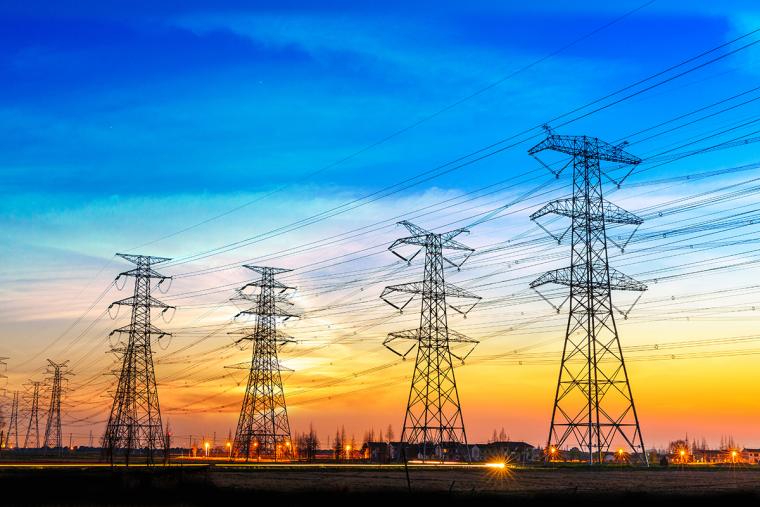
As a company makes a commitment to expand its operations, considerations such as logistics, labor availability and potential incentives and assistance programs to offset tax liability and startup costs often come to the forefront of the site search. These are important considerations while conducting the search; however, companies often overlook utilities as another significant search factor.
The prevailing thought is that utilities are always available – costs may vary, but electric power, natural gas, water and waste water needs can always be secured for their industrial expansion. This may be true, but at nearly one-third of total annual operating costs, utilities require more attention.
In conducting a detailed community cost analysis, overall utility costs are typically the third most important general operating cost category for most manufacturing operations. Labor and employee benefits comprise the largest operating cost, followed by transportation and logistics, then utilities. However, for many manufacturers, including chemical, pharmaceutical and food processors, the importance of utility availability and cost often emerges as the second most important annual operating cost – surpassed only by labor.
The graphic below illustrates how important overall utility costs can be as an operating cost percentage when compared to other major annual costs.
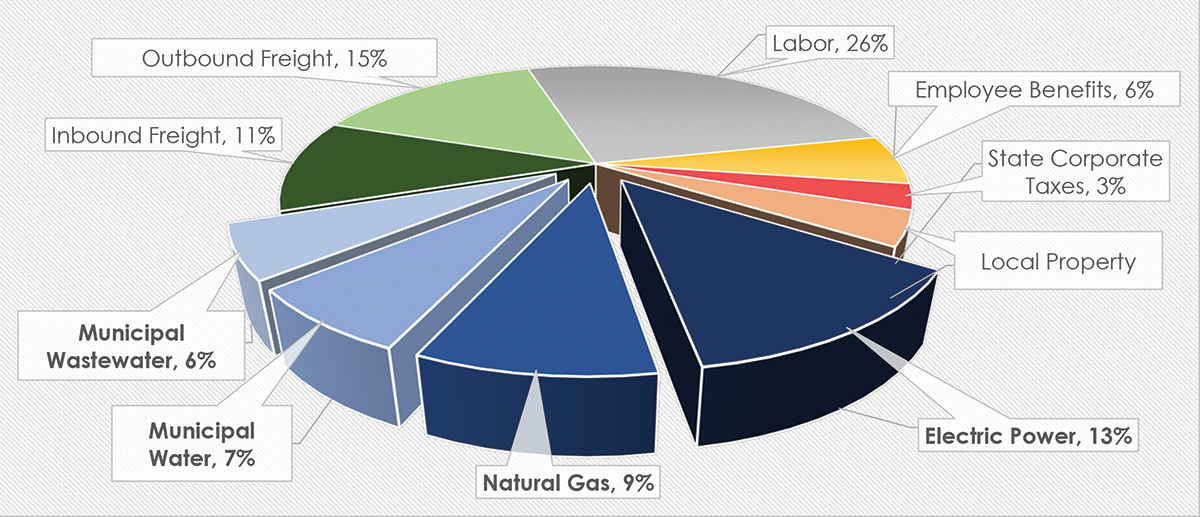
1. Initiate detailed research to understand preliminary utility needs for the startup operation and forecast potential future needs in five years or longer, based on potential expansion plans.
2. During a comprehensive screening process, match those needs with the community that appears to best satisfy those requirements.
3. Conduct field investigations to secure a community that provides those needs at a reasonable cost and reduced risk.
4. Identify major take-aways in determining a “utility-friendly” community.
Conduct the Research, Determine the Need
Based on the determination that plant expansion is necessary, the company must secure a clear understanding of its utility needs. In many instances, a company can rely on securing utility consumption levels from existing operations and model those numbers up or down based on estimated plant size or production output for the new operation. If the proposed operation is new to the organization based on a different product line or process technology, the company may need to obtain the advice of a design and engineering firm with a background or understanding of the company’s process and production machinery to secure good estimates of utility usage.
To forecast utility needs, the company must first be comfortable with estimating consumption levels, volumes and usage for electric power, natural gas, water and waste water for the proposed operation. In addition, the hours of operation per day, shift duration, number of days, employee estimates per shift, proposed product output and process machinery used are all key measures to give the company the input information necessary to forecast or estimate utility consumption levels.
Following are critical points that must be addressed early in the analysis.
Electric Power
• Determine the maximum rate of electricity usage over a 30-minute interval, denoted as kW demand
• Estimate the monthly consumption levels, expressed as kWh per month
• Establish required voltage to operate machinery
• Identify machinery susceptible to power interruptions.
Based on the volume of electric power required, primary transmission service may be a viable option over distribution (also referred to as secondary) service. Primary transmission service is typically a viable option once the kW demand exceeds 5,000 kW, but is also determined by the individual electric power provider.
Natural Gas
• Estimate the monthly volume required for processing and space heating, expressed in therms or MCF (thousand cubic feet)
• Determine the line pressure necessary for the operation
• Decide whether a firm (non-interruptible) supply of gas is required for the operation.
Water
• Forecast the initial daily requirement, expressed in gallons per day or month
• Identify peak demand, expressed in gallons per minute, usually over a 60-minute interval
• Establish special water requirements and chemicals or mineral composition to avoid that may negatively impact production
• Determine preferred flow rate.
Waste Water
• Forecast the initial daily discharge, expressed in gallons per day or month
• Identify discharge characteristics, including effluents such as organic materials (BOD, COD) and suspended solids (TSS), usually recorded in milligrams per liter (mg/l)
• Based on potential discharge levels, determine whether an onsite pre-treatment system should be considered if required by the community.
Communications
• Verify necessary communication requirements, including the need for fiber optics at the site
• Establish preferred communications carrier.
It is critical to not only determine the initial needs, but also what utility consumption levels could be within the next three to five years, or even longer. This is important information to use throughout the analysis.
Secure the Best Community Match During In-House Screening Analysis
Once the initial and ultimate utility needs have been verified, the process can move forward. During the screening process, the company now focuses on an in-house evaluation within the desired geographic search area to match utility and other project requirements to potential sites and communities that may work for the operation.
To initiate the screening process, the company should complete a document discussing key location considerations of the project, referred to as an RFI (Request for Information). The RFI is usually submitted to state, regional and local Economic Development Officials (EDOs) within the targeted search area where the new operation may locate.
This document includes pertinent utility information, including volume and consumption considerations established previously. The primary goal is to receive the best properties that could work for the proposed operation. Another purpose of the RFI is to request estimated utility cost information from each provider based on consumption information. In addition to estimated utility bills, other pertinent information to request includes natural gas, water and waste water line sizes and their location in relation to the subject property.
The next step is to rate and rank each received site on how well it will best satisfy the utility requirements for the proposed operation. Once this has been achieved, perform field investigations of the sites and communities to see how well they address project requirements for the operation. Depending on the project and geography involved, it is recommended to complete field investigations for no fewer than five locations in at least two states.
Conduct Field Work to Discover the Best Options
A detailed field investigation is the best way to inspect each finalist community and property to determine if the location will work for the new operation. For utilities, there are many considerations to assess during this step of the analysis. The following utility information should be reviewed and documented for every site investigated:
Electric Power
• Evaluation of existing transmission and distribution infrastructure
• Distance to substation(s)
• System capacity
• Condition of infrastructure
• Feasibility of dual feed service
• Service redundancy
• Cost of infrastructure improvements
• Surrounding power users
• Service history (outages)
• Incentives (rates, infrastructure)
• Quality rating of service provider
• Power generation sources
• Detailed costs, including any one-time costs.
Natural Gas
• Service availability, line size
• Evaluation of existing transmission and distribution infrastructure
• Line pressure
• Feasibility and evaluation of dual feed service
• Cost of infrastructure improvements
• Planned improvements
• Detailed costs, connection fee, surcharges.
Water and Waste Water
• Service availability, line size
• Treatment facility capacity and condition, distance from site
• Treatment technologies
• Water source(s)
• Water quality, including chemical composition
• Special permitting procedures
• Reliability of water supply, back-up plan
• Water pressure
• Lift stations versus gravity service for waste water
• Effluent treatment capacity and surcharges
• Planned improvements to the system
• Planned changes to the current rate structure
• Recent water and waste water service interruptions
• Water and waste water moratoriums affecting business development
• Need for on-site pretreatment (waste water)
• Detailed costs, connection fees, surcharges.
Communications
• Services available
• Fiber optics capabilities at site.
Once the sites have been inspected, schedule in-person meetings with representatives from each utility provider to discuss the sites and review any questions or concerns encountered during site inspections. During each meeting, have each utility provider illustrate on a map the location and line size of the water, waste water and natural gas serving the candidate site.
For electric power, secure a copy of the provider’s power grid map. This map gives an overview of the power network and available voltage emanating from the provider’s substations and transmissions lines. All mapping information discussed during the meeting should be sent to your attention electronically.
These meetings also provide the best time to review the estimated annual and one-time costs for each investigated site with the utility representative(s). In addition, request a detailed copy of all estimated annual and one-time cost information in writing on each provider’s letterhead, if not provided earlier.
Upon returning from field investigations, complete and review detailed cost comparisons for each finalist site. For utilities, compare all annual and one-time costs. Rank and recommend the top two or three locations that are the best fit for the new operation. Remember, all properties and communities will not be a perfect match; there will be deficiencies and risk to overcome, even with the recommended locations. The key is to secure the best community where deficiencies are manageable and can be overcome at the state and local level with quick action.
The next step is to discuss site deficiencies with state, local and utility economic development organizations and identify the best way these groups can assist in overcoming these gaps. This step is often conducted during final site due diligence assessment and incentive negotiations.
Major Take-Aways in Determining a “Utility-Friendly” Community
There are several ways a company can determine how “utility-friendly” a community or service provider is throughout the site search. This becomes evident early in the screening process, as the search progresses into field investigation, and finally during due diligence and incentive negotiations. As suggested earlier, the best time to correct any utility flaws or deficiencies is to negotiate directly with state and local EDOs and utility providers. All utility concerns must be addressed before a purchase agreement is finalized.
In securing the best site and community, you have likely reviewed countless proposals from locations across the designated search area eager to win the project. During this process, certain positive community attributes will emerge, giving these locations an advantage in their ability to supply the necessary utilities for current and future needs.
A “utility-friendly” community has the following positive attributes:
1. Ample reserve capacity of municipal water and waste water targeted for future community growth. It is recommended that a community should have an excess reserve capacity of at least 30 percent within its existing water and waste water system at any time.
2. Planned industrial parks containing a looped water and waste water system throughout the subject property for consistent and strong utility flows.
3. Constructed industrial parks with a centralized storm water system in place to serve both current and future industrial development.
4. Good relationships with local private electric power and natural gas providers, and aggressively monitors and requests the necessary expansions by these utility providers for future industrial development.
5. No water or waste water connection, impact or tap fees for new industrial development.
6. Reasonable or no effluent surcharges for those industrial users with higher than average effluent discharge levels.
7. Electric power providers with a plan in place to add future or upgrade current substation(s) as industrial districts expand.
8. Municipal service providers with a plan in place to expand their water and waste systems to serve the future industrial sector. This includes proper planning, such as securing right-of-way for line expansion and initiating pre-engineering studies to extend services once a prospect commits to a site.
9. Local utility providers that have exhibited little or no rate increases over the past five-year period and have no rate increase planned for the immediate future.
10. Communication providers that can provide advanced technical services, including fiber optics capabilities.
Communities that exhibit some or most of these utility-friendly traits are out there. It is up to a company to conduct a thorough vetting process based on these outlined steps to uncover the best location for their future manufacturing operation. T&ID