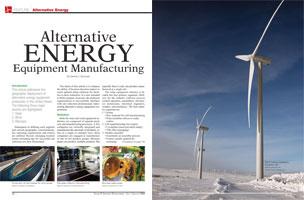
IntroductionThis article addresses the geographic deployment of alternative energy equipment production in the United States. The following three major sectors are highlighted:
Solar
Wind
Biomass
Subsequent to defining each segment and current geographic concentrations, key operating requirements and criteria are outlined. Recent, emerging location trends (including tips for successful site selection) are then illuminated.
The intent of this article is to enhance the ability of location decision-makers to reach optimal siting solutions for facilities in these industries. It is also intended to better prepare economic development organizations to successfully interface with site selection professionals representing alternative energy equipment corporations.
Definition
Both the solar and wind equipment industries are composed of separate products and manufacturing processes. A few companies are vertically integrated and manufacture the spectrum of products, either at a single or multiple sites. Most companies are engaged in manufacture of one or two product groups. Biomass plants can produce multiple products. But typically there is only one product manufactured at a single site.
The solar equipment industry is divided into four primary segments. Skill-sets for the industry embrace process control operators, assemblers, electronics technicians, electrical engineers, welders, and mechanics. The four industry segments are:
Casting
Raw material for cell manufacturing
Polycrystalline silicon to make wafers
Cell manufacturing (two types)
Crystalline (most prevalent today)
Thin film (emerging)
Module assembly
Essentially an assembly process
Frames usually applied for mounting
Systems assembly
Completed onsite
Two main functions
Electrical integration
Mechanical integration
Wind turbines are machines that convert wind’s kinetic energy into rotational energy and then electricity. The primary components of a wind turbine are:
Base
Concrete reinforced with steel bars
Installed onsite
Tower
White steel cylinder
75-100’ tall/10’ diameter
Blades
Mainly fiberglass or other composite material
50’ long
Nacelle
Generator
Gearbox
Drive shaft
Other components (e.g., cabling, bolts)
The production process for wind turbines typically involves machine operations (e.g., molding, drilling, boring), soldering, welding, electronics testing (especially for nacelles), and assembly. Skills associated with metalworking industries are applicable to wind turbines.
Biomass is a renewable energy source derived from living or recently living organisms. It may also include biodegradable wastes that can be burned as fuel. Key skill-sets are process control operators (e.g., mixing/bathing machines). Biomass conversion into fuel is similar to chemical manufacturing. The process can involve one of three conversion methods: thermal, chemical, biochemical.
An emerging production technology is known as cellulosic. This basically involves drawing inedible material from a plant (e.g., cornhusk) but leaving the edible part of the plant intact.
Biomass fuel can be made from multiple sources. These include algae, crops, grasses, wood, and waste (animal, municipal, manufacturing).
Geographic Concentration
All states have the potential to develop renewable energy. However, there is significant variation due to prevalent atmospheric conditions and natural resource bases.
The greatest solar energy capability lies in the Southwest and portions of the Intermountain West. Secondary potentials exist in the Pacific Time Zone, Midwest and Southeast. Map A demonstrates solar energy potential across the U.S.
Wind energy resources are most pronounced in the upper Midwest, northern half of the Rocky Mountains, portions of Pacific Time Zone states, portions of South Central states, northern Appalachia, the Great Lakes, and northern Atlantic coast. The latter two represent offshore wind potential. Map B tells the story of wind energy potential.
Regions with the largest biomass resource base include the Southeast, South Central, and Midwest. Map C depicts biomass material resource concentrations.
Requirements/CriteriaPrototypical operating requirements (e.g., building, site, capital investment, labor, utilities, etc.) for facilities in each industry segment appear in Exhibit One. By and large, alternative energy equipment plants are capital intensive and require large sites and buildings. There is a strong preference for siting new solar and wind facilities close (within overnight truck delivery) to existing and potential customers (solar wafers and crystalline cells the exception). Biomass operations tend to be situated near the pertinent raw material base.
Transportation costs are important (except for wafers and cells). In some cases, rail service is important (e.g., casting or wafers for inbound, module assembly for outbound, wind towers for outbound, and biomass for inbound). Motor carrier service is a top priority for all segments.
Electric power (cost, capacity, reliability) is critical for wafers (consumes large amount of electricity) and fairly important for other segments (moderately large consumption). Vast quantities of water are necessary for wafer production.
Experienced semi-skilled, skilled, and technical labor are important for all segments. As these are capital intensive enterprises, property and sales tax on equipment comprise a key factor. Incentives are also key once a number of qualified locations have been identified. Among the most desired incentives are renewable energy tax credits and grants, capital investment tax credits, property tax exemptions, site development assistance, deal closing grants, and pre-employment training. As many operations do not post significant profit, transferable tax credits are strongly preferred. There are also Federal tax credits (30% of investment under the stimulus package) and Department of Energy loans and grants. Fast track construction and permit facilitation are highly desirable.
The majority of companies like to locate in states that overtly support alternate energy development and consumption. One positive trait is whether a state has a renewable portfolio standard. This is a state policy requiring electricity providers to obtain a minimum (often 15%-20% by a certain year) of power from renewable energy sources. Currently, there are 29 states with such a policy. It is anticipated that many more will adopt such a policy over the next couple of years. Dedicated tax credits (specific to the industry) and collaborative efforts to advance the industry are also coveted.
Companies do place importance on higher educational resources. Especially key are renewable energy research, two and four year curricula in renewable energy, and specialized training. It is important that private industry team with higher educational institutions to foster needs of the renewable energy industry.
Location Trends
This is a nascent industry so it is not surprising that the first wave of new facilities has tended to cluster near customers (solar and wind) or raw materials (biomass). Finally selected locations possess the attributes (as mentioned above) deemed of greatest criticality by the particular operation. Among the states that have landed a significant number of alternative energy equipment manufacturers are:
Solar | Wind | Biomass |
Oregon | North Dakota | Georgia |
Arizona | Iowa | Louisiana |
New Mexico | Kansas | Iowa |
Colorado | Colorado | Texas |
Michigan | Ohio | Florida |
Pennsylvania | Michigan | Illinois |
California | Montana | North Carolina |
Nevada | Arkansas | New York |
Idaho | Texas | Indiana |
Utah | Indiana | Mississippi |
Examples of recent new facility announcements within each industry are shown below.
Solar | Location |
SMA Solar (inverters) | Denver, CO |
Hemlock (castings) | Saginaw, MI; Clarksville, TN |
Sanyo (integrated) | Salem, OR |
Walker (castings) | Cleveland, TN |
Schott (cells) | Albuquerque, NM |
Abound Solar (cells) | Ft. Collins, CO |
Solon (modules) | Tuscon, AZ |
Advanced Solar Photonics (modules) | Lake Mary, FL |
United Solar (cells) | Greenville, MI |
Solar World (cells) | Hillsboro, OR |
Solar World (modules) | Camarillo, CA |
Heliosphera (panels) | Philadelphia, PA |
A-Power Suntech (modules) | Phoenix, AZ |
Wind | Location |
Nordex (blades & nacelles) | Jonesboro, AR |
Siemens (blades) | Ft. Dodge, IA |
Molded Fiberglass (blades) | Aberdeen, SD |
LM Glasfiber (blades) | Little Rock, AR; Grand Forks, MI |
Vestas (blades) | Brighton, CO; Windsor, CO |
Global Wind Systems (blades) | Novi, MI |
Fuhrlander (blades) | Butte, MT |
Vestas (towers) | Pueblo, CO |
Vestas (nacelles) | Brighton, CO |
Siemens (nacelles) | Elgin, IL; Hutchinson, KS |
Bergywind (small turbines) | Norman, OK |
Southwest Wind Power (small turbines) | Flagstaff, AZ |
Acciona (wind turbines) | West Branch, IA |
Biomass | Location |
Range Fuels (wood chips) | Soterton, GA |
US Biodiesel (algae) | Seabrook, TX |
Brain Cellulosic (corn) | Emmetsburn, IA |
Cargill (soybeans) | Iowa Falls, IA |
Fibrowatt (poultry litter) | Surry County, NC |
Verenium (cellulosic glass straw) | Jennings, LA |
Xethanol (cellulosic corn) | Spring Hope, NC |
MS Investment Petroleum (poultry fat) | Aberdeen, MS |
Logen Biorefinery (cellulosic corn/barley) | Shelley, ID |
It is likely that the pattern of locating near major markets for wind and solar will continue over the near future. However, as these markets either mature or become constrained due to transmission capacity we expect to see a growing presence in secondary market concentrations. The winning states will be those that place the greatest emphasis (policy, taxes/incentives, and education/training) on the underlying foundation supporting the industry. Biomass will continue expanding in the Southeast and Midwest. But other states will also be players due to agricultural, municipal and factory waste resources.
Conclusions
The alternative energy equipment industry is essentially in its infancy. Growth prospects are bright due to a convergence of forces. These include expensive fossil fuel energy, the imperative to wean the country from foreign energy sources, the burgeoning green movement, the importance of sustainability within corporate America, and government’s emphasis on developing clean energy.
More and more companies will be seeking new sites. Companies should carefully delineate realistic operating requirements with an eye toward the future, ascertain the criticality of being proximate to a targeted customer or raw material base, determine if the defined market or raw material base can sustain scale of operation, assign appropriate weightings to location criteria focusing on those which are overarching, and adhere to a logical and systematic process for finding the optimal location. And, a word of caution: do not let incentives drive the process. It is far more important to choose a location which maximizes long-term success. Incentives should be considered as “icing on the cake.”
Economic development agencies need to cultivate resources that most benefit firms within the respective industry segment. Physical infrastructure, collaborative initiatives, and favorable policies are pivotal to success.
Lastly, the lion’s share of new investment will be placed where the greatest end-user (or raw material) concentrations exist. But as green energy is a national priority, all states will witness an infusion of the industry. Greatest success will accrue to those states and localities that best understand and respond to the most critical industry needs.