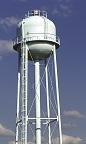
When evaluating a site and its surrounding community in order to assess its potential as a suitable location for building a new manufacturing facility, there are several critical aspects to consider. Certainly, accessibility is key; one must study the site’s geographical location with regard to airports, highway systems and navigable ports, all of which are vital to many processes from the smooth reception of raw materials to the distribution of finished product.
Another key consideration is the labor force that is available within the community. The quantity and quality of labor, and the ongoing availability of appropriately skilled workers in the foreseeable future, is certainly an important factor in the initial success and ongoing vitality of the manufacturing endeavor as a whole.
A third key consideration is the availability and quality of basic utilities. Basic utilities necessary for use in manufacturing include electricity, natural gas, telecommunications and water and wastewater/sewer services. While the reliability of the electric power supply, the availability of natural gas and the service providers and redundancy of telecommunications are all extremely important to operations, water and wastewater cost, availability and service play an equally important role in site selection for today’s manufacturing sector.
Water: Key to Manufacturers
While water is key to survival for most everything on the planet, it is comparatively vital to manufacturers. Twenty-two percent of the world’s water supply is used for industry1, and every manufactured product uses water as part of its production process. The number of ways manufacturers use water during their processes are myriad: for fabricating, processing, washing, diluting, cooling or transporting a product down the production line. Water may also be incorporated into a product or used for sanitation needs within the manufacturing facility.
In America, industrial facilities withdraw over 18.2 billion gallons of fresh water per day.2 While factories have actually reduced water use by 30 percent since 1985 due to the implementation of production efficiencies, the ever-increasing demand for products and services keeps manufacturing water usage a reliable constant.
Traditions and Alternatives
Generally, most manufacturers rely on municipal water systems to provide all water needs for processing and potable uses. However, due to increased water scarcity in many areas and the brisk urbanization of many regions, alternatives to using municipal water systems are growing, such as the usage of reclaimed water. Sources of reclaimed water are many: harvested rainwater, onsite stormwater, graywater, water discharged from purification processes and captured condensate from air-handling units. The use of reclaimed water can support the demands of a variety of industrial processes, and is a sustainable alternative solution for those industries that wish to reduce their environmental footprint.
Tapping into a Community
If a manufacturer is planning to tap into the municipal water system for its needs, a critical evaluation must first take place to assess the utility’s suitability. Using the criteria of availability, capacity, cost and quality, a manufacturer can more clearly decide whether the site and community is one that can support its water needs now, and that will increase with future growth.
Availability. Municipal water sources generally take two forms: surface water and ground water. Surface water comes from streams, rivers, lakes, reservoirs, wetlands and estuaries. Ground water requires a well system to pump the water to the surface for use. In the U.S., surface water is the source for around 83 percent of total industrial water usage, whereas groundwater accounts for around 17 percent.3 Once the water source has been determined at the municipal level, it is wise to then determine the size of the water main that will be delivering the municipal water to the manufacturing site. For most industrial use, a 10- to 12-inch water main will ensure proper flow to the site, enough to deliver a desirable average of 1,000 gallons per minute, figuring in peak usage times. A good understanding of the placement of water lines throughout the municipal network will ensure necessary flow and service redundancy critical to most manufacturers.
Capacity. An assessment of the community’s water capacity should take into account its typical capacity during daily water usage and, more critically, the average excess capacity that’s typically available for use. A close look at the community’s past history with regard to reserve capacity, past curtailments, water shortages and even depletions can determine if the municipal system is the right fit for a new manufacturing operation. Most communities should have reserve capacities between 20 to 25 percent of their peak daily usage. This will ensure growth for new manufacturing operations locating in the community and for current manufacturers to expand. While assessing capacity, it is also wise to assess whether peak usage times have an effect on water quality and contaminant issues, as can be the case.
Costs. Costs involved with using the municipal water system are of primary importance when assessing the suitability of a manufacturing site. Costs can take the form of one-time fees, service charges and wastewater service charges. One-time fees may be for initial connection to the water line, as well as impact fees for usage. Ongoing water service charges are commonly based on thousands of gallons of water used, either on a monthly or quarterly basis. Wastewater service charges take into account the amount and composition of the wastewater that is discharged by the industrial facility back into the community’s sewer system.
Since water usage costs can be affected by a number of factors in the community, and can vary widely from location to nearby location, it is wise to do one’s due diligence in discovering specifics. In areas that face chronic water shortages, it is not uncommon to find that the community will mitigate impact on their water supply from industrial usage by collecting significant one-time high-impact fees, the proceeds of which can be reinvested into the community. Other factors related to costs (which vary widely among communities) are age and condition of the water system, along with current and planned expansions to the system affecting its efficiency, growth rate of the community and its past ability to expand the system to address that growth, the history/volatility of past service charge increases, and the community’s projections for any future increases.
Quality. Contamination of the municipal water supply in some communities has recently received much notoriety. Water to be used in manufacturing should be no less scrutinized with regard to contaminants, in order to maintain the integrity and efficacy of the manufacturer’s production processes. It is wise to have a formal water quality analysis done to specifically determine the chemical content of a potential community’s water, including microbiology testing for legionella, fecal organisms, pathogens and other indicators, as well as physical and chemical testing for pH level, metals, turbidity, minerals, color and anions. The analysis should identify not only the presence of, but also the density of organisms and dissolved minerals that could potentially interfere with industrial processes and purposes.
Handling Wastewater/Effluent
Effluent is defined by the Environmental Protection Agency as "wastewater — treated or untreated — that flows out of a...plant, sewer or industrial outfall.”4 For industrial operations, there are two ways of transporting effluents away from the manufacturing facility and to a municipal treatment plant: gravity-feed systems allow effluent to be conveyed via gravity to the dispersal area, with no pumping required; pumping stations move effluents to higher elevations in order to allow transport further via the flow of gravity. A thorough site selection process will consider which type of system will be required to handle the facility’s effluents, as well as the total system capacity, average daily usage, peak daily usage and excess capacity, all measured in million gallons per day (MGD).
Communities vary with regard to whether they will accept untreated effluent, as well as how much and what type of untreated effluent they will allow to flow into their treatment plant. These values are dictated by the community’s sanitary sewer ordinance manual, which outlines what is acceptable, and is based on EPA and state guidelines. Additional costs or surcharges are often imposed by a community based on effluents discharged by a company. These costs are typically based on the measured value of Biochemical Oxygen Demand (BOD) 5, which is the amount of dissolved oxygen required during the treatment process to biologically decompose any organic matter in the wastewater, as well as the measured value of Total Suspended Solids (TSS), which is the total amount of materials in the wastewater. Site selection should include a thorough discovery of maximum allowable limits for effluents in general (measured in mg/l) as well as any surcharges for exceeding limits in terms of BOD, TSS and other effluents. An estimated, itemized monthly bill based on both wastewater usage and effluent production (including all applicable state and local taxes) is extremely helpful in evaluating a site for facility location.
Whether one is evaluating utility services for water or wastewater, the final step in the process should involve requesting a commitment letter from the municipal providers. These letters should include confirmation of the specifics discovered during the evaluation process, including the community’s ability to meet usage requirements, confirmation of water and wastewater line size and locations on the site, confirmation of total system capacities including average daily usage, average peak usage and excess capacity and a variety of other criteria. In both cases, it is also important that the commitment letter include projections regarding potential increases in costs for the near future, to ensure that the site and its utilities remain adequate as the manufacturing business continues to grow.
Site Selection: a Key Utilities Checklist
The complexity of site evaluation for manufacturing cannot be overstated and the key utilities of water and wastewater are among the most important aspects of that process. In order to simplify the process, the following checklist can be a guide to ensuring that a thorough, detailed evaluation is conducted.
1. Water
a) Capacity and source
b) Line size at site
c) Water pressure
d) Water flow
e) Improvements to system
f) Monthly estimated costs
g) One-time costs
h) Water analysis report
i) Commitment letter
2. Wastewater
a) Capacity
b) Line size at site
c) Improvements to system
d) Monthly estimated costs
e) One-time costs
f) Effluent limits
g) Effluent surcharges
h) Sewer ordinance manual
i) Commitment letter
Followed diligently, a key utility evaluation of water and wastewater resources will uncover whether or not the proposed site truly holds potential for that new manufacturing facility. As water is an essential element to life here on Earth, the proper handling of it will add vitality to the manufacturing operation once up and running — and into the future.
References
1http://www.unwater.org/downloads/Water_facts_and_trends.pdf
2 http://www.gracelinks.org/285/the-hidden-water-in-everyday-products
3 http://water.usgs.gov/edu/wuin.html