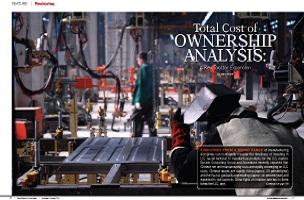
Executives from a broad range of manufacturing disciplines can confidently consider the timeliness of investing in U.S. based factories to manufacture products for the U.S. market. Boston Consulting Group and Accenture recently reported that Chinese net unit manufacturing costs are rapidly converging on U.S. costs. Chinese wages are rapidly rising (approx. 20 percent/year) and the Yuan is gradually appreciating (approx. six percent/year) and expected to rise faster as China fights an inflation rate two to three times the U.S. rate. So Chinese labor costs are rising rapidly and their productivity is, and will be, far below the U.S. level. As a result, by 2015 Chinese unit labor costs will be close enough to the U.S. level that the Chinese Total Cost of Ownership (TCO) will be higher than for the same products produced in lower cost U.S. states such as in the Southeast. (TCO includes the obvious direct costs such as the price plus all of the other costs, e.g. duty, freight, carrying cost, travel, etc., that impact the company’s P&L.) For this economic trend to have a rapid impact on the behavior of major U.S. companies, however, the companies will have to calculate their TCO. Unfortunately, most companies’ calculations are rudimentary, rather than complete, mainly comparing prices rather than the entire costs of offshoring. In fact, Archstone Consulting’s 2009 survey showed that 60 percent of manufacturers ignore 20 percent or more of the cost of offshoring. Accenture’s 2010 survey confirmed the results with 61 percent of respondents acknowledging the need to implement TCO. As a result, companies have offshored more than is in their own self interest. Total cost of ownership and other concepts and tools from the Reshoring Initiative help companies objectively decide which work to reshore and which to offshore.
Some commentators suggest we abandon the manufacture of high volume, relatively simple products and focus on low volume high tech products and processes. In contrast, I believe we have to recapture many of the high volume relatively simple products that have been offshored. My reasoning is twofold. First, much of the high volume, simple work can be made with low labor content processes. Second, there is not enough of the low volume work to balance the trade deficit and reduce unemployment and the budget deficit. One or more of the following must eventually happen: companies will develop a better understanding of the cost of offshoring; we will figure out how to be cost competitive; or the dollar will decline in value to the point where we are competitive, as the Chinese did so successfully, cutting the value of the Yuan vs. the U.S. dollar by about 80 percent between 1980 and 1994. Despite the strength, stability and rising productivity of the Chinese economy, the Yuan on July 12, 2011, was only back to the 1993 level and still 75 percent below the level of 1980.
Other commentators suggest we forget about manufacturing and, instead, become an “innovation” country. Recent studies show you cannot have the one without the other. Profs. Pisano and Shih of the Harvard Business School recently reaffirmed that U.S. innovation declines when manufacturing is offshored because the partnership of manufacturing and engineering is weakened. The TCO Estimator includes a cost factor for this impact and provides the comprehensive total cost calculation that can objectively justify keeping manufacturing close to U.S. engineering. Domestic manufacturing and innovation are thus mutually reinforcing.
These are some of the commonly overlooked cost factors involved in offshoring:
Rising wage rates, currencies and reject rates in developing countries
Duty and freight
Pipeline and surge inventory impacts on balance sheets and Just-in-Time (JIT) operations
Intellectual property and regulatory compliance risk
Higher transportation and fuel costs
Higher prototyping costs (U.S. shops charge more for prototypes because they will not get the production)
Higher end-of–life obsolete inventory costs because of higher inventories when the design is changed or the product life ends
Less effective innovation because manufacturing operations are distant from R&D and marketing (loss of clustering effectiveness)
Travel and personnel cost
Carbon footprint
Companies that calculate their TCO will discover that they could reshore substantial amounts of work and save money. The Reshoring Initiative's TCO Estimator software allows Original Equipment Managers (OEMs) to calculate and compare the total costs associated with outsourcing and offshoring. The Estimator includes 18 user-modifiable cost factors and makes it easy for an OEM to compare the full profitability impact of local versus offshore sourcing. The TCO is calculated for the present and then forecast based on user-projected wage inflation differentials and exchange rate changes. Job shops can use the Estimator to help their customers understand and calculate TCO.
For example, sourcing consultant Gibb River Group compared the U.S. and Chinese TCO of a low labor content, machined stainless steel gear. At FOB price level, the U.S. cost was 15 percent higher than the Chinese cost. However, costs were the same for producing the steel gear in each country after adding duty, freight, quality and inventory cost. The U.S. cost was 8 percent lower after allowing for end-of-life and prototyping cost differences - a 23 percent swing just by calculating cost correctly! Calculation of IP risk, proximity to R&D and carbon footprint would have widened the U.S. advantage even more.
The non-profit Reshoring Initiative helps close the gap with offshore manufacturing and support innovation now by helping U.S. companies understand their true cost of offshoring: their Total Cost of Ownership. With clear evidence of the fragility of global supply chains, Chinese and other LLCC wages rising rapidly, the U.S. dollar declining and oil soaring, this is the perfect time for U.S. companies to reevaluate their offshoring strategies and bring some of the sourcing home.
The Reshoring Initiative offers a non-protectionist, efficient way to reduce our imports, increase our "net exports" and regain manufacturing jobs. To help companies make better sourcing decisions the Reshoring Initiative provides:
Free Total Cost of Ownership software that helps them calculate the real offshoring impact on their P&L,
Publicity to drive the reshoring trend,
An online Library of 98 articles about successful reshorings, and
Access to NTMA/PMA Contract Manufacturing Purchasing Fairs to help them find competitive U.S. sources.
The Initiative has received increasing visibility and influence: recognition by Industry Week magazine via its 2010 Manufacturing Hall of Fame; inclusion of the TCO concept in Cong. Wolf’s (R VA) “Bring Jobs Back to America Act” (H.R.516); numerous webinars; dozens of industry articles; presentations in major industry and government policy conferences in Chicago and Washington, DC; and coverage by CBS, CNBC, WSJ, CNN, Fortune and USATODAY.
An integrated 5-step Illinois Reshoring Initiative has been launched to demonstrate the Initiative’s effectiveness. One step is the Sept 8, 2011, NTMA/PMA Contract Manufacturing Purchasing Fair at which customers can find competitive U.S. sources. We anticipate improving companies’ profitability while bringing “permanent” manufacturing jobs back at a cost of $1,000 each, less than one percent of the cost of one year Stimulus Program government jobs.
On July 22, I met in Washington, DC, with the Commerce Department’s SelectUSA which encourages FDI (foreign direct investment) and increased domestic investment by U.S. companies. SelectUSA is quite interested in reshoring. We discussed SelectUSA’s distributing the tools of the Reshoring Initiative to economic development groups across the country.
Other developments at the Reshoring Initiative since my last article in Trade & Industry Development include:
TCO Version 5 was released with the capability to calculate costs from 17 countries.
We will make approximately 100 presentations nationwide this year: conferences, trade shows, company events, TV, radio, etc.
The Reshoring Library will expand greatly in detail and in number of articles by September.
A much needed new website will launch in August at the same URL: www.reshorenow.org.
Affiliated groups are being formed in the Midwest and in NY/NJ.
The Initiative now has 14 sponsoring trade associations and companies.
We are considering a Washington, DC-based conference that would bring together reshoring and the groups that either strengthen reshoring or are strengthened by reshoring. The groups might include: innovation, technology suppliers, green, labor and minority representatives.
Reshoring is the most cost effective way to stimulate the economy. Exporting is much more difficult because it requires the U.S. company to bear all of the “hidden” TCO costs. Government spending programs and tax reductions are ways to slice the pie differently. Neither is accomplished timely. Reshoring grows the pie, reducing the need for pie slicing. The current U.S. trade deficit is about $550 billion per year. Balancing the trade deficit by reshoring will:
Bring back about three million manufacturing jobs and four to five million multiplier effect jobs for those who supply materials and services to the manufacturing companies and workers: at least seven million total.
Reduce unemployment from above nine percent to below five percent.
Dramatically reduce federal, state and local budget deficits by increasing tax revenue and reducing unemployment and other expenditures.
Strengthen our defense industry capability.
The basis for globalization, the effectiveness of Ricardian comparative advantage, has even been called into question. Prof. Autor of MIT and NBER has concluded that the total cost to our country for unemployment and other costs due to offshoring are about as high as the savings due to lower prices due to offshoring. We wind up with a hollowed out economy and no savings.
Here are ways you can help:
Large companies: improve profitability, and simplify and de-risk your supply chain, by reevaluating offshoring decisions using the Estimator.
Suppliers: use the Estimator to convince your customers to reshore.
Both: Ask for help from the Initiative, propose local Reshoring Initiatives and send me successful reshoring cases to be publicized.
Learn more at free reshoring webinars. Four are scheduled in August, including an Industry Week hosted Zurich America webinar on how reshoring can play a role in reducing supply chain risk management. Links are at the Initiative website.
Sponsor the Reshoring Initiative.
Together we can bring more manufacturing back now!
The Reshoring Initiative, www.reshorenow.org, is supported by: the Association for Manufacturing Technology (AMT) www.amtonline.org; Sescoi, www.sescoi.com; GF AgieCharmilles, www.gfac.com/us; the Association for Manufacturing Excellence (AME), www.AME.org; the National Tooling and Machining Association (NTMA), www.ntma.org; BIGKaiser, www.bigkaiser.com; Mazak, www.mazakusa.com; TCI Precision Metals, www.tciprecision.com; Science of Business, www.VelocitySchedulingSystem.com; Doosan, www.infracoremt.com; the Swiss Machine Tool Society (SMTS), www.smts.org; Hand Tools Institute (HTI), www.hti.org; and IBS, www.ibs-us.com. Additional information on the NTMA/PMA Purchasing Fairs can be found at www.purchasingfair.com. Additional information on the Illinois Reshoring Initiative is at www.illinoisreshoring.org.