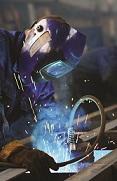
For thousands of years, metalworking has been a key component of the development and assembly of goods and structures. Metalwork is the basic process of shaping metal into different parts and assembling or creating metal structures. This could include working with transportation vehicles, such as ships, airplanes and automobiles, as well as large structures such as bridges and buildings. The fabrication involves building large metal objects through cutting, bending and other processes.
As humans have advanced over time, innovations and discoveries in metalworking have been vital. Today, metalworking, while maybe not on the forefront as other sectors, is still a critical industry around the world. In the United States, metal, particularly steel, is utilized and relied upon to continue the nation's economic growth.
U.S. Steel Industry
In manufacturing, the U.S. steel industry is still a critical component to the industry’s success. Many sectors depend on steel for their operations, such as construction and automotive – two sectors primed for the nation’s growth. In 2015, the U.S. steel industry operates over 100 production facilities and factories across the country. The industry produced close to 100 million tons in 2014 with a total value of approximately $75 billion. Currently, the industry employs 150,000 people across a number of states and supports more than one million jobs nationwide. One of the aspects that propels the growth of the steel industry is the success of the end users. The construction sector is a perfect example because it’s considered the biggest steel consumer in the U.S. market.
Chemically, steel is defined as an alloy that contains a high proportion of iron combined with a certain amount of carbon. The properties of steel such as formability, durability, strengths, thermal conductivity and others depend on varying proportion of the elements added during its manufacturing. Steel is considered the most important metal in today’s market and its high strength makes it an essential part of infrastructure and machinery.
The manufacturing of steel is the basic process of converting iron ore to steel through two steps: producing molten iron and manufacturing the actual steel. The production of molten iron involved mixing with limestone and coal then the mixture is headed (a metalworking process). The result is reduced to metallic iron that melts and impurities are removed. The molten iron goes through a vanadium recovery and a process called KOBM, the acronym for Klockner Oxygen Blown Maxhutte (steel-making furnace). The process oxidizes dissolved impurities by blowing oxygen through the molten metal. Last, fine adjustments are made to bring the molten steel to the required composition.
Metal and the Automotive Industry
The automotive industry depends heavily on metal and its availability in the market as it plays a crucial role in the manufacturing process of vehicles. Steel is one type of metal used in the creation of vehicles, and it brings many benefits to the vehicle lifecycle. Specifically, steel benefits a vehicle in three key ways: manufacturing, driving and end-of-life recycling.
Modern car manufacturers depend heavily on steel to protect the passengers due to the metal’s strength, durability and dependability. Cars are still the most relied-upon mode of transportation, and owners trust in the strength and toughness of the vehicle. Steel is being used increasingly in new vehicles, partly because it is easily accessible and available to manufacturers. Additionally, it has the highest strength to weight ratio of any building material with consistent quality.
With a focus on sustainability, steel is also recyclable, thus reducing the carbon footprint of future manufacturing. Each year, the steel industry recycles enough to power more than 18 million homes for 12 months. In today’s passenger car, 60 percent of the vehicle is steel, and more than 25 percent of that is recycled. Going forward, the industry is expected to provide further sustainability benefits and climate solutions.
Supply Chain of Steel
The supply chain of steel manufacturing still depends heavily on access to raw materials. In most cases, one will find steel manufacturers more proximate to the raw materials than to the consumers. For steel, the primary raw material is iron ore, which is now produced at sites around the world. Close proximity to suppliers not only ensures a reliable source, but also significantly reduces time and transportation costs.
In many industries, supply chain managers prefer to keep inventory low. However, the steel industry functions in a different manner as the product is produced over several stages and the supply chain is part of an ongoing process. Iron ore is initially formed before moving to further processing and completed into the finished product. It’s important for managers to keep additional inventory in case a shutdown or an operation break occurs. With the additional inventory, the company can continue operating through a variety of disruptions.
Being considered a commodity throughout the entire process, today’s steel supply chain managers need to utilize sophisticated logistics tools and best practices. For example, supply chain concepts such as contract management, commodity pricing and hedging are critical to an effective and fluid logistics process.
Finally, the supply chain management of steel manufacturing operations requires continuous innovation and improvements. The biggest challenges are faced in the storage and transportation of the raw materials, as well as the finished goods. Weighing between one and 25 tons, steel can present a number of challenges, not to mention the inefficiency of treating all goods in a similar fashion. Around the world, engineers, scientists and supply chain experts are investing in and studying new methods and practices to make the process more efficient and cost-friendly.
Changing the Future: Innovative Processes
Metal Laser Cutting
Laser cutting is the process of cutting certain types of metal and is being used largely in the manufacturing industry. The process of cutting may be done through burning, melting or blowing and works for different types and shapes such as flat sheet, structural or piping metals. Standing for “Light Amplification by Stimulated Emission of Radiation,” the laser beam is generated by stimulating a lasing material by electrical discharges, while all being contained in a closed environment. There are many discovered methods to do so such as thermal stress cracking, melt and blow, scribing, cold cutting and vaporization.
From a manufacturing perspective, laser cutting has many benefits and few drawbacks when used in mechanical cutting. Overall, the process produces cleaner and more precise cuts, as well as quicker production, which ensures minimum interference in operation. The main benefit of laser cutting is that it can duplicate the same pieces and parts with great consistency and precision.
One drawback is the possible contamination of the machines by cutting certain materials, which could ultimately affect the life of the machine. An additional challenge can be on the energy side, as laser cutting may require a significant power source and involves a cooling mechanism.
3D Printing
3D printing technology has seen incredible development over recent years and now works with many materials and surfaces. However, 3D printing on metal wasn’t always a real solution as it was a challenging task for the manufacturing industry at the outset. In fact, the first attempt of 3D printing on metal goes back to the late 19th century when welders used electrode arcs to blend metal together. Eventually, the introduction of electron beams and vacuum chambers made 3D printing more sophisticated and possible on metal. Today, the most important technology that has enabled further development in 3D printing on metal is laser. Lasers enable the process to be more precise, detailed and timely.
The method of 3D printing on metals varies depending on the size, shape and details of the object printed. The basic process is dumping a powder metal matrix that contains binders, which creates layers. The outcome is melted and the metal is temporarily held together until it is baked in an oven. The object that’s required could be printed as a whole or a shell could be printed and used to shape metals of a lower melting degree. The development of 3D printing is still in its earliest stages, as the true uses of the technology are only beginning to be realized.
Help Wanted
Throughout the metalworking industries, there is a sharp need for trained and skilled employees to enter the workforce. According to a study conducted earlier this year by the National Tooling and Machining Association (NTMA), 84 percent of its member companies report having skilled positions open at their facilities, with a great shortage of engineers. Meanwhile, a similar organization, the Precision Metalworking Association (PMA), found that nearly 70 percent of its member companies have a workforce with an average age of 41 to 60 years old. When it comes to recruitment, those same companies almost unanimously reported moderate to severe trouble finding new workers.
There are ongoing efforts around the country to offset this problem and encourage more individuals to enter the industry. Through community colleges and technical schools, the American workforce is finding more opportunities for education programs and apprenticeship opportunities. At the engineer level, there is a push for the establishment of more university-level programs. Earlier this year, a bipartisan bill was introduced in the U.S. Senate, the “Manufacturing Universities Act,” calling upon the National Institute of Standards and Technology (NIST) to designate up to 25 academic institutions as U.S. manufacturing universities. Federal funds will then directly assist in the development of engineering programs alongside the manufacturing industry.
Location Strategy
When determining where best to locate a metalworking facility, there are a number of key factors that must be considered in the site decision. At the outset, these factors include access to and availability of raw materials, particularly products such as iron ore. While the proximity to the materials can vastly impact the time and costs for procurement, transportation requirements are critical to the site needs, especially freight rail. Throughout the U.S., rail is still a key component in the nation's infrastructure, and can be essential for a facility’s ultimate success.
As previously mentioned, the ability to find and recruit the necessary workforce for a facility is important in the site selection process. Certain regions will present both opportunities and challenges in discovering the employees needed for a facility, particularly when it comes to engineers and skilled metalworkers. An in-depth labor analytical study needs to be conducted to ensure the site will have the skills available immediately, as well as for the long term.
Another critical aspect to be reviewed is utilities. With energy being a significant driver in the metalworking process, a site strategy must take into consideration the type of energy, expected rates and reliability of the source. Additionally, all of the environmental ordinances that may be in place at the federal, regional, state and local levels must be reviewed per the specific use of the facility. These regulations can vary greatly dependent on the actual location of the site.
In the end, the proximity to the customer should be considered in the final site decision. However, among all the other factors, the customer location may not be as vital if the logistics, labor, environmental and operational costs are all understood and meet the facility’s needs.
Looking Ahead
As the global economy evolves toward the future, metalworking is still a critical industry and vital to the American economy. In an age of technological innovation, new methods utilizing lasers and 3D printing are set to revolutionize the industry. Unfortunately, there are a number of challenges yet to be overcome to ensure the industry’s success, with the future workforce on the forefront.