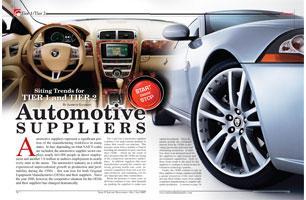
Automotive suppliers represent a significant portion of the manufacturing workforce in many states. In fact, depending on what NAICS codes are included, the automotive supplier sector employs nearly 665,000 people in direct employment and another 1.8 million in indirect employment in nearly every state in the union. The automotive industry as a whole experienced unprecedented growth in production and profitability during the 1990s – this was true for both Original Equipment Manufacturers (OEMs) and their suppliers. Since the year 2000, however, the competitive situation for the OEMs and their suppliers has changed dramatically.
Tier 1 and Tier 2 automotive suppliers continue to be under intense pressure to reduce their overall cost structure. This pressure stems from a number of factors including the demands for price cuts from their OEMs – which are the result of price pressures that the OEMs are facing in the competitive automotive marketplace. In addition, suppliers (like most manufacturers around the country) are facing growing health care costs, increased competition from low-cost foreign producers, and escalating cost for raw materials and other commodities.
While the pressure to lower costs on all fronts continues to rise, other demands are pushing the suppliers to make new capital investments. These demands include the continued interest from the OEMs in providing just-in-time deliveries and eliminating inventories. In addition, there is an increased need for the suppliers to add research and development capabilities. Both of these items result in the need for the suppliers to continue to invest in new information technology systems.
Finally, the OEMs continue to rely on these suppliers to design, engineer and build a greater proportion of the total vehicle moving them further away from simple component manufacturing to complete subsystem production. This, too, has resulted in the need for increased capital investments in research and development and information technology has the suppliers have looked for ways to innovate their processes. The National Science Foundation reports that in 2005, nearly 40% of the automotive-related research and development occurs in the automotive supplier sector.
Some of the suppliers have been able to adapt to this new environment and others have not. This competitive environment has resulted in a number of mergers, acquisitions, and other industry consolidations. Companies that are being successful in this environment are those that have been able to adapt quickly bringing new products and processes to the marketplace. In order to be successful supplier companies must have a collaborative and open relationship with their customer OEMs.
All of these factors discussed above have an impact on the location strategies of automotive supplier companies. In today’s competitive environment it is more important than ever for automotive supplier companies to make strategic thoughtful choices about their plant locations rather than simply building facilities where customers demand.
Factors in Automotive Supplier Plant Locations
Proximity to OEMs
The current plant siting model for automotive assembly operations and their suppliers usually means that the landing of an automotive final assembly plant will also result in a region receiving more than its fair share of secondary facilities that will supply the plant. Typically the supplier operations create even more jobs for the community than the automotive assembly plant itself. The Southern Automotive Corridor is a prime example of this phenomenon with hundreds of new automotive supplier companies and tens of thousands of new jobs created from Mississippi to South Carolina in the decade following the announcement of BMW in South Carolina, Mercedes, Honda, and Hyundai in Alabama, Nissan in Mississippi, and Kia in Georgia.
However, as a result of the mergers and acquisitions, the need to supply multiple OEM customers in a just-in-time fashion and the demand for cost reductions (as described above) Tier 1 and Tier 2 suppliers are siting new capital investments in more centrally located communities. Proximity to multiple assembly plants is still one of the greatest determinants in an automotive supplier location, but the suppliers are going to be looking for ways in which they can maximize that investment to serve as many customers as possible.
Human Resources
Tier 1 and Tier 2 suppliers will have to continue to find ways to become more productive in order to meet the competitive demands of the current economic situation. This productivity will come in the form of new innovative processes, information technology, and highly-automated machinery. As such, these facilities will require a dramatically different skill set from a flexible and high-performance workforce.
Supplier companies will seek partners in the local community and technical colleges to provide customized training (i.e. Six Sigma, TS 16949 certification similar to the ISO 9000 series of the past). In order to be competitive, communities will need to be in a position to provide flexible, customized start-up recruiting, screening, and pre-employment training programs to potential prospects. These programs will have to offer highly innovative screening tools and provide the well-rounded training opportunities to give the supplier companies a productive, high-performance workforce in a timely manner.
Engineering Support / Higher Education
As the supplier companies’ participation in research and development continues to increase, their need to have access to quality engineering programs and engineering support will also continue to increase. In plant location searches, access to graduate students from quality engineering programs will be an important consideration. In addition, locations that can offer financial support to shared research infrastructure and research programs will have a competitive advantage in future supplier capital investment decisions.
An example can be found in The Timken Company’s decision to locate its process and product engineering team for powertrain products at Clemson University’s International Center for Automotive Research in Greenville, South Carolina. This move puts Timken in close proximity to the automotive research support, partners and graduate students it will need to improve its research and development capabilities and ultimately innovate its products and processes to meet its’ customers demands.
Transportation infrastructure
Proximity to Interstate systems (or highways of comparable quality) with quick efficient access to multiple assembly plants will be a must requirement for most Tier 1 ant Tier 2 suppliers. There is an inherent geographic advantage associated with this requirement – your community is either close to a supplier’s potential customer base or it is not. But, having quality transportation access to multiple OEMs or other potential customers in other product lines can in some instances mitigate the distance.
Sites / Facilities
Like almost all new capital investment projects, sites that are ready for development are going to be a real asset for communities trying to recruit automotive assembly operations. As discussed above, companies in the automotive supplier sector are under intense competitive pressure and when the decision has been made to invest in a new facility, the company needs to get that facility up and running as quickly as possible. Therefore, communities that have taken the time to identify sites that are suitable for development (i.e. environmental assessments are complete) and do the necessary due diligence to ensure that the site can be served by all utilities will have an important competitive advantage. One potential example, automotive business parks provide a distinct advantage for those suppliers who produce substantial sub-assemblies and have an emphasis on time of delivery considerations.