of Los Angeles/Long Beach is the most recent example of delivery delay issues, which resulted in products stuck sitting on ships in the harbor for weeks while store shelves dwindled.
From a labor standpoint, Chinese wage rates also have risen at a swift pace over the past five years. According to the National Bureau of Statistics in China, average yearly wages in manufacturing have increased by over 50 percent since 2011.
Naysayers to the U.S. reshoring trend cite Mexico as a more likely manufacturing location – closer to the U.S. market than China, with lower cost labor compared with the U.S. But the mammoth retailer Walmart is swaying the market: in 2013, the company announced it would spend an additional $250 billion dollars on “Made in the USA” products over the next 10 years. The purpose of the program is multifold:
-
Sourcing products closer to demand allows for faster response to seasonal trends
-
Consumer demand for products labeled “Made in USA” is rising
-
With over 5,000 stores across the U.S., Walmart realized it can increase consumer buying power in its stores by creating manufacturing jobs nearby.
-
Walmart recently announced a re-commitment to its Made in USA Program, and other major retailers are following suit. Companies are responding by reshoring their operations. Here are some recent examples:
-
HanesBrands recently announced it would bring 120 new jobs to Clarksville, Arkansas, for a new hosiery production line to be moved from Honduras
-
Element Electronics has built the first U.S. television assembly plant in decades in Winnsboro, South Carolina, and will employ 500 by 2018.The parts are still sourced offshore, in large part because the supply chain for televisions in the U.S. was non-existent after the industry disappeared, but the company is working to identify U.S. suppliers
-
Last fall, global bicycle supplier Kent International began production of U.S.-made bicycles called Bicycle Corporation of America (BCA) at a new facility in Manning, South Carolina, that will employ 200. After years of sourcing products in China, BCA represents the first mass-production bicycle facility in the U.S. in more than 15 years. In addition to Walmart, BCA also is supplying products to Toys R Us, Amazon and other sporting goods retailers.
Despite the favorable economics and recent success stories, some companies that want to bring manufacturing back to the U.S. still need support services to make it happen. Supply chains for some industries that in large part left the U.S. years ago, such as textiles, have to be rebuilt. Labor skill sets must be established for new manufacturing processes, many of which are automated and require skilled labor for operating and maintaining equipment. Financing programs with flexible terms need to be created to assist with startup costs.
The conditions are right for 2015 to be the start of the “tipping point” for U.S. reshoring, but local communities and states across the U.S. will need to help create the right local economics to realize the trend’s full potential.