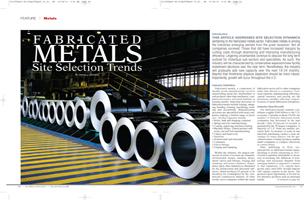
This article addresses site selection dynamics pertaining to the fabricated metals sector. Fabricated metals is among the industries emerging earliest from the great recession. Not all companies survived. Those that did have increased margins by cutting costs through downsizing and improving manufacturing efficiency. Lingering uncertainties continue to obscure the long term outlook for individual sub-sectors and specialties. As such, the industry will be characterized by conservative expansion/new facility investment decisions over the near term. Nonetheless, the industry will gradually add new capacity over the next 18-24 months. Beyond that timeframe physical expansion should be more robust. Importantly, growth will occur throughout the U.S.
Industry Definition
Fabricated metals, a component of durable goods manufacturing, involves transforming metal into intermediate or end products other than machinery, computers/electronics, and metal furniture or treating metals. Important processes in fabricated metals include forging, stamping, bending, forming, machining, welding and assembling. Manufacturing processes are specialized with most companies making a limited range of products. Product segments include:
Boiler, tank and shipping container
Spring and wire manufacturing
Coating, engraving and heat treating
Machine Shops; Turned product and screw, nut and bolt manufacturing
Cutlery and hand tools
Hardware
Architectural and structural
Containers
Valves/fittings
Forging and stamping
Within the industry, the largest subsectors in terms of revenue are ornamental/structural metals, machine shops, metal valves and fittings, forging and stamping, and metal containers. Dependence upon other industries is illustrated by the architectural and structural sub-sector, which produces 95 percent of its inventory for consumption by the commercial construction industry. In other words, most companies within the metal fabrication sector sell to other companies rather than directly to consumers. Technical expertise, manufacturing efficiency, capital intensity, and pricing are the prominent variables affecting competitiveness of metal fabrication enterprises.
Industry Size/Growth
The fabricated metals industry contributes roughly $340 billion to the U.S. economy. Currently at about 55,000, the number of domestic fabricated metals companies has decreased in the past decade. Only 20 percent of revenue is generated by the 50 largest companies. A majority of U.S. firms are smaller, privately held. Economies of scale in raw materials purchasing creates a clear advantage for major players, but the specialized nature of many products enables small companies to compete effectively in certain niches.
After stabilizing in 2010, revenue/profits in fabricated metals manufacturing is slowly advancing in 2011. Growth is partially attributable to inventory re-stocking, but diffusion of technology and increased demand from emerging markets is expected to continue to fuel expansion. U.S. exports have grown since mid-2009, though imports still outpace exports in the sector. The greatest export opportunity is for less labor-intensive products such as structural metals.
Among mega players in fabricated metals industry are:
Ball Corporation
Flowserve
Mueller Industries
Snap-on
The Timken Company
Illinois Tool Works
United States Steel
Smith International
Crown Holdings
General Cable Stanley Black & Decker
Silgan Holdings
Harsco
Crane
Griffon
Barnes Group
Kaiser Aluminum
NCI Building Systems
BWAY Holding
Century Aluminum
Employment
Industry subsectors that account for the greatest proportion of industry employment are:
Machine shops: 16 percent
Sheet metal manufacturing: 8 percent
Fabricated structural metal manufacturing: 7 percent; and
Precision tuned metal manufacturing: 6 percent
Skilled crafts and semi-skilled production account for the bulk of employment within the industry. Total industry employment approximates 1.3 million. The top three occupational categories are:
120,000 machinists
90,000 welder/cutters
75,000 assemblers
Geographic Concentration
The industry has a notable presence in most states. However, the densest concentrations are found in the following geographies:
Rust Belt (Ohio, Illinois, Pennsylvania, Wisconsin, Michigan, Indiana, New York, Minnesota): large population base; density of consuming industries; and a skilled workforce;
Southeast (Texas, Alabama, Mississippi, North Carolina, Georgia): strong population growth; energy production in some states; lower operating costs including wages in Right-to-Work states; and,
West (California): aerospace industry, proximity to Pacific Rim markets, and technological innovation.
Fabricated Metals Employment | % Fabricated Metals Employment | % State Workforce | |
U.S. | 1,300,000 | ||
Texas | 117,000 | 9.00% | 1.41% |
California | 117,000 | 9.00% | 0.97% |
Ohio | 95,000 | 7.31% | 2.28% |
Illinois | 89,000 | 6.85% | 1.89% |
Pennsylvania | 79,000 | 6.08% | 1.67% |
Wisconsin | 64,000 | 4.92% | 2.85% |
Michigan | 59,000 | 4.54% | 1.88% |
New York | 49,000 | 3.77% | 0.72% |
Indiana | 45,000 | 3.46% | 2.00% |
Minnesota | 37,000 | 2.85% | 1.71% |
Locational Tendencies
Fabricated metals firms are most likely to locate near other manufacturers, particularly those up or down stream in their supply chain. Once proximity has been defined other prime locational determinants include availability of requisite skills (e.g., CNC machine operator), labor costs, available building, highway linkage, transportation resources, electric power cost/reliability, union risk, moderate taxes and meaningful incentives.
An illustration of a new plant in this industry involves Middle River Aircraft. The company required proximity to Boeing and needed 200 mostly skilled workers. Consequently, the company selected greater Baltimore for its new production facility.
Another typical new manufacturing plant is Dennen Steel. The company will soon begin production in Iuka, Mississippi, of fabricated steel parts primarily for the motor vehicle market. Some 100 employees will work in the 50,000-square-foot facility. Distance to southern auto plants, labor supply/cost, transportation resources and utility infrastructure were important locational determinants.
Bonnybrook Steel is about to open a 110-person facility in central Missouri. The operation will serve a predominantly Midwest market. Here again market proximity, a qualified labor pool and moderate operating costs were key siting factors.
Company | Location | Product | Employment |
Sewon Precision | La Grange, GA | Automotive Stampings | 700 |
The Hamlin Companies | Garner, NC | Custom Metal Components | 250 |
Schuff Steel-Gulf Coast | Humble, TX | Steel Fabrication, Steel Pressure Vessels | 200 |
Supermetal Holdings | Rock Hill, SC | Steel Structures | 200 |
Quaprotek | Ripley, TN | Metal Parts | 120 |
Bonnybrook Steel Forms | Glasgow, MO | Steel Forms for Precast & Prestressed Mat. | 110 |
Dennen Steel | Iuka, MS | Fabricated Steel Parts | 100 |
Scot Industries | Auburn, IN | Steel Tube & Bar | 65 |
KMC Atlanta | Atlanta, GA | Ball Valves | 60 |
AMECO USA | Cleveland, OH | Fabrication of Engineered Products | 20 |
RJLK Holdings | Orangeburg, SC | Fabricated Metal Parts | Undisclosed |
A sampling of recent new facilities started by fabricated metals companies is shown in Exhibit 1. New fabricated metals plants vary in scale, but a prototypical operational profile follows:
1. Product: Shipping containers
2. Markets:
Primary 500 miles
Secondary 1000 miles
3. Raw Materials:
Steel, corrugated steel, aluminumFasteners, locking bars and corner fittings
Protective finishes and paint
4. Real Estate
10-20 acre sites
Building
100,000 SF
Room to double in size
6” reinforced concrete flooring
24’ ceiling height
Open column spacing
6+ truck docks
Rail siding a plus
5. Machinery and Equipment Investment: $10-20 million
6. Utility Consumption
Electric Power
1,500 KW
400,000 kWh
Natural Gas: 3500 MCF/month
Water: 0.2 MGD
Sewer: 0.1 MGD
7. Environmental
Minimal pollutants
Hazardous waste from
Heat treating
Painting
8. Employment
Category | Numbers |
Machine Operator | 60 |
General Laborer | 20 |
Packaging | 10 |
Shipping/Receiving | 10 |
Machinist | 15 |
Machine Maintenance | 5 |
Welding | 5 |
Quality Control Tech | 5 |
Engineer | 5 |
Supervisor | 10 |
Management | 7 |
Clerical | 8 |
Total | 160 |
9. Average Hourly Wage (production workers): $15.50
10. Fringe Benefits: 30 percent of payroll
11. Transportation services
Motor carrier
TL
LTL
Possibly rail for inbound
Within 75 minutes of a commercial airport
For some companies within 500 miles of a seaport (mainly for imported materials)
Looking Forward
Fabricated metals will be a growth industry for the U.S. While the industry will become more global, production will remain parochial due to supply chain dictates. These include proximity to customers and/or suppliers, delivery times, inventory costs and transportation costs. U.S. companies will continue expanding by serving a growing domestic market and exporting. Some corporations will establish new facilities offshore. But offshoring will be driven more by gaining market share than seeking a very low operating cost platform.
In the U.S., a shortage of semiskilled (e.g., CNC machine operator) and skilled (e.g., machinist) labor could constrict growth. Areas that can generate more throughput (i.e., students/graduates) in the machine trades will be winners in terms of attracting new fabricated metal plants.
Technology is rapidly advancing. Thus companies can benefit from industry/education partnerships that focus on the core needs of this industrial sector. This will be another trait of successful areas for fabricated metals.
The industry will be locationally active over the next several years. New facilities will be established throughout the U.S. Many new metals plants will avail themselves of advantages associated with smaller communities provided these locations have at least moderate talent pool depth, adequate infrastructure including available modern buildings, and industry specific training. Due to transportation costs, many new facilities will serve regional markets (e.g., 500 mile radius).
The following factors will continue to exert the greatest influence over siting new fabricated metals plants:
1. Customer/market access
2. Four-lane highway access
3. Transportation services including rail for some prospects
4. Modern available buildings
5. Fully served, pre-permitted sites
6. Reliable, moderately priced electric utility
7. Natural gas availability/cost
8. Depth/breadth of talent pool
Machine operators
Assemblers
Welders
Machine maintenance
Quality control inspectors
Engineers
Industrial
Materials
Mechanical
9. Labor costs
Immediate
Longer range
10. Nonunion
11. Moderate taxation
12. Meaningful incentives
Preferably cash-based
Earned over time based on:
Jobs
Payroll
Capital Investment
Deal closing funds
Property and sales tax abatement
Financing for smaller companies
Pre-employment training