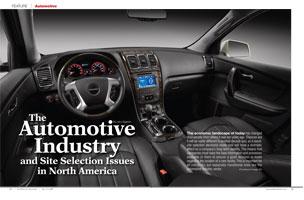
The economic landscape of today has changed dramatically from where it was ten years ago. Chances are it will be vastly different in another decade and, as a result, site selection decisions made now will have a dramatic effect on a company's long-term viability. This means that companies must have the best information and processes available to them to ensure a good decision is made regarding the location of a new facility. This is important for all industries, but especially transitional ones like the automotive industry sector.
An increased demand for the technology required to compete on a global level, along with a well educated workforce, produces one kind of challenge, while shifts in manufacturing and distribution from both national and international suppliers creates another. When all of them are combined they create new dynamics in the automotive site selection process. The best location can be critical to the success of a new, expanded or relocated operation. Companies need to not only identify prospective sites, but also carefully and comprehensively analyze their suitability for their respective needs. From the overall real estate market, including brownfield redevelopment and greenfield site development, transportation infrastructure, susceptibility to natural disasters, proximity to competitors and vendors, labor market conditions, and economic impact studies, sites must be examined for their current value and future impact to the company's operations.
Successful location modeling typically includes:
Information on workforce skill levels and labor costs
Real estate costs
Available economic development incentives
Demographic statistics
Cost of living
Utility rates, availability and redundancy
Tax rates, both business and individual
Infrastructure availability
Transportation options and access to interstates, rail lines and airports
Regulatory environment
In the automotive industry, however, some site selection factors weigh more heavily than others, to the point where it is not only a question of thorough analysis but also interpreting the signs of the future. This type of understanding may be most influential and a critical factor for the industry in years to come.
![]() |
MAGNA Drivetrain |
Companies are correctly focused on adapting and implementing structures that allow for flexibility in their workforce and supply chain, as well as leveraging costs and productivity through new technologies. Improving efficiency through renewable energy technology will most likely be a key factor moving forward.
For example, California utilities are responding to current environmental and financial issues by promoting a statewide program that encourages high performance nonresidential building design and construction. The benefits include reduced long-term operating costs, conservation of natural resources and cleaner air due to lower need for power generation. This also helps to improve the comfort, health and productivity of workers. Automotive manufacturers and suppliers will be watching initiatives like this one as they continue to respond to rising operating costs and new regulations.
Another case in point is one of our automotive clients, MAGNA Drivetrain, a Tier I supplier of drivetrain components and systems for light trucks and automobiles. Several years ago MAGNA was looking to increase its manufacturing and assembly capabilities near one of its existing plants in Lansing, Michigan. MAGNA supplies components to DCX, GM, Ford, Toyota and Honda. Phase I of the project included a 200,000-square-foot building consisting of manufacturing, assembly, logistics and office space, and the ability to expand the building as the company was awarded new contracts from its customers.
As noted above, there is always a complex array of issues unique to the automotive site selection process. In this case, land availability, transportation infrastructure and supply chain issues, as well as economic development incentives can offset both short- and long-term operating costs.
Appropriate land and existing building options to accommodate MAGNA's current and future needs were some of our earliest considerations for the site selection process. Real estate requirements included utility infrastructure, properly zoned land, major interstate highway access, a preference for rail service, and a location within a triangle whose corners were Indianapolis, Indiana, Lansing, Michigan and Dayton, Ohio.
![]() |
Members of United Auto Workers Local 602 install a trailer hitch on teh 2011 GMC Acadia Denali, which began production on Tuesday, September 21, 2010 at the Lansing Delta Township Assembly Plant. |
While the automotive industry has grown tremendously in the Southern states during the past 20-25 years, in places such as Kentucky, South Carolina, Tennessee, Georgia and Texas, many supply chain factors still favor the Midwest for certain types of projects due to efficiencies found in manufacturing plants located within the region. Indiana alone has approximately 135,000 workers employed at close to 600 facilities in the automotive industry.
This is not surprising considering the findings of a 2010 report from the Brookings Institute on Economic Recovery and Transformation in the Great Lakes Region which confirmed the fact that the Great Lakes region has significant resources available as a byproduct of the automotive industry. These resources include global trade networks, which are critical to an export economy, clean energy/low carbon capacity, innovative infrastructure, and opportunities for an educational network that will continue to feed a changing workforce need.1 In addition, the large number of universities and community colleges in the region helps develop the skill set of the workforce that is necessary to attract and support manufacturers and suppliers.
During the site selection process for MAGNA, plentiful real estate options allowed us to rapidly hone in on several potential locations within the Great Lakes Region. Our analysis took into effect not only the key real estate issues, but also environmental issues, zoning regulations, permit expediency, utility costs/redundancy and emission regulations. In addition, we examined key economic development incentive opportunities such as land subsidies, property tax abatement, job creation and capital investment income tax credits, training grants and public infrastructure grants.
Because manufacturing components come from various points throughout North America and around the world, proximity to railroads and ports, as well as highway infrastructure will continue to play an important role in the site selection process. The distance to and from suppliers, competitors and customers are also key issues to consider. Suppliers often want to be close to as many customers as possible to offset their inventory and logistics costs. Our site location modeling and analysis for MAGNA began with research on the number of engine and transmission plants within a 450-mile radius of the specified locations.
![]() |
Ford Motor Company celebrated the launch of the 2012 Ford Focus with employees, dealers, suppliers, media and other invited guests at the Michigan Assembly Plant. (Photo by Sam Varnhagen/Ford Motor Co.) |
There is constant pressure to drive excess costs out of the OEM supply chain. Moving forward, companies will need to make capital investments to stay competitive. Investment in research and development, and flexibility to adjust to consumer preferences and global market needs, will be critical for long-term success.
Automotive clusters can have a significant advantage in a site location decision in that they affect investment interests. In the Midwest, research and innovation infrastructure is driving the development of new products and processes. Within the Great Lakes Region, Michigan, Ohio and Illinois are among the top states in terms of green tech patenting, focused on new technologies in battery power, hybrid systems and fuel cells.2 In West Virginia, Toyota is investing $64 million and creating 40 new jobs at its facility in Buffalo, and will add six-speed automatic transmission capacity to the plant. "During the economic downturn, there were times when we had no choice but to stop production because of slowing sales. But, our North American plants made the important decision to provide full employment," said Toyota Motor Manufacturing West Virginia President Yoji Suzuki. "The training and process improvements during the worst of times prepared this plant for (the) future."
In view of the fact that automotive projects are capital intensive, it is important to identify appropriate and available economic development incentives to offset both start-up and ongoing operating costs. A key component in the MAGNA project was the availability of local and state governmental finance to support the project.
The Indiana Department of Commerce (now known as the Indiana Economic Development Corporation) offered several types of economic development incentives to support the project. These incentives included: the Skills Enhancement Fund (SEF) to help defray the costs of training new employees; the Industrial Development Infrastructure Assistance Program to pay for infrastructure improvements; the Economic Development for a Growing Economy (EDGE) job creation tax credits; and the Hoosier Business Investment (HBI) capital investment tax credits.
In addition, the Indiana Department of Workforce Development provided funding to match jobseekers' skill levels to particular company job requirements, which helped MAGNA put together its new team in a very efficient manner. The local incentive package also included funding for the purchase of land, environmental testing of property, public infrastructure improvements and Tax Increment Financing (TIF). Of considerable advantage to MAGNA was the selection of a site within a Community Revitalization Enhancement District (CReED). This economic development incentive program allowed the company to receive significant financial benefits thru the form of tax incentives tied to qualified capital expenditures and job creation related to the generation of new taxes from the project.
Incentives can be an aggressive tool used by a city and state to attract a project to an area, but there is also an increasing demand for the right kind of labor for the right price. The aforementioned shift in automotive plants to Southern states occurred for a number of reasons: low wage rates, lower cost utilities, non-unionized labor, less expensive land, freight costs, lower taxes, and market share redistribution from traditional domestic manufacturers to Asian and European companies who manufacture in the South.
![]() |
Workers install doors on Chevrolet Malibu and Buick LaCrosse vehicles at the General Motors Fairfax Kansas Plant Tuesday, April 20, 2010 in Fairfax, Kansas. GM announced Wednesday, April 21, 2010, a $257 million investment to produce the next generation Chevrolet Malibu at Fairfax and the Detroit Hamtramck Plant. (Photo by Steve Fecht for General Motors) |
Within the automotive industry, training and human resource services can play a major role in the site selection process. Resources can and should be shared whenever possible, especially where employees with technical expertise are concerned. According to an Original Equipment Suppliers Association (OESA) survey published in November 2010, 69 percent of respondents are adding hourly personnel and 77 percent are adding technical staff. However, 36 percent of respondents stated that they were having difficulty filling technical positions, while 22 percent were having a hard time meeting hourly labor needs. Collaboration that encourages innovation as well as outside investment is important for the growth and progress of the automobile industry. As the industry grows, and as additional technology solutions are implemented, there will be a growing need for a highly trained workforce. Issues such as fuel cell technologies, mechanical engineering, biofuels and advanced battery technology will require a new breed of worker to support an ever-changing automotive industry. The need for flexibility and the ability to adapt and respond to new technologies as they develop will become increasingly important as global competition increases.
Six large companies, rather than three, now dominate the industry. Chrysler, GM, Ford, Honda, Nissan and Toyota all have a global presence and together represent 80 percent of automotive sales in the U.S. marketplace. In the coming months, these automotive companies will continue to face challenges and uncertainties. Flexibility, innovation and foresight will be needed to deal with new issues that affect manufacturers and suppliers. Smart site selection decisions today will give companies an edge over their competition and allow them to draw on an array of resources available to take them into the next wave of automotive production and distribution.
1The Next Economy: Economic Recovery and Transformation in the Great Lakes Region Jennifer S. Vey, John C. Austin and Jennifer Bradley, Sept. 2010.
2Ibid