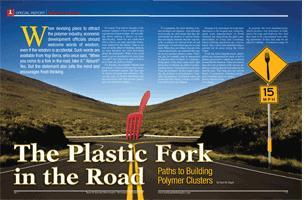
When devising plans to attract the polymer industry, economic development officials should welcome words of wisdom, even if the wisdom is accidental. Such words are available from Yogi Berra, who once said, “When you come to a fork in the road, take it.” Absurd? Yes. But the statement also jolts the mind and encourages fresh thinking.
Of course Yogi had no thought of the polymer industry or how it might fit into regional development plans. He was talking about making a choice (or not). Specifically, when we are confronted with a choice, we may reject the limitations implied by the choice. That is, we may set aside either/or thinking. Instead, we may broaden our view and think about the destination. What if we could reach a given destination by more than one path? And what if we were to follow more than one path at a time?
For decades, the polymer industry has presented a choice between two basic kinds of polymer cluster. The first type of cluster develops near refineries. The second type of cluster develops near manufacturers that incorporate plastic parts into finished products.
To consumers, the most familiar polymer products are plastics. And although most people are well aware that they are surrounded by plastics of various kinds, they are largely unaware that the vast majority of plastics are derived from oil and natural gas. Oil and natural gas are not just fuels. When they are refined, they provide various feed stocks, raw materials that maybe used to produce plastics resins. Ethylene gas, for example, may be transported by pipeline from a refinery to a manufacturing plant. At the plant, many small, light molecules of ethylene are linked together, forming heavy, long-chained molecules. These are polymers. (In this simple example, the polymer is polyethylene.) Typically, the polymers, or polymer resins, are processed into liquid, powder or pellet form before they are shipped.
Because it is convenient for resin manufacturers to be located near refineries, many resin manufacturers in North America are sited along the gulf coast, particularly in Texas and Louisiana, where refining operations are concentrated. Also, some resin manufacturing is carried out in areas along the Great Lakes.
From the resin manufacturers, plastic pellets are transported by truck or rail to plastics processors, which are scattered around North America. These processors may mix raw polymers with various additives, creating special formulations for specific uses. They may also use various kinds of equipment, including molds and extruding units, to create plastic objects of various shapes.
In general, the resin manufacturers, which produce raw polymers in bulk, tend to be large and relatively few. And they tend to be concentrated near refining operations. In fact, they may be adjuncts to refining operations, divisions of energy companies. In contrast, plastics processors tend to be smaller and more numerous. Also, they tend to be more specialized, creating products designed to suit other manufacturers, such as automobile assemblers.
Plastics processors locate near their customers. By doing this, the plastics processor is better positioned to conform to the customer’s “just in time” sourcing preferences. Also, the plastic processor may reduce shipping costs. This is an important consideration for plastics processors, which may create parts that do not pack densely. In other words, plastics processors may pay a lot to essentially “ship air.”
There has even been speculation that plastics processors located abroad, which certainly includes low-cost operations in China, are significantly disadvantaged by the costs of shipping plastic parts. Plastics processors in China are much more likely to supply manufacturers in China than manufacturers in North America.
Within North America, plastics processors, like many other manufacturing concerns, have been shifting operations to the south. A large contributor to this trend is the need to follow automobile manufacturing. Many plastics processors are still in the north. But many are locating in southern states, the better to serve transplants, foreign-owned auto assembly plants that produce cars for the North American market.
As this trend progresses, it becomes, in some respects, easier to sustain. Plastics processors do not mind locating near competitors. In fact, they see advantages to locating near dense concentrations of polymer activity. Dense polymer clusters are more likely to support providers of specialized equipment. In addition, workers with the appropriate training and experience are more available.
As characterized thus far, the polymer industry and its site selection priorities suggest nothing so much as stability. Indeed, this perception is reinforced by statistics provided by the Society of Plastics Industries, an association that periodically updates its state-by-state rankings of polymer manufacturing and processing activities. Occasionally, a state moves up or down a notch or two, but the overall pattern remains much the same.
For example, California remains the leader in various categories, despite persistent grumbling about its’ costs and aggressive enforcement of environmental standards. So, when news arrives that yet another polymers processor has moved to a neighboring state – escaping the California orbit while remaining close enough to serve California-based customers – one is reminded of another one of Yogi Berra’s nostrums: “Nobody goes there anymore on account of it being so crowded.” Yes, sounds like polymers in California.
Yet it would be too easy to overstate the constancy of the polymer industry. Yes, it is large and mature. And it is balanced in the sense that plastics are integral to varied industries. There are, for example, applications in automobiles, aerospace, electronics, medical equipment, packaging and so on. But the plastics industry has the potential to undergo fundamental, even disruptive, change. Such change could influence site selection criteria, as well as the policies implemented by development authorities.
The main reason to anticipate change in the polymer industry is this: the costs of oil and natural gas – the industry’s essential feed stocks – keep rising. This trend, which shows no sign of abating, is bound to cause complications. The polymer industry is characterized by low margins as it is.
Other pressures on the polymer industry include long-term efforts to move from commodity products to specialty products. In general, development authorities would like to encourage this transition. Commodity operations, largely because of pricing constraints, tend to become increasingly automated, making them less attractive as job engines. Also, sensitivity to costs makes it difficult for local authorities to implement policies to protect the environment.
Specialty products, it is hoped, would command higher margins and employ a workforce possessing increasingly diverse, sophisticated and more highly compensated skills. In addition, innovations in the polymer industry may offer solutions to other problems. These include the rising costs of procuring traditional feed stocks, implementing policies to limit hazardous wastes and disposing of used plastics in landfills.
Innovation in the polymer industry may follow the disruptive pattern outlined by analyst Clayton Christensen. According to Christensen, disruptive innovations may occur when two distinct constituencies – incumbents and upstarts – pursue different technological strategies. In this scenario, incumbents continue to refine tried-and-true technology that has already been applied profitably and that already dominate the most lucrative market segments.
The upstarts, however, concentrate on market segments overlooked or underserved by the incumbents. Typically, these segments are found at the very low and the very high ends. At the low end, upstarts may deploy technology that is less impressive, less capable, but that serves the needs of the least-sophisticated (and, possibly, most cost-sensitive)customers. At the high end, upstarts may deploy highly sophisticated technology too costly or too specialized for general use.
For the upstarts, these hardscrabble or esoteric niches serve as footholds. Given time, the upstarts may ascend to more profitable reaches. They may refine their technological approaches enough to make them suitable for mainstream applications. If this happens, the upstarts may force the incumbents aside.
For this threat to the fortunes of incumbents, Christensen has a name: the innovator’s dilemma. Incumbents must monitor the capabilities of upstarts and, if necessary, appropriate the upstart innovations, even if this means cannibalizing themselves, sacrificing near-term profits and undermining their own hard-won technological advantage. Incumbents may spin-off divisions that develop their own upstart strategies or they may simply acquire promising (and potentially threatening) startup companies.
It sometimes happens that incumbents remain blind to threats and fail to act until it is too late. Business history is littered with examples. Sailing ships were overtaken by steamships. The telegraph was no match for telephony. Mainframes were largely supplanted by minicomputers and workstations, which were in turn supplanted by personal computers. Vertically integrated steel mills struggled while mini steel mills thrived. The list goes on.
In the polymer industry, several developments may lead to disruptive, industry-changing innovation. These include plant-based plastics, biodegradable plastics, plastics compatible with biological tissues, plastics capable of conducting electricity and novel materials combining plastic and nano-engineered components. These innovations, aside from a few special, limited applications, are not yet ready for commercialization. However, these innovations are being developed by several institutions, some of which enjoy public support. Examples from several states are listed below:
Massachusetts
Center for Advanced Engineering Fibers and Films, Clemson University and MIT
Polymer Science and Engineering, University of Massachusetts Amherst
Mississippi
University of Southern Mississippi
New Jersey
Center for Advanced Materials Through Immiscible Polymer Processing, Rutgers
Medical Device Concept Laboratory, New Jersey Institute of Technology
Polymer Processing Institute, New Jersey Institute of Technology
New York
Center for Integrated Manufacturing Studies, Rochester Institute of Technology
Cornell Center for Material Research
Polytechnic University (Brooklyn)
Ohio
Case Western Reserve University
Ohio State University
University of Cincinnati
Pennsylvania
Emulsion Polymers Institute, Lehigh University
Plastics Technology Center, Penn State-Erie Behrend College.
Institutions such as these recognize that the innovator’s dilemma confronts not only individual businesses, but local, state and regional economies too. So, while economic development authorities stay attuned to the needs of today’s polymer industry, they are also trying to position themselves as platforms for the polymer industry of the future.
At present, for the great majority of polymer companies, site selection depends on a familiar collection of attributes: proximity to raw materials (for plastics manufacturers) or key markets (for plastics processors), well-developed transportation infrastructure, availability of a quality workforce, low utility rates, favorable tax rates, a tolerable regulatory regime and various incentives. Less critical, though still important, attributes include quality of life and educational resources. These “nice to have” attributes, however, may be critical to upstart companies. Indeed, upstarts focused on disruptive innovation probably would not be content with academic programs limited to extension programs. They may want to be near top-ranked research institutions, and they may be interested in gauging a locality’s commitment to supporting business incubators and technology parks.
A serious reconfiguration of the polymer industry may seem far-fetched or at best a distant prospect. After all, plastics based on oil and natural gas remain far cheaper and more capable than plant-based plastics. Plus the production of traditional plastics is supported by extensive physical and social infrastructure. Finally, sustaining innovations may make it possible to conserve increasingly expensive feed stocks. For example, new catalysts may permit milder processing conditions.
All the same, events may accelerate disruptive trends. It has happened before. The polymer industry as we know it got a boost during World War II, when North America lost access to rubber from Southeast Asia. To replace rubber, synthetic polymers were developed. Leaders in this transition were the tire manufacturers in Ohio. When the tire industry in Ohio waned in the 1980s, Ohio’s polymer expertise remained. Today, Ohio is a leader in the processing and distribution of polymers.
Could prohibitively expensive oil and natural gas hasten a similar change in the near future? If so, we might remember another quote from Yogi Berra: “It’s like déjà vu all over again.”