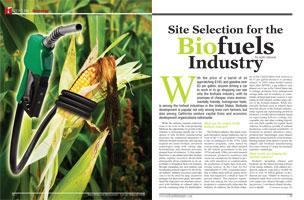
With the price of a barrel of oil approaching $100, and gasoline over $3 per gallon, anyone driving a car to work or to go shopping can see why the biofuels industry, with its promises of cheaper, more environmentally friendly, homegrown fuels, is among the hottest industries in the United States. Biofuels development is popular not only among Iowa corn farmers, but also among California venture capital firms and economic development organizations nationwide. While the industry remains relatively close to its roots in the corn-producing Midwest, the opportunity for growth in this industry is increasing rapidly due to the spread of new biofuels manufacturing processes, the commercial maturation of different biofuels feedstocks, and ongoing research into newer biofuels conversion technologies using both cutting edge biotechnology and chemical processes gleaned from oil refineries. To best understand how to site ethanol and other biofuels plants, industry executives should think strategically about expansions as an opportunity to strengthen their core business through expanding into new markets and broadening political support for the biofuels industry. Industry executives must take care to not be awed by large incentives packages for short-term gains, and understand the long-term cost structures associated with building an ethanol plant to provide continuing value for shareholders.
What are the origins of the biofuels industry?
The biofuels industry, like many resurgent alternative energy industries, has its roots in the U.S. government’s response to the oil embargoes of the 1970s. Early incentive programs, some started by corn-growing states, and others adopted by the federal government in the late 1970s and early 1980s, provided research investment, production incentives, and excise tax exemptions for ethanol to provide early incentives to commercialize the production of liquid fuels from non-foreign sources. In the Clean Air Act Amendments of 1990, oxygenated gasoline in urban areas with air quality problems was required to contain at least 30 percent ethanol. This statutory requirement was among the first government programs to commercially jump-start the industry. In addition, the biofuels industry in the United States now receives a $0.51 per gallon incentive to produce ethanol. In 2005, when methyl tertiary butyl ether (MTBE), a gas additive, was phased out of use in the United States due to leakage problems from underground storage tanks and its tendency to contaminate underground water sources, it was replaced with ethanol, another major driver of the biofuels industry. While historically biofuels such as ethanol have been the drivers of the biofuels industry, many regions are experiencing growth in biodiesel, a locally-driven industry based on reprocessing leftover cooking oils, vegetable oils, and other cooking byproducts into fuels suitable for regular diesel vehicles. In addition, growth of soybean production could expand availability of biodiesel as another alternative transportation fuel. Interestingly, some ethanol plants are being fueled by solid biomass, burning manure from dairies to power the ethanol and biodiesel manufacturing processes instead of using increasingly expensive natural gas.
What trends are shaping the biofuels industry?
Biofuels, including ethanol and biodiesel, are the fastest growing portions of the energy industry, with ethanol production capacity expected to double by 2010 to over 10 billion gallons of production per year. Ethanol in America is primarily made from corn by converting corn sugars into ethanol through a refining process. Corn-based ethanol production is rapidly bumping up against supply constraints, as corn is needed for animal feed, driving increases in the commodities price of corn.
Ethanol plants are increasingly turning their byproducts of miller’s grain and carbon dioxide into salable products. Miller’s grain is useful for animal feed, and carbon dioxide, a very expensive product to transport, is often used for beverage carbonation or injected into oil fields for enhanced oil recovery. Ongoing research into cellulosic ethanol promises breakthroughs in converting cellulose, or woody biomass, including the stems and branches of brush and agricultural byproducts, into ethanol. In fact, Range Fuels broke ground on the first commercial biomass-to-fuel plant in America, in Soperton, Georgia, in November 2007. This plant will convert pine chips and other logging waste into 20 million gallons of ethanol annually. As cellulosic ethanol becomes commercially available, the economic development potential for this segment of the renewable energy industry promises to become more dispersed and available to communities nationwide as a primary job driver.
Site Selection Factors
For any company looking to build a biofuels plant, knowing which factors are most important to short- and long-term cost structures can be the difference between a plant generating profits in six months and a plant generating profits in two years. While the biofuels industry encompasses many different types of facilities, including research and development labs, small scale demonstration plants, and biodiesel plants, by far the most likely plant expansion currently being constructed in the biofuels industry is an ethanol plant. Corporate site selection experts in the biofuels industry focus on several categories of factors in selecting an ideal location for expansion, including:
Underlying Costs Structure
Sites and Infrastructure
Incentives Packages
Community Concerns
Underlying Costs Structure
Executives focusing on building strategic value for their companies should look closely at the cost structures provided by communities seeking biofuels investment. Two factors based on cost alone will likely determine the vast majority of an ethanol plant’s operational costs: feedstock availability and cost, and utilities costs, including natural gas, water and electricity. Feedstock costs alone make up 50-60 percent of the cost of producing a gallon of ethanol. For present ethanol plants, the local price of the corn crop will determine the success of a plant. With the increasing amount of corn devoted to ethanol production, ethanol plants will look for areas without significant competition for their corn supply, as well as an adequate supply of corn for their production needs. As plant types evolve, though the feedstock may change, the importance of an adequate, cheap, reliable source of feedstock will continue to provide the biggest site selection criteria.
Utility costs make up the next largest cost factor, and are consequently the next largest site selection criteria considered by ethanol plant operators. Communities considered must have cheap, plentiful supplies of natural gas and water to power these plants. Many companies will consider developing their own water supplies when public supplies are not available by drilling industrial wells, but regions must have adequate water underground for this option to work. Natural gas, water and electricity costs account for an additional 20-30 percent of the costs for producing a gallon of ethanol. While providing access to inexpensive feedstocks and utilities provides communities with an advantage in reducing the costs structure for producing ethanol, these factors alone will not ensure corporate investment in a community.
Sites and Infrastructure
General locations for sites must minimize both the distance from feedstock supplies as well as the distance to major markets for highly oxygenated gasoline, primarily major metropolitan areas across the United States. Typical ethanol plants will require sites in the range of 40-80 acres, with smaller companies reporting sites of as few as 10 acres, while plants producing up to 100 million gallons per year will require sites of up to 160 acres. Rail access and highway access are important for transportation of both feedstocks and finished products. Because of the difficulty in transporting ethanol long distances (ethanol is corrosive to traditional petroleum pipelines and must be trucked to its final destination), ethanol production and mixing with gasoline will increasingly occur close to large demand centers.
Ultimately, the site size depends not only on the planned size of the ethanol plant to be constructed, but also on the room required for rail sidings, rail switching yards, and leaving room for expansion of the plant over time. Executives should work with operations specialists in their company to determine the necessary acreage and infrastructure for their particular investment.
Incentives Packages and Public Policies
In addition to the substantial incentives provided by the federal government for ethanol production, additional targeted incentives will attract ethanol plants and other biofuels businesses to a state. One of the most successful programs has been Minnesota’s oxygen standards for fuels, which sets fuel standards that can most cost-effectively be met through ethanol mixing. This has had the effect of attracting additional ethanol plants to Minnesota that may otherwise have located in neighboring states. States have also experimented with state ethanol production tax credits, fuel tax incentives, and of course, state and local tax abatements.
USDA’s Agricultural Research Service has developed a production and financial model, for example, a mid-size ethanol plant, which can provide companies with additional insight into the capital and operating cost parameters and includes a projected investor return-on-investment (ROI) statement. Understanding these models at a corporate level can help to leverage incentive programs specifically targeted to reduce the largest cost factors in any operation, providing a competitive edge to companies who site their operations not only based on commodities costs, but who take the time to understand the strategic financial aspects of a siting decision. While these incentives programs will not drive the site selection process, incentives can make the difference between short-listed communities.
Additionally, public policies, including air emissions permitting, and general construction permitting timelines can make the difference for biofuels producers. States and regions with fast turnarounds in permitting processes can be good partners for biofuels investment by providing ethanol producers with the ability to begin operations more quickly. Companies should ensure a business-friendly operating environment for long-term stability and value in their operations.
Community Concerns
Finally, ethanol producers must consider community concerns when siting a biofuels plant. Community support is essential to reducing the time to market for ethanol producers. Companies must take into account prevailing wind directions to avoid any odors downwind of the plant. Companies must also take into account dust control, noise pollution, and site lighting and any effects these might have on the surrounding community. Several plants in development are facing community opposition due to these issues, and communities should be aware of these challenges when attracting ethanol production plants.
Conclusion
Companies seeking to expand in the biofuels industry must assess sites at a number of different levels. Strategic decisions, such as entering new markets, expanding political support for production incentives through diversifying sites, and building access to multiple feedstocks must be considered when selecting a site. Operational decisions, including site size and infrastructure requirements, access to transportation, and feedstock availability are also important. Finally, companies must consider the business operating environment, including available incentives, public permitting processes and community concerns, before making an investment in a community. As the processes for converting different feedstocks, such as logging debris and switchgrass, into cellulosic ethanol, many businesses will seek to capture the opportunities surrounding the biofuels industry. Those companies who site strategically as well as tactically will best be able to compete in an increasingly competitive industry.