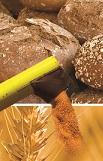
Taco Bell wasn’t thinking about its corporate or franchisee site locations when it coined the phrase “think outside the bun” as its company advertising slogan, but it should have. Food processors in the past traditionally conducted site selection using the same planning as the infamous bank robber Willie Sutton used to rob banks. When asked why he selected a particular bank, he replied, “That’s where the money is.” In the case of food processors, historically they would look at site selection and expansion with the simple notion, “That’s where the produce (or beef, fish or milk) is.”
An Industry of Expansion and Consolidation
The U.S. Bureau of Labor Statistics reports there are currently more than 29,000 companies defined as food and beverage process manufacturers in the United States, employing more than 1.4 million people. Most food processing corporate CEOs foresee production and subsequent job increases of better than 20 percent in 2014, according to Food Processing magazine.
However, the increased number of mergers and acquisitions that have occurred in the food processing industry over the past 12 months — notably, the acquisition of Ralcorp Holdings by ConAgra Foods, Cargill being the winning bidder in the federal bankruptcy court auction of SFAs Foods ground beef processing plant and perhaps the most aggressive, Flowers Foods, that not only scooped up Hostess Bread Brands, but also added Lepage Bakeries and entered into an agreement with Mexico’s Grupo Bimbo to receive exclusive license to the Sara Lee and Earthgrains brands — is creating a Willie Sutton doubled-edged sword environment for economic development organizations.
Corporate site selectors in the food processing industry should take note that economic development organizations are wrestling with not only the question of how they can attract expansion of the new food processing facilities, but how to hold on to their existing food processing facilities in the face of consolidations due to this unprecedented, and record setting, number of mergers and acquisitions.
There were a total of 316 acquisitions in 2012 according to Food Processing magazine (August 2013). The first thing is to understand why this is happening. Dave Fusaro, editor-in-chief of Food Processing magazine said in the January 2103 issue on the state of the industry, “Just when you thought the recession’s end would bring calm, it’s time to reinvent your company and meet new challenges.” He noted that in the aftermath of the recession, “a new emphasis on profitability and repositioning is emerging. Companies survived on being reactive now are expected to be proactive.” Translation: proactive expansion through mergers and acquisitions; profitability through consolidation and increased productivity.
Regionalization and Repositioning
It has been a trend for several years for food processors to regionalize production rather than have a centralized facility. This developed as a result of steadily increasing transportation costs and quality concerns. Therefore, food processors are moving closer to population centers and toward the points of consumption. This will only be accelerated by the consolidation of brands under a single corporate entity. For example, Koch Foods expanded in Hamilton, Georgia, by purchasing Cagle’s Inc.’s facility last year at a cost of $49 million. Koch Foods retained Cagle’s existing 350 jobs and added 350 more. A second phase expansion by Koch will create 750 additional jobs.
The other edge of that sword is the consolidations, and possible subsequent job losses, due to these acquisition and improvements in food processing technology. An example of that is Hostess Bread Brands, which was acquired by Flowers Foods; Hostess came with 20 bakeries and 38 distribution centers. Keith Wheeler, executive vice president of Flowers Foods, explained Flowers is executing a very deliberate roll out of the iconic brand that is leaving cities across the country from Toledo, Ohio, to Stockton, California, wondering if they are on the chopping block.
The food processing industry is developing a new way of doing business. Driven by technology, consolidations and regionalization, it’s making economic developers revise the way they approach site selection criteria for the industry.
The Top States for Food Processors
It is no surprise that California leads the nation in the number of food processing companies, followed by New York and Texas. These are the three most populous states and time to market is a major consideration. California, however, is seeing some problems in retaining food processing industries. The chief issue in California is the greenhouse gas emissions law Assembly Bill 32 (AB 32), commonly called Cap and Trade. Briefly stated, AB 32 requires companies to reduce their greenhouse gas emissions to 1990 levels by 2020, and by 80 percent of that standard by 2050.
According to a recent study by Andrew Chang & Company, LLC performed on behalf of the California League of Food Processors, the implementation of AB 32 is projected to cost California fruit and vegetable processors more than $150 million in direct costs and more than 2,000 jobs from 2012 to 2020. Direct costs to all industries in the state are projected to be in the $18 to $63 billion range over the same period of time, with employment impacts of 119,000 to 460,000 lost jobs depending on model assumptions and implementation impacts.
Additional carbon credits can be purchased at auction from the state, however, to allow businesses to continue to operate or expand. That gives food processors an expensive choice that will typically run in the millions of dollars. One choice for food processing companies is to spend millions of dollars in new equipment as they attempt to comply with AB 32 requirements. The alternative is to face the prospect of paying additional millions of dollars to “purchase credits” from the state. This is causing many food processors to review their long-term production options since California can be serviced from several neighboring states.
What are Food Processors Looking for in a Site in 2014?
Food Processing magazine’s 12th annual “Manufacturing Trends Survey,” published in January 2013, notes that food processors’ top-three concerns are food safety, cost control and labor. Unfortunately, site selection for the food processing industry is not that easy. Factors influencing food processing location decisions have been discussed in many different studies. Most of these studies focused on the traditional firm location factors: availability of labor, cost of labor, proximity to markets, access to inputs, etc. While all of these still play a role in location selection, there are many other factors that separate the food processing industry and its related industries such as food processing equipment and packaging manufacturing industries from traditional non-food manufacturing. Every industry says “we’re different,” and they are all correct. Every industry has nuances that separate its location decision from a decision in another industry.
When you add in the additional factors that didn’t exist in the food processing industry 20 years ago, such as skyrocketing fuel costs, concerns among consumers over dietary health and food safety, adequate water availability in many locations, ever-growing and restrictive environmental regulations, energy costs, sustainability and a lack of the skilled workforce with the specific expertise needed for the food processing industry, you create a whole new set of variables. For example, last year at Pack Expo, The RSH Group conducted a survey of food processing equipment manufacturers in the Central Valley of California as to their single greatest need in considering a location. The answer was the availability of mechanical engineers and a university program that gave them a steady supply of them. Most of the engineering schools’ programs in the area were turning out electrical engineers that left the area lured by the nearby Silicon Valley.
There is another important consideration for food processing companies in reviewing site locations that may separate them from other industries. Because of the sizable capital investment in a food processing plant and its subsequent tax base, they should look at the bonded indebtedness per capita in the states and/or counties they are considering. Eventually, someone is going to have to pay off this debt, and it will fall heavily on the companies that are already there.
A comprehensive study conducted by Oklahoma State University Robert M. Kerr Food and Agricultural Products Center surveyed 422 food processing and traditional manufacturing companies to determine the difference in location requirements between a non-food processing manufacturer and a food processor manufacturer. The study was divided into five sections – Availability of infrastructure, Cost, Labor, Business climate and Quality of life. All categories were ranked utilizing the standard five-point Likert scale (five representing most important and one representing no importance).
Jim Renzas, principal of the RSH Group, considered an expert on food processing industry site selection as a result of his many years working with organizations such as The California League of Food Processors and The National Restaurant Association, said, “Most economists and the majority of economic developers believe that plant location decisions are driven only or primarily by cost advantages. We have long believed that decision makers base site selection on more factors than raw materials input and transportation costs. Because plant location decisions impact the economic base of a region, an economic development organization should be industry specific, regardless of whether it’s food processing or heavy equipment manufacturing, in their attraction programs emphasizing those qualities considered most important to any given industry.”
Take a look at Oklahoma State University Robert M. Kerr Food and Agricultural Products Center survey’s top 25 factors impacting location decisions between a food processing company and a non-food processing manufacturer shown in the table below in the order of importance.
The food processing industry needs to take a look at how their “want” list overlays with general site location programs. The changing demographics being created in manufacturing of all types by technology, the shift in the logistics paradigm, increased regulation and the drive to more sustainability means food processing manufacturers must address the business of site selection by thinking “outside the bun.”