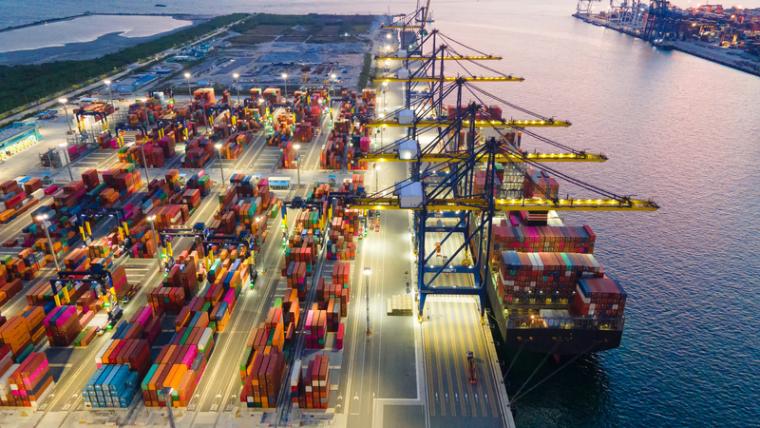
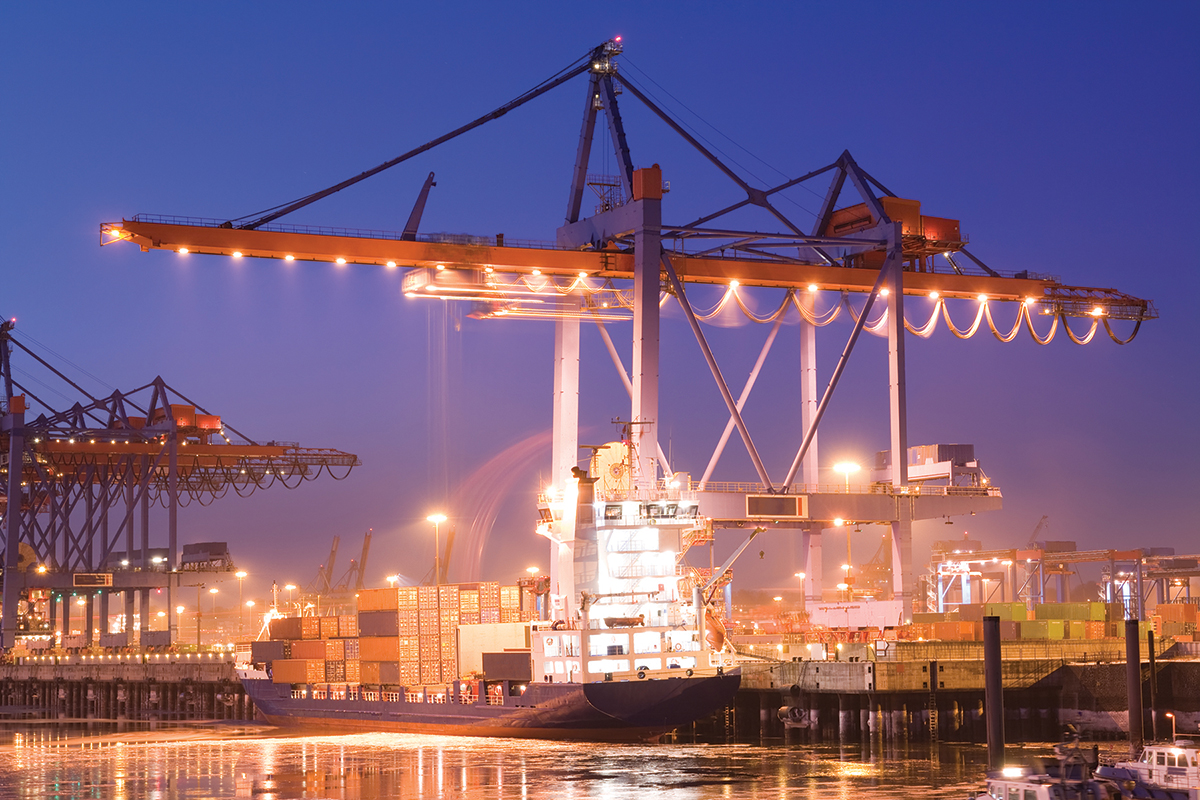
While reshoring is a hot topic right now, it’s important to recognize the trend predates the global COVID-19 pandemic by about five years. The global health crisis, which has strongly affected supply chains and labor, is simply accelerating the trend, adding a new dimension and greater urgency to reshoring.
Reshoring is a trend that can be seen across multiple industry sectors, but particularly those deemed essential, such as defense, technology, aerospace and pharmaceutical. Overall, however, I believe that nearly every industry sector will be engaging in some level of reshoring, particularly as Americans express more interest in buying American.
What Are the Reasons for Reshoring?
To understand reshoring, it’s important to look at the trends that were occurring before the crisis broke. Companies have been looking for a way to consolidate and optimize their supply chains and manufacturing footprints for lower risk and greater resiliency. They’ve realized that long global supply chains are risky, increasingly expensive, and relatively inflexible. Twenty-first century supply chains must be nimble and offer more span of control over the entire footprint.
The bulk of reshoring will come from China, as that is where most companies had placed production capacity to serve global markets. American manufacturers are looking to reduce their dependency on China, perhaps building what’s known as the “China-Plus-Two” model.
China-Plus-Two
While China will likely remain part of the manufacturing equation, expect manufacturers to take action to reduce their reliance on China alone. Some companies might consider establishing facilities elsewhere in Asia, like India or Vietnam. And while Mexico was playing a greater role before the COVID crisis, the shutting of production facilities in that country is likely to slow the pace and drive more production to U.S. shores.
Inhouse, Outsourced or Hybrid
In addition to a different geographic footprint, companies will likely alter their in-house versus outsourced strategies. Many manufacturers are taking a more hybrid approach, bringing some manufacturing back in-house and strategically employing outsourcers located on U.S. shores to build redundancy into their processes. Companies will need to identify the strategy that works best for them. They may also find, in the near term, that suppliers and outsourcers are busy with newly reshored work, which will necessitate a more graduated approach.
What About Costs?
While the conventional wisdom dictates that manufacturing in the U.S. is far costlier than China, this is becoming less true. When we look at the “total landed cost” of manufacturing in China versus the U.S., the U.S. has become more competitive as labor costs and transportation costs have risen in China. In addition, investment in technology made by U.S. companies is making reshoring more economically feasible. New technologies have reduced the labor component in the cost of goods sold, allowing manufacturers to reduce the labor intensity of operations. These technologies include automated processes, virtual reality/assistance, artificial intelligence and more. This trend is likely to continue and will enhance the need to find skilled labor capable of running these smart factories.
These are powerful forces that will not be reversed; they will only accelerate. Once COVID is behind us, economic development agencies and communities need to implement the lessons the pandemic has taught them to ensure they’re in equilibrium for manufacturing by ensuring they’re offering updated economic incentives, robust utilities, modern infrastructure and high-quality labor pools. T&ID