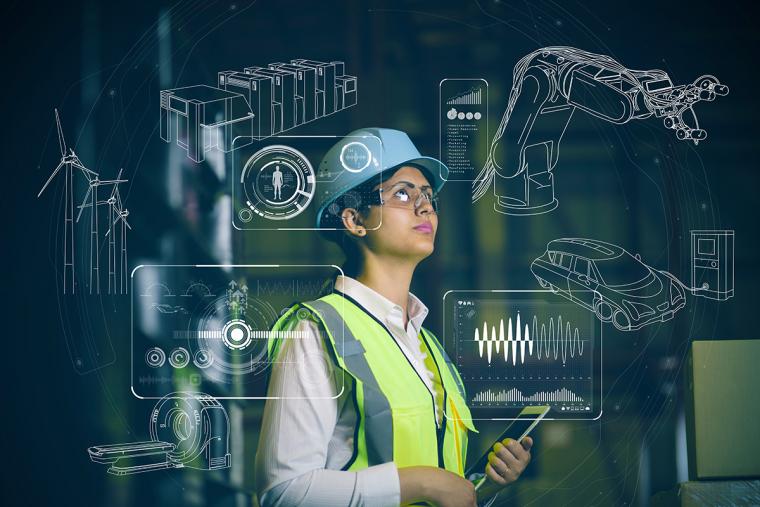
Countless articles have dissected how manufacturers and their site selectors make location decisions and which factors typically drive those decisions. Anyone who has been part of the location and economic development world for at least a few years has read or heard that a manufacturer’s location decisions are driven by:
• Access to customers, raw materials, suppliers, services;
• Access to workers/skills/talent with the necessary capabilities, availability, and quality;
• Variable operating costs, ranked differently by type process or operation: workforce, freight, utilities, taxes real estate;
• Availability of high-quality utility and road infrastructure that meet current and future requirements;
• Availability of suitable real estate – buildings or sites;
• Potential for economic development incentives.
These concepts are regularly discussed and well understood. What is less discussed, and varies over time, are the less-direct issues and trends that also directly impact whether, how and where companies locate their new operations. Following, some of those issues are explored from the viewpoint of a site selector in 2018 and how these issues may impact location strategy and site selection decisions over the next few years.
It would take many articles to fully explore any one of these topics, so take this as an overview of trends that economic developers and site selectors will be wrestling with now and in the near future when siting and attracting manufacturing investment.
Re-ordering Manufacturing Critical Location Factors: Access to Low-Cost Labor Wanes, Access to Everything Else Waxes
For decades, much of the battle to attract and retain manufacturing was focused on the ability to hire low-cost labor. While other variables were also important, it was low-cost, qualified labor that defined the great shifts of manufacturing. But then the pace of technology changed, automation mushroomed and with it, the demand for low-cost/lower-skilled labor was steadily eclipsed by the demand for highly technical skills and creative talent.
Access to a skilled workforce still drives most manufacturing and the cost of the workforce is still a focus. What has changed is the labor component portion of the overall operating cost picture tends to decline as technology and automation investment increases. While the focus on labor costs lessens in the site selection search, other location variables become equally or more important.
For many manufactured products, access to the market — customers and suppliers — has become even more important. Cost and speed to market provide a competitive edge, especially when labor content and costs decrease as they are digitized and automated. When the labor content of a manufactured product is not significantly higher in the U.S. than in China because of technology investment, then driving down other costs, such as logistics and improving speed to market, become paramount for manufacturers.
Likewise, access to robust, high-capacity infrastructure increases in importance as labor content decreases. As labor costs’ influence on the overall variable cost equation declines, the importance of utility costs and quality rises, doubly so since automation typically requires more robust utilities.
The same is true for transportation and real estate infrastructure. Access to high-quality roads, airports, rail and ports, along with superior logistics providers, become more of a focus and expectation. Manufacturers demand and expect sites and buildings that are fully served by high-capacity utilities and transportation services that are flexible to grow and change as the company’s processes and technology evolve. An area’s ability to provide these essentials becomes more of an advantage as the focus on low-cost labor recedes.
The Quest for Talent: Companies Go to the Worker, Not the Worker to the Company
Throughout the Great Recession, the political and economic development mantra was jobs, jobs, jobs. Unemployment was high throughout much of the country and, at least on paper, there was a huge pool of qualified workers looking for jobs; it should have been a buyer’s market for companies. For some, it was. But for most manufacturing companies, within that great pool of unemployed they found few qualified, skilled workers. Now, well into the recovery, that problem is getting progressively worse. Why? While skilled and talented people have always been in demand, the massive manufacturing technology evolution and incredible pace of change in technical skill demands, paired with the steady loss of skilled workers to retirement or career change, has created a huge gap between the supply and demand of workers qualified and prepared to succeed in today’s highly technical manufacturing jobs.
Lower-skilled, repetitive task jobs have been steadily removed from the manufacturing workforce. While this has caused significant job loss, it has also created an enormous demand for new and more technical skills. It has also created new jobs that are needed to operate and program complex machines, maintain applications and systems, troubleshoot shop floor technology issues and repair complex automation devices and machines. Today’s manufacturers require workers to multitask, filling the roles formerly occupied by several, if not many, workers. Supervisors and management also require updated skills so they can understand and manage new and highly technical processes, and the skilled workers they require, including how those workers interact with robots and other forms of automation and how to manage the vast amounts of data emanating from their complex manufacturing processes.
In today’s manufacturing job market, it’s a seller’s market. Highly talented and skilled workers get to make choices like almost never before about where, when, how and with whom they will work. Today’s top talent is no longer limited to the positions offered by an industry or company wherever they may be, and has become extremely discerning about the quality of the workplace and the community in which it is located. Highly skilled and talented workers are demanding more independence and flexibility in the workplace and are seeking companies with values that align with their own. They are also seeking communities with the quality of life they desire as much, if not more, than the company or job itself. Consequently, with fewer workers willing to simply follow the job, more companies must follow the talent. Great places attract great talent, which in turn, attract great companies.
Artificial Intelligence: The Automated and Robot Workforce
We have all read the warnings of the coming massive workforce disruption resulting from the exponential growth of AI and robotics. A report by the McKinsey Global Institute predicts that potentially over 70 million current jobs in the U.S. could be lost to automation in the coming years. In 2017, U.S. companies bought at least 30 percent more robots than they did in 2016. Manufacturers are installing robots and other forms of AI and automation rapidly to not only reduce long-term costs, but to increase productivity and efficiency and improve their speed to market.
AI and robotics will no doubt disrupt the workforce. Many of today’s manufacturing jobs in their present form will disappear. It is important, though, to remember that this is nothing new; automation and job disruption have been a constant since the beginning of the Industrial Revolution. While the pace of change is perhaps faster today, automation, along with its disruption of the manufacturing worker, has been with us for well over 100 years.
It is also important to remember that while jobs and entire occupations will disappear, many jobs will evolve with training into different jobs, and other new jobs will be created. The same McKinsey report implies that at least a quarter of the workers displaced by coming AI and automation will probably find work relatively easily in similar occupations, and if not, will retrain and work in new occupations, perhaps in the same industry or company. This new generation of manufacturing workers will learn to build, program, monitor, calibrate, maintain and repair the automated machines or so-called “no-collar workers,” and over time, the human workers will learn to seamlessly work together with the machines.
Many of the manufacturing tasks AI and robots are replacing are physically difficult, time-consuming, repetitive and often boring or uninteresting for most workers. Other tasks executed by AI and robots are simply beyond the ability of human workers to perform. As these forms of automation inevitably replace these jobs, the human workers will move into other positions that require other skills that are more difficult (presently) for machines to execute, such as jobs that require communication, negotiation, empathy, collaboration and emotional intelligence as part of problem-solving for broader issues. Human workers will be developing the applications and entirely new processes that efficiently leverage the best abilities of human and machine workers, finding new ways for the two to integrate and collaborate to improve efficiency and quality. Human workers will continue to perfect the design, construction and applications of the no-collar workers.
Human workers, through education and training, will learn new skills across a broader range of tasks and activities, knowing their jobs will require ongoing training, and will continue to evolve over time as AI advances. Manufacturers and society as a whole will develop new and innovative ways to develop the skills of people as we adjust to the realities of AI, robots, the Internet of Things, cognitive technologies and augmented reality and their many applications to products and processes.
The Gig Economy: Decentralization of the Workforce and Production
If you are sensing that all things workforce is the key issue most manufacturers are dealing with, you are correct. Rapidly evolving changes in the type of skills manufacturers need, combined with the retirement of older skilled works has manufacturers scrambling and testing workforce alternatives. In addition to finding locations where the best skills live and combining them with AI and robotics, another emerging strategy is engaging the so-called gig worker.
The trend to using independent contractors and temporary positions has been used by manufacturers for years, but the technical talent shortage has created a new twist. Whereas independent contractors have long been used for new process or equipment installations, and temporary positions were typically low-skilled positions hired for busy seasons, more companies are experimenting with engaging highly skilled workers as contractors or temps on specific technical tasks or short-term projects.
The skilled people companies need are in demand, mobile and increasingly live in specific cities or areas. If the manufacturer is not located where this talent is and cannot practically place an operation in those locations, it may still be able to tap into the technical talent pool virtually for tasks or projects that do not require the talent to be in the plant, or at least not that often. This strategy potentially opens manufacturers up to a wide network of design, engineering, programming, project management and other technical and managerial skills. It can also be an effective alternative for traditional high-skilled manufacturing positions like machinists, toolmakers, electricians and equipment maintenance. Companies can source this talent from consultants, freelancers and possibly even suppliers and customers to find the skills needed for specific technical matters. This talent will often possess different perspectives, gathered from other companies and industries, bringing breadth and depth to technical challenges and problem-solving.
Today’s manufacturing shop floor increasingly requires complex problem-solving skills that make the traditional factory worker more difficult to engage. By outsourcing the more complex tasks to gig workers, manufacturers can fill the gaps. Like the traditional temp worker, this model can be effective in industries experiencing seasonality and uneven demand, such as food processing, vehicle manufacturing and various consumer products.
Some of a company’s gig workers may seek to join full time, allowing the company a testing period before it commits to adding highly paid skills to its payroll and benefits system. While not traditional or as easy to manage, there are services developing just for the gig economy, matching tasks and projects to workers. T&ID