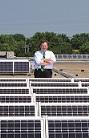
Over the years, warehousing has moved away from only being for the storage of materials, parts and products and has expanded into performing “value-added” services, such as labeling, kitting, assembly, packaging, customization and similar operations. And in recent years, warehouses have assumed additional responsibilities in operations (reverse logistics), in technology (systems and automation) and social issues (sustainability and LEED building certifications).
While the warehousing component has gained in importance within many organizations, it has thrived especially where emphasis has been on training, educating and upgrading the workforce from the management through the operator/associate levels. This has led to improvements in warehouse performance and in recognition throughout the organization. For example, companies are including these individuals on teams that visit customers, participate in site selection projects and collaborate with engineers and designers concerning facility layout issues.
The Work of WERC
For almost four decades the Warehousing Education and Research Council (WERC) has and continues to develop the warehousing and distribution profession by providing practical education, application research and networking opportunities. Among the resources made available are educational events, performance metrics for benchmarking, practical research and peer-to-peer knowledge exchange.
Warehousing has expanded outside its traditional four walls along with the responsibilities of its stakeholders. In response, WERC has added focused offerings to its product and services. One example of special interest to Trade & Industry Development readers was the introduction of a Real Estate track at our 2014 Conference. Led by real estate subject matter experts, the programming addressed a range of real estate-focused topics.
The 2015 Conference committee will again include a Real Estate track along with new tracks addressing the needs of retail, manufacturing, healthcare/pharmaceutical and reverse logistics professionals.
WERC addresses the trends through its research initiatives and collectively the industry contributes to WERC by participating in the research or by sharing their knowledge at the annual meeting. Some examples follow.
WERC Introduces Warehouse Assessment & Certification Program
WERC, in late 2010, announced the industry’s first and only best practices certification program. The WERC Warehouse Certification Program certifies an individual’s warehouse facility’s capabilities and its ability to perform core warehousing functions.
The two-day assessment audit examines 114 processes to certify that the facility is executing its processes in a manner that is consistent with recognized industry standards. Certification is based on audits using the WERC Warehousing & Fulfillment Process Benchmark & Best Practices Guide. The Guide outlines five levels of warehouse process competencies and covers the common warehouse practices of receiving and inspection, material handling, slotting, storage and inventory control, warehouse management systems, shipping documentation, picking and packing and load consolidation and shipping.
To date, 40 individual warehouse/distribution center facilities, domestic and international, have been designated as a WERC Certified Warehouse.
Every five years since 1998, WERC has conducted a survey to determine facility trends in the industry. One objective is to determine the latest sustainability issues. The most recent survey (2012) indicated sustainability is receiving considerably more emphasis by the industry than it had in previous years and it is much more sustainability conscious.
Among the green initiatives adopted, the WERC survey respondents submitted a diverse list, indicating innovations ranging from purchasing renewable energy credits to replacing older light fixtures with those that were more environmentally friendly. Some 13 percent were using solar power and 18 percent were pursuing LEED certification.
A Sustainability Case Study
Surveys can indicate trends and movements, but it’s really a solid case study that provides valuable insights and learnings about specific practices and technologies implemented. At the 2014 WERC Conference, an industry leader shared his company’s experiences to improve its buildings’ sustainability and to do so affordably.
Richard Murphy, president and CEO of the Murphy Warehouse Company, detailed how the company has retrofitted its facilities to lessen their impact on the environment. For example:
-
Lighting. Murphy purchased a 350,000 square-foot building of 1980s vintage and one of the first issues addressed was whether or not to keep the existing lighting, which was high-pressure sodium, or to retrofit with LED. Doing their own research, Murphy learned that LED would cost more money and the ROI for T-5 was determined to be 2.6 years, while the ROI for LED was 4.4 years. Then there was consideration of using motion sensors, which would be operating at about 20 percent of the time. Murphy opted for the LED-based solution.
-
Landscaping. Murphy addressed the landscaping question by debating between cut, manicured lawns and native prairie grass. The decision was to go with the prairie grass because prairie grasses have the ability to carbon sequester through their 15-foot-deep roots and no watering or fertilizing is needed with prairie grass. Additionally, maintaining prairie grasses adds up to a 7.3 percent savings compared to cut grasses.
-
Solar power. Warehouse roofs are large flat areas, so solar power can be a great use of space. Working closely with the city, Murphy was able to design a solar panel system with five major innovations and secured four major grants. Without this, he maintained, it would require 20 years to obtain an ROI. “Work closely with your local agencies and the small business administration,” is his advice.
Murphy Warehouse has gone a long way toward carbon neutrality. It is almost at net neutrality versus 70-plus without the innovations, Murphy shared.1
Research Notes Trends and Issues
WERC addresses and defines industry trends through it research and provides operational information, based on member input, for metrics studies (WERCWatch, DC Measures 2014 and Facility Trends 2012-2013) and warehousing best practices guide (Warehousing & Fulfillment Process & Best Practices Guide)2. A recent research study is The World Is Urbanizing: Is Your Logistical System Ready?, which sought to better understand distribution and warehousing problems in large cities. The three key findings were identified as traffic, accessibility and locations. Specifically:
-
Traffic. City traffic, including intermodal, rail, pedestrian and airlines, can cause major delays. These delays will be expected to worsen over the next two-three decades, as the population of the world continues to increase.
-
Accessibility. With more tourists, more shoppers and more obstacles in urban areas, reaching the pick-up or delivery point grow more difficult or even impossible. To avoid delays on primary delivery routes, managers should consider alternative transportation and storage methods.
-
Facility locations. As cities get more crowded, more people bargain for scarce real estate and prices for land and buildings rise. Companies cannot control traffic and accessibility. They can, however, decide where to locate. Facility location presents both opportunities and challenges in urban areas, the report concludes.
For the future, warehouses and distribution centers aren’t going away. They may look different and have a different role, but they still will be a major, critical and contributing part of a company’s business strategy and a vital part of its supply chain.
Notes
1Listen to the complete conference session at http://www.werc.org/sustainability/.
2 For copies and/or additional information about these and other reports, go to www.werc.org.