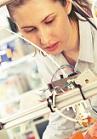
3D printing enables a more diffuse manufacturing footprint, allowing for production to take place in locations that may not have been able to support “traditional” large-scale manufacturing plants. But while everyone can compete, areas with the supporting talent pool, ecosystem and enabling business environment will be most successful.
Advancing Today’s Manufacturing
Technology in recent years has continued to follow Moore’s law – exponential growth in computing power coupled with a dazzling array of new applications. Some of the most exciting applications, known as “exponentials,” that have relevance to manufacturing include artificial intelligence, robotics, 3D printing/additive manufacturing and cloud-enabled crowdsourcing, among others. All of these technologies will inevitably have an impact on manufacturing and location strategy, however, 3D printing is already exerting a significant influence.
While the invention of the first 3D printer can be traced back to Chuck Hull in 1983[1], new applications for 3D printing are changing the way products are prototyped and produced in industries as diverse as automotive, aerospace, medical devices and consumer products. For the past few years, it’s been hard to pick up a manufacturing trade journal and not see an article on the transformative power of 3D printing.
Industry growth projections for 3D printing vary, but there is widespread agreement that the market will continue to expand through at least 2020, and likely well beyond. With an estimated market size of $5 billion in 2015, some high-end projections suggest up to 34 percent compound annual growth rates through 2020, indicating the market may explode to more than $20 billion within the next five years[2]. In another indication of the rapid technology adoption, a recent Gartner report indicates that by 2018, nearly 50 percent of discrete manufacturers expect they will be using 3D printers to make parts for products they sell or service[3].
Most experts align on the transformative nature and rapid growth potential of 3D printing. But how will this evolving technology impact manufacturing location and footprint decisions? The answer can be viewed through several lenses. As a starting point, the primary manufacturers of 3D printers are dispersed throughout the United States, with production locations including Eden Prairie, Minnesota, (Stratasys), Brooklyn, New York, (MakerBot, which was acquired by Stratasys in 2013) and Rock Hill, South Carolina, (3D Systems). Similarly, the 3D print “service bureaus” – third-party providers that print 3D objects on behalf of consumers or enterprise user — have sprung up across the country. For example, Stratasys Direct Manufacturing, the 3D printing services arm of Stratasys, lists production facilities in five U.S. states (California, Arizona, Texas, Michigan and Minnesota) as well as Canada and Brazil. For this article, however, we will focus primarily on location drivers and implications for the growing base of “traditional” manufacturers that are increasingly incorporating 3D printing into their production processes.
Technologic Advancement is Still about People
As with many evolving technologies, a skilled labor pool will be paramount to attracting and retaining operations that involve 3D printing. According to a 2015 article by the Institute of Electronics and Electrical Engineers (IEEE), 35 percent of engineering job postings now require 3D printing skills.[4] Talent development for this industry comes from many different sources, including traditional educational institutions, industry trade associations and the 3D printer manufacturers themselves. A prerequisite in most cases for fostering a deep talent pool is having a vibrant STEM-related ecosystem in place that builds basic skills in science and technology, on which 3D printing operations can draw. Well-known technology clusters and large university towns like the Research Triangle Area in North Carolina, Boston and Ann Arbor have an edge in this regard due to their already-extensive offerings of STEM programs at multiple educational institutions in those metro areas[5].
However, simply having generalized STEM programs is not enough. One of the most powerful accelerants for developing the workforce needed for 3D printing is through institutional partnerships, largely between universities and 3D printer manufacturers. Notable examples of such partnerships include those forged by the University of Virginia, the Rochester Institute of Technology (New York) and the University of Maryland with Stratasys. These collaborations are wide-ranging, from universities simply buying 3D printers for ancillary use in existing courses, to designing tailored curricula related to 3D printing technology with dedicated space for rapid prototyping labs and “maker space” with dozens of printers and related equipment. For example, the partnership between the University of Maryland and Stratasys resulted in a dedicated MakerBot Innovation Center within the university’s engineering school that is open to all university students, with dozens of 3D printers, associated software and direct integration into the required introductory course for all engineering students.[6]
Developing parts and components using 3D printing has been a major focus for aerospace companies for years, and regions with significant aerospace manufacturing clusters are likely to have skilled talent with 3D printing experience or with readily transferrable skillsets. For example, GE is working to integrate a large 3D printing operation into its facility in Auburn, Alabama, to produce fuel nozzles for its aircraft engines business.[7] Industry trade associations like the Society of Manufacturing Engineers (SME) also have developed forums and courses for their members to educate them on 3D printing technologies through local chapters.
3D Printing doesn’t Flourish in a Vacuum
Talent is critical, but it’s not the only driver for manufacturers to deploy 3D-printing-focused operations. As with any emerging technology, a supporting “ecosystem” is important to cultivate adoption and growth. Key players in developing a local or regional 3D printing ecosystem can include training providers (universities, technical colleges, etc.), software developers, materials suppliers (ceramics, plastics, metals, etc.), financers and 3D printing service providers, among others. When Shapeways, the leading 3D printing marketplace, relocated operations from the Netherlands to the United States, it selected New York City. The location may be a surprise based on “traditional” manufacturing deployment drivers, but Shapeways’ decision may have been influenced by proximity to MakerBot in Brooklyn and by the region’s access to abundant venture capital funding[8].
A strong enabling business environment is also important. Locations that incent the use of emergent technologies and heavy capital investment (3D printers can range in price from under $1,000 for basic models to more than $10,000 for commercial-grade printers) may have an advantage over those that heavily incent job creation instead.
Foreign Direct Investment for 3D Printing has Already Begun
The recent case of a foreign-based manufacturer seeking to enter the U.S. market sheds light on the location decision process for companies focused on 3D printing. In this case, the company, which produces advanced materials components for aerospace and other industries, considered a wide range of location drivers including quality and experience of the existing workforce, available workforce development programs, relevant industry concentration, development-ready real estate options and attractive economic development incentives. Of the many location factors, however, the company placed the highest priority on workforce and was specifically seeking professionals with Computer Numerically Controlled (CNC) machinery skills and associated engineering abilities. In addition to incumbent skills, the company sought a location with a system of local technical colleges and universities to provide training, education and workforce development programs that would create a pipeline of talented workers who could be hired as interns and future full-time employees.
Through initial desktop analysis, followed by field investigations of the “short list” candidate locations, the company was able to identify areas that had the ecosystems in place to appropriately support the proposed investment and had a history of success with similar companies. Many locations are trying to develop the educational infrastructure and partnerships needed to develop talent for advanced manufacturing in general and 3D printing specifically. For example, the region around Hartford, Connecticut, demonstrated its long history of training workers through its technical college system, placing them with partner companies and continually improving their programs with input from these local corporate partners. Dallas and Hartford stood out for their concentrations of similar advanced manufacturing companies specifically related to the aerospace industry. And regions such as the Richmond, Virginia, area are developing an advanced manufacturing and R&D center to help entice companies seeking to make significant investments in 3D printing and other related technologies.
Throughout the location decision process, these areas stood out among the many communities vying for the project and their emphasis on developing a workforce focused on advanced manufacturing has placed them a step ahead in the race for this particular investment and perhaps other similar projects in the future.
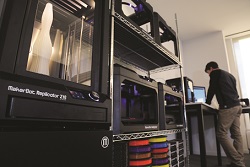
Among location drivers for 3D printing operations, the availability of talent and the supporting ecosystem often take top priority. But as the technology permeates, some factors that drive “traditional” manufacturing location decisions may be de-emphasized for companies deploying operations that rely heavily on 3D printing. Given the focus on availability of highly skilled talent for 3D printing, labor costs in this industry appear to be less important of a location driver. As 3D printing skillsets become more mainstream over time, however, this dynamic may change. In addition to labor costs, logistics may also be less of a consideration for 3D-printing-focused operations, as finished goods warehouses decrease in size and more products are made to order. Manufacturing footprints are also likely to become more distributed, as smaller production batches become more commonplace, and companies can avoid the high setup costs of creating molds or tooling in a large, centralized plant. This “footprint dispersion” may open up 3D printing opportunities for locations – urban or rural – that have historically been less capable of supporting large-scale manufacturing plants based on “traditional” location factors. While more locations may be able to compete, however, those that demonstrate the most favorable talent pools, ecosystems and supporting business environments will be the big winners in the race to attract 3D-printing-focused manufacturing to their regions.
[1] The Night I Invented 3D Printing; cnn.com; http://www.cnn.com/2014/02/13/tech/innovation/the-night-i-invented-3d-printing-chuck-hall/
[2] 2015 Roundup Of 3D Printing Market Forecasts And Estimates; forbes.com; http://www.forbes.com/sites/louiscolumbus/2015/03/31/2015-roundup-of-3d-printing-market-forecasts-and-estimates/
[3] Market Guide for 3D Printing; Gartner; December 2014
[4] Thirty-Five Percent of Engineering Jobs Now Require 3-D Printing Skills; ieee.org; http://theinstitute.ieee.org/career-and-education/career-guidance/thirtyfive-percent-of-engineering-jobs-now-require-3d-printing-skills
[5] Brookings Institute, Patent and STEM Data; http://www.brookings.edu/research/interactives/2013/metropatenting
[6] University of Maryland Opens MakerBot Innovation Center. http://investors.stratasys.com/releasedetail.cfm?ReleaseID=908293
[7] GE Aviation plans $50 Million 3-D printing facility in Auburn to make jet engine parts http://www.al.com/business/index.ssf/2014/07/ge_aviation_plans_50_million_a.html
[8] Where Will the 3D Printing Industry Cluster?; Robotics Tomorrow; http://www.roboticstomorrow.com/article/2014/07/where-will-the-3d-printing-industry-cluster/4292