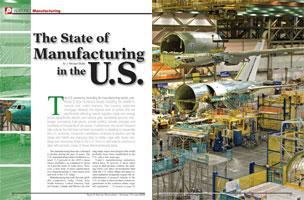
The U.S. economy, including its manufacturing sector, continues to face numerous issues including the volatile financial and credit markets, the housing subprime mortgage debacle, the highest ever oil prices that are significantly affecting overall logistics costs and energy prices (specifically electric and natural gas), worldwide security challenges, increasing food prices, armed conflict, climate changes and hundreds of thousands of job losses. Furthermore, the recent frequent rate cuts by the Fed have not been successful in assisting to rejuvenate the U.S. economy. Consumer confidence continues to decline, and life styles and habits are changing daily to better cope with these relatively poor economic times in the U.S. The U.S. will have to continue to deal with periodic crises of these aforementioned types.
The manufacturing base has continued to decline during the past 10 years. The U.S. manufacturing related workforce totaled 11.5 percent in the 2005 Census (latest available), as compared to about 16.4 percent some 10 years prior. However, a new style of more capital-intensive manufacturing is very much alive and well in the U.S. today.
Manufacturing has truly become globally competitive. India, China, Asia, South America, Central America, Eastern Europe, Canada, and Mexico are winning many major new projects that would probably have been established in the U.S. only a few years ago.
Today’s manufacturing industries, which have 30 percent or more labor costs in final product content, are seeking lower cost labor environments than what the U.S. offers. Many aerospace related industries frequently require the establishments of projects outside of the U.S. in order to meet product content requirements in the countries where original equipment manufacturers are selling products.
Developed countries such as the U.S., all of Europe, and even Japan and China, are experiencing qualified labor shortages in production related industries; yet countries such as Mexico, Brazil, Ireland, Egypt, Turkey, India, Malaysia, Indonesia and Singapore are projecting qualified labor surpluses for at least the next 10 to 15 years.
Pertinent Criteria for Site Selection
Today’s site selection process for various types of project establishments begins with a more global perspective of analysis with particular initial emphasis on pertinent criteria such as worldwide access to customers and vendors, overall business competitiveness, logistics/supply chain characteristics, education attainment levels, the availability and/or trainability of the required skill sets for all types and levels of workforces, managements’ assessments for the cultural merging of given projects and new countries, industry clusters, conditions regarding inflation rates and trade deficits, natural disaster risks, intellectual property transfer protection, and reliable and secure communications solutions.
Once the initial pertinent criteria have been analyzed quantitatively and qualitatively, the site selection process turns to evaluations of criteria regarding global politics and monetary policies; utilities (long-term availabilities and quality [electricity, natural gas, water and wastewater], dependability and costs); environmental and physical project development related reviews and permitting; available existing properties – existing, and sites for new physical facility construction; all types and magnitudes of statutory and discretionary incentives (ex. – financing, tax reductions, training, infrastructure improvements, property reduced costs, political support, accelerated permitting, and special conditions) by all levels of government; and policies and regulations for work permits and/or visas for foreign technical and professional personnel.
The next round of criteria that are evaluated in today’s global site selection process include labor laws and regulations; business legal structures and reporting functions; commercial air access and travel safety features; globally-positioned, fully-integrated intermodal operations (highways, deepwater port access, rail and air services) for product movements on a worldwide basis; and the necessary process and accelerated timing for the total site selection process.
For numerous manufacturing industries, rail access for inbound raw materials and outbound final products is essential to better control logistics costs. There is a rail renaissance underway in North America for the first time in almost 100 years. Railroads are pressing for advantages over their main competitor, long-haul trucking, which continues to struggle with rising fuel prices, driver shortages and highway congestion. The major railroads are now spending some $10 billion in improvements in operating systems and tracks.
Key Site Selection Issues
One key site selection issue today, which has become quite problematic, deals with higher energy costs that are impacting transportation costs at an unprecedented rate. All of a sudden, today’s cost of moving goods is the largest barrier to global trade. Should this issue continue, it could result in a significant slowdown in the growth of world trade, and also the future realignment in worldwide trade patterns. The U.S. could well be the benefactor of significant growth for types of manufacturing that have a high ratio of freight costs to final product selling prices.
Another key site selection criteria today that has become very problematic deals with data protection and loss prevention. Today’s business is about communication, and without access to the Internet, email, and landline and wireless phones, many businesses would likely struggle to remain successful. Broadband connectivity is now a must, and not just a need. Businesses must take extra precautions to protect their data.
Overall Site Selection Procedures
The typical overall site selection process for a given manufacturing related project for today follows these representative procedures:
• Establishment of the Project Team members from the company and the consultant. The members from the company will include at least Operations, Legal, Tax, Finance, Facilities, Human Resources, Environmental and Logistics.
• Development of a business plan, and comprehensive set of pertinent criteria, for the initial project’s requirements, and a typical 5-year probable growth plan.
• Logistics integration analysis for all inbound and outbound services.
• Determination of the geography of consideration (country, region, and specific locations).
• Initial evaluations of the location candidates within the selected geography of consideration. This initial evaluation process is elimination vs. selection oriented. The Internet and the consultant’s internal data bases are being used frequently.
• Direct meetings and discussions with the selected first-round candidates.
• Submittal of ‘Request for Information’ (RFI) documents to the selected first-round candidates.
• Review of the completed RFI documents, and selection of the second-round candidates. Submittal of ‘Request for Proposal’ (RFP) documents to the selected second-round candidates.
• Review of the completed RFP documents.
• Visits by the Project Team to the selected second-round candidates.
• Project Team’s continued evaluations of the selected second-round candidates and the determination of maybe three location candidate finalists.
• Return visits by the Project Team to the location candidate finalist; and the determination of the preferred location candidate, and the alternate location candidate.
• Negotiations for the final incentive package, including statutory and discretionary provisions.
• Preparation of the ‘Memorandum of Understanding’ (MOU), or a similar document(s), to be executed among all of the involved parties who have made certain commitments for the project.
• Determination of the project’s physical development process and the completion of issues regarding permitting, environmental, equipment relocation and/or installation, and management assessment/approaches for the cultural merging of the company and the new location.
Critical Needs
The need for accelerated timing for the overall site selection process for a given manufacturing related project is critical. The additional need to maintain confidentiality is essential for reasons of pre-mature disclosure to the public in general, awareness to competitors and disclosures to existing workforces.
One big issue which consultants, companies and governmental entities have to deal with today is relative to the “Freedom of Information Act.” When does a given project, and its details, have to become available for public review and scrutiny? Major pending deals must be kept quiet until they are consummated and not subject to change. This is a very challenging issue that will continue to be under scrutiny and challenge for years to come.
What Should be Done?
While the site selection process continues to be globally oriented, the U.S. should remain a leading world power in the manufacturing industry through the development of more capital intensive industries with smaller workforces, intellectual and technological achievement, and more advanced technology workforces. The U.S. is the most advanced, most forward looking, and most self-assured country in history; and the U.S. leads the world in creativity, and lack of overall regulations in the advanced Western World.
Today’s professionals, who are involved in site selection in the U.S., are more sophisticated “Jacks Of All Trades,” with the ability to integrate numerous human and technical resources to successfully accomplish various site selection processes.
The projections for world power positioning by the year 2030 are that countries such as China, India, Russia and Brazil will have more power, and that countries such as the U.S. and Western Europe will have less power. The U.S. is going to work harder than ever before to maintain its recognized world power position and to recruit and retain manufacturing related industries.
What strategy is required to further strengthen U.S. manufacturing? Risk minimization with multiple manufacturing sites which are close to customers’ markets and raw materials/components suppliers, reduction and maintenance of industrial tariff rates to sell and distribute more products outside of the U.S., stabilization and control of inflation to maintain competitive product costs, legal system and regulatory reform to allow companies to better operate in a democratic society, development of long-term sources of reliable and affordable energy, re-engineering and reenergizing all types and levels of workforce training, and improve programs and funding for all levels of public education.