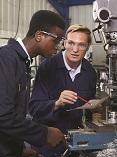
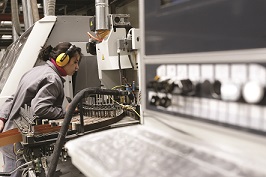
One of the most heavily debated issues in the advanced manufacturing industry today is the notion of a “skills gap” that poses a significant challenge to the growth of the U.S. manufacturing sector. Extensive research has been conducted on this topic by many respected firms, often reaching significantly different conclusions about the scope of the problem. In the Manufacturing Institute’s most recent Skills Gap Report, a joint study conducted with Deloitte Development, LLC that surveyed over 1,000 U.S. manufacturers, 93 percent of the respondents indicated they think there is a shortage (ranging from low to moderate) in the availability of workers across all job categories. These shortages were most pronounced in the areas of skilled production jobs such as machinists and technicians. Of importance, 56 percent of respondents indicated they expect the shortage in overall workers to increase over the next three to five years. The Manufacturing Institute/Deloitte report estimates these circumstances contribute to approximately 600,000 manufacturing jobs going unfilled in the U.S.
Illustrating that highly respected firms can reach significantly different conclusions on the scope of the current manufacturing jobs shortage, a 2012 study conducted by the Boston Consulting Group (BCG) titled “Made in America, Again: Understanding the U.S. Manufacturing Skills Gap and How to Close It,” estimated the current manufacturing worker shortage at approximately 80,000 to 100,000 jobs. However, the BCG study went on to state there is the potential for a substantial increase in the shortage of manufacturing workers by 2020 as a result of factors including the retirement of aging workers and a possible influx of manufacturing jobs associated with reshoring of manufacturing operations.
While experts may disagree about the scope of the skills gap facing the advanced manufacturing industry and the associated shortage of qualified workers, there is a general consensus that a significant skills gap does exist and that action needs to be taken to prevent the problem from becoming worse and ideally to reduce the skills gap over time. This circumstance presents both challenges and opportunities for the public sector, academia and private industry. In many cases, states and regions are investing heavily in workforce solutions to address skills gaps (particularly in the manufacturing industry) in an effort to create the most competitive business environment possible. This also creates an opportunity for site selection professionals to add value to their clients by identifying potential resources to help clients identify resources to recruit employees and invest in their own workforce, either by direct incentive support or by participating in workforce development initiatives or by participating in programs led by other groups. Following is a discussion of various programs that have been implemented in various markets throughout the United States. An understanding of the general framework of such programs is useful in identifying resources available in a given market.
One step companies can take to enhance their ability to attract and retain qualified talent is by identifying prospects at an earlier age, rather than waiting to begin the recruitment process closer to high school or college graduation. Despite significant efforts by the public sector and private industry, some negative misperceptions about the manufacturing industry still persist. Regrettably, these misperceptions can be difficult to overcome by the time a student has completed their education. Efforts to correct the notions that manufacturing work may be mundane or unsafe have made progress, but there is still more work to be done. Apprenticeship programs are one way to instill an interest in manufacturing in students at a young age and also to promote competency in the disciplines the student would need to possess to become a regular employee of the company.
Several states have recognized the value of apprenticeship programs and now offer tax credits to companies to incentivize the development of such programs. Examples of states offering apprenticeship tax credits include Connecticut, Indiana, Louisiana, Missouri, Rhode Island, South Carolina and West Virginia. The amount of these credits is typically calculated as a percentage of new wages or withholdings associated with the hiring of new apprentices, up to a certain dollar amount cap. The credits are usually awarded over a period of several years, which varies by the state issuing the credit.
In addition to financial incentives designed to offset the cost of implementing an apprenticeship program, resources are also available to assist in the organizational aspects of setting up the program, often through the community college system, non-profit organization or industry association. Examples of industry associations that can assist in establishing an apprenticeship program are the National Tooling and Machining Association (NTMA), which operates through approximately 50 local chapters, and the Ohio-based Precision Metalforming Association (PMA), which serves a nationwide membership base. These groups represent companies practicing disciplines such as tool and die making, CNC machining and operating and precision custom manufacturing. These disciplines are particularly noteworthy because they represent areas in which there are often significant regional skills gaps and workforce shortages. Additionally, these are positions that often offer very competitive wage levels, which support the public policy objective of helping citizens enhance their earning potential and improve their quality of life. An example of an advanced manufacturing apprenticeship program in action is the Arizona Precision Manufacturing Apprenticeship Program (AzMAP). Illustrating the importance of broad-based collaboration to the success of these initiatives, organizations participating in AzMAP include the Arizona Commerce Authority, Maricopa Community Colleges, the Arizona chapter of NTMA and a local precision machining firm.
Another important component of addressing the skills gap facing the manufacturing (and other) industries is ensuring that a state’s investments in education are aligned with the needs of employers looking to fill jobs, especially at the regional level. Most of the net new jobs in the U.S. are being created by small to midsized business. Many of these firms prefer to recruit their employees from within their own region, often because of their ties to the community or because a multistate recruiting effort would be prohibitively costly. Community college systems have an important role to play in this effort based on their regional delivery model. The importance of alignment between post-secondary curricula and regional workforce needs was discussed recently at the America’s Small Business Summit sponsored by the US Chamber of Commerce. The discussion included comments from governors sharing experiences from their states.
In 2012, the North Carolina Community College System (NCCCS) announced its Project Green Super Curriculum Improvement Project. This ambitious program would streamline NCCCS’s offerings by consolidating 80 curricula down to 32. This program, which included support and input from the National Association of Manufacturing, is designed to improve the ability of NCCCS’s course offerings to meet the needs of industries important to the state’s continued growth. One unique notion discussed in conjunction with the development of this program is the idea that employers having positive experiences with graduates from NCCCS would more likely send their employees back to the institution for further training, creating revenue opportunities for the school and further promoting a mutually beneficial relationship between industry and academia.
In Utah, certificate programs play an important role in the state’s 66 by 2020 plan, which aims to have 66 percent of the state’s population ages 25-64 possess either a board-approved post-secondary certificate or a college degree. The plan calls for the percentage of workers holding a certificate to increase from 4.3 percent to 13.0 percent. Certifications play an important role in addressing skills gaps and worker shortages in the manufacturing sector, as they often provide a pathway to well-paying manufacturing jobs for individuals who chose not to pursue a college degree.
In 2013, the State of Indiana established the Indiana Works Councils, a regional approach to addressing skills gaps and worker shortages by employers and educators who will evaluate career, technical and vocational educational opportunities for high school students within each of 13 regions. Recognizing the importance of manufacturing in regions throughout the state, the board of the Indiana Works Council regions has significant representation from the advanced manufacturing sector. Indiana has also implemented a matching grant program designed to support career and technical education curriculum development at the local and regional levels. Consistent with the national findings that such initiatives require collaboration across public, private and academic sectors, the grant program requires that grant funds be matched by significant private contributions. Advanced manufacturing career pathways were featured significantly in the first round of grant awardees.
The U.S. manufacturing sector has faced significant challenges over the past several decades, challenges that were significantly amplified during the Great Recession. However, the advanced manufacturing sector is, and will continue to be, a vital part of the U.S. economy. The recent signs of a rebound are certainly very promising and have important implications both for manufacturing firms and site selection professionals who represent them.
Several advanced manufacturing firms contemplating significant expansions to their U.S. operations are not only considering factors such as tax climate, regulatory environment and economic development incentive support, but have highly prioritized workforce development and human capital considerations as part of their evaluative process. These firms are seeking increasingly detailed information on factors such as regional labor cost and availability, educational attainment and other qualitative factors related to labor supply. In addition to data about the current workforce development/human capital situation, companies are also interested in learning about what resources are available to ensure they will be able to continue to recruit qualified workers over the long term. It is in this latter area where an understanding of workforce development solutions through the public, private and academic sectors can be extremely valuable. While this increased prioritization of workforce development issues is especially pronounced for manufacturing firms, this trend is seen in firms from other industries as well. The ability to provide accurate, detailed information on human capital subject matter areas at the state and regional level is likely to become an increasingly important part of the work of site selectors as companies increasingly prioritize these areas.
While there is a general consensus that a skills gap exists to some degree in the manufacturing industry, there are several strategies the public sector, academia and private industry can consider to address the challenge of ensuring there is a supply of qualified labor to support the growth of the U.S. manufacturing sector. Examples of these solutions include active promotion of apprenticeship programs, curriculum reform in the regional community college system and support for career and technical education pathways at the secondary school level. While the ideal solution for a particular region will likely involve a combination of several approaches, any successful strategy will require participation among the private, public and academic sectors.