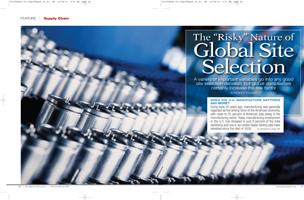
Does the U.S. manufacture anything any more?
Going back 50 years ago, manufacturing was generally regarded as the driving force of the American economy, with close to 25 percent of American jobs being in the manufacturing sector.
Today, manufacturing employment in the U.S. has dropped to just 8 percent of the total workforce and one in six United States factory jobs have vanished since the start of 2000.
Given numbers like this and the downward trends related to manufacturing jobs in this country, it is not surprising that there is a general perception that “America doesn’t make anything anymore.”
But while the numbers don’t lie, it is insufficient to judge the strength of the manufacturing industry here solely by job count. In fact, due to a variety of changing dynamics worldwide, manufacturing in the U.S. appears ready for a renaissance.
Productivity in the U.S. – up 70 percent since 1977 – is at an all-time peak. According to the Federal Reserve Bank of Chicago, just 184 workers can do now what it took 1,000 workers to do in 1960. As a result, Americans produce 21 percent of all goods globally, more than the Japanese, Germans, British and Italians combined, a fact that might surprise many.
American laborers are also well-educated and highly motivated compared to those in developing countries. As more sophisticated products like aircraft/aerospace vehicles and components, pharmaceuticals and semiconductors continue to account for the biggest – and highest-paying – chunk of global manufacturing jobs, the U.S. is well-positioned to reap the benefits. “Made in America,” it turns out, also makes good business sense.
It now appears that the advent and intensification of globalization, which gave rise to the manufacturing sector in developing countries like China, India, Mexico, Brazil and Vietnam, is now turning out to be a double-edged sword of sorts. Manufacturers that got caught in the “offshoring” craze of the ‘80s, ‘90s and 2000s are now considering moving those operations back to the U.S.
The price of doing business, of course, is the key factor at play. The consulting firm AlixPartners reported that, in 2005, Chinese-produced parts arrived at U.S. destination ports an average of 22 percent cheaper than comparable products domestically. By the end of 2008, the average price gap had dropped to 5.5 percent.
The rising cost of Chinese labor is partly to blame, with average manufacturing wages in China rising nearly 70 percent between 2002 and 2006. An equally important factor, however, is transportation. The higher the cost of transportation, the more significant the freight “penalty” becomes to ship over greater distances. Freight costs are increasingly offsetting, even eclipsing, any savings from cheaper labor.
Oil prices are a key driver here. Offshoring manufacturing, which might have seemed attractive when oil was $70 a barrel, might be dramatically different if the price rises—as it has in the recent past—to $140 a barrel.
In fact, in a recent survey by the global consulting giant Accenture, 61 percent of manufacturing executives said they were considering relocating factories back to the U.S. or Mexico from lower wage rate Asian countries due to rising logistics and transportation costs.
Risk management – a new priority for supply chain practitioners
When it comes to global supply chain considerations, the one decision factor which has taken on increasing scrutiny and importance is that of risk management. The complexities associated with global freight moves and the risks associated with doing business thousands of miles from home, are causing companies to re-evaluate their supply chain manufacturing and sourcing strategies.
Many of the same executives surveyed by Accenture also raised concerns over a variety of “risk management” related issues including inconsistent application of intellectual property laws, human rights issues, product quality control deficiencies and the lack of environmental regulation in developing countries --- particularly China.
Meanwhile, threats like Somali pirates, Mexican drug lords and the fallout from natural disasters like the Japanese earthquake and tsunami have left more and more companies thinking twice about the supposed advantages of producing products half-way around the world.
The concept of “outsourcing” has evolved to a trend termed “near shoring” or bringing the source of supply closer to the markets in which you serve. Our point of view is that this will ultimately trend to “right shoring” or a regionalized manufacturing/sourcing strategy.
Think of “right shoring” like you would your own personal financial investment portfolio. From a risk management perspective, it is far wiser to diversify your savings across a range of investments as opposed to putting all your eggs in one basket. For the same reasons, from a supply chain perspective, no one should put all of their manufacturing or sourcing investments in one country or area of the world. From a supply chain risk management perspective, it makes sense to diversify as well.
Port diversification strategies, as Wal-Mart has employed now for years, are prudent. Importing all of your goods through one port, LA/Long Beach for example, would be a business killer should something happen to shut down that port, be it a natural disaster or otherwise. This is just another example of supply chain risk management in practice.
We truly operate in a global world today. The benefits to operate on a global scale are significant, but so are the added risks and complexities. Supply chain practitioners were once focused solely on creating more efficient and effective supply chains, although this has not changed, risk management considerations have taken on increased importance in the development of those strategies.