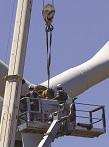
For many, the term manufacturing still conjures up images of rusty smokestacks, dirty production floors and sweaty workers. However, like with most everything in the world, technology has changed how things are made, leading to a new name for the industry: advanced manufacturing.
The definition of advanced manufacturing varies, but in general, the industry includes companies that use process technologies and automation to produce products, including products that are innovative or technologically complex.
Today, the majority of new manufacturing investment in the U.S. can be considered “advanced” – as most rely on technology and automation to compete in a global economy where consumers demand better products faster.
As a result, site selection factors for advanced manufacturing operations are primarily focused on finding skilled workers capable of operating new equipment and finding communities that support “speed to market” through sites, infrastructure and business climate.
Manufacturing: Linchpin for U.S. Economic Growth
Despite a “new age” economy seemingly focused on technology and services, manufacturing remains more important than ever to the U.S. economy. According to National Association of Manufacturers1 (NAM), there are 12.3 million manufacturing jobs in the U.S., accounting for nine percent of the total workforce. Including an additional 18.5 million jobs that exist to support manufacturing operations, one in six private sector jobs are related to manufacturing.
The industry is not only vital to U.S. jobs and productivity, but also to addressing the long-term needs of the country related to infrastructure, energy and sustainability. Manufacturers produce materials needed to repair and expand roads and other infrastructure, machinery and equipment to power the world and renewable energy components like solar panels and wind turbines.
A vibrant manufacturing sector is also a catalyst for innovation and technology growth, creating new products designed to improve quality of life. As of 2012, the manufacturing industry is responsible for 68.9 percent of all R&D spending2 in the U.S., thus further justifying the term advanced manufacturing.
Reshoring and Foreign Direct Investment Trends
Global economics are contributing to the growth of the advanced manufacturing industry in the U.S. Rising wages in China, increased transportation costs and competitive energy prices in the U.S. have reduced the cost-benefit – and the appeal – of producing some goods in Asia. In addition, the threats of shipping delays and risks associated with intellectual property theft have directed advanced manufacturing investment to the U.S., a trend known as reshoring or nearshoring.
A 2011 study3 by Boston Consulting Group identified the industry sectors primed for a reshoring shift based on the economics cited previously; they generally fall into these categories:
1) Goods expensive to ship - such as automotive, transportation equipment, machinery, appliances and furniture
2) Technologically advanced products in which intellectual property is a concern, such as computers and electronics
3) Companies that have, or can develop, automated production processes – such as fabricated metal products, plastics and rubber, among others.
Companies in all of these categories utilize advanced manufacturing in some, if not most, of their production processes.
The same economics apply to foreign direct investment (FDI): companies based outside the U.S. that invest in new production operations in the U.S. Many of these organizations had been importing their products as suppliers to U.S. original equipment manufacturers (OEMs), but the economics now justify locating production facilities closer to major customers.
The same trend holds for companies including Swiss industrial robotics supplier ABB Ltd., which designs and produces automated equipment and machinery for manufacturing plants in the U.S. In 2015, ABB announced a major investment in the Detroit region based on its proximity to the U.S. automotive industry.
The Threat of the Skills Gap
Reshoring and FDI trends are largely made possible due to advances in technology and production processes that have become more automated (i.e., advanced), thus requiring fewer workers. While automated processes are replacing many manual, low-paying jobs, they are simultaneously creating a need for skilled employees to operate, maintain and retool equipment — jobs that are typically associated with higher wages, such as machinists and programmable logic controller (PLC) technicians.
This is where the skills gap comes into play. Simply stated, companies are struggling to find enough qualified workers. A recent study by NAM’s Manufacturing Institute and Deloitte found that manufacturers will need to fill 3.5 million production jobs over the next decade. Two million of those jobs will likely go unfilled based on the changing needs for skills, retiring Baby Boomers and a shortage of young workers entering the field.
The U.S. skills gap is particularly threatening to small and medium-size operations, where production efficiency is critical. Chandler Systems Inc., a 35-person manufacturer of innovative water treatment products in Ashland, Ohio, that also works with a manufacturing supplier in China, is testament to this. “We would love to bring more jobs back to the U.S., but are concerned about the availability of individuals willing and able to perform the work we need,” said Bill Chandler, III, marketing director, who also handles some of the company’s hiring. Chandler Systems typically pays its entry-level workers $12-$14 per hour, well above the state minimum wage of $8.10.
Notably, many of these skilled jobs do not require a four-year college degree. A 2014 study4 by the Brookings Institute found that only half of all U.S. STEM jobs – those that require some knowledge of science, technology, engineering or math – demand a Bachelor’s degree or higher. An Associate’s degree in a specialized field such as computer aided design (CAD), a certification in a trade such as welding or maintenance, or sometimes just a high school diploma and an ability to learn on the job, can be ample preparation for these skilled positions. “One of the toughest skills to find are workers who are willing to learn and comprehend new things,” said Chandler.
Customized Workforce Training
Customized workforce training has become an attractive way for states and communities to narrow the skills gap and lessen the burden of employee training costs for employers. Three states in the Southeast U.S. offer best-in-class workforce training programs. Georgia’s Quick Start5, Louisiana’s FastStart6 and South Carolina’s readySC7 take a similar approach to customized training programs for employers. Each program bases its training curriculum on the specific skills and technical expertise required by employers in the state. Instructors often visit company facilities, including those overseas, to familiarize themselves with processes, while the companies may contribute equipment for classroom instruction. The training often takes place at a local community or technical college, onsite at the employer or in mobile training lab stations. Each program is centered on the idea of flexibility – whatever it takes to best meet the training needs of any company.
Several states have developed specialized workforce training facilities that instruct trainees on skills most desired by the advanced manufacturing industry. Students at the Alabama Robotics Technology Park8 receive training in automation and safety processes while practicing on $40 million automation and robotic technology equipment. Employers gain the benefit of no-cost training for employees and avoid sending workers to out-of-state facilities.
Shovel Ready Sites
Speed to market is key for advanced manufacturers, including the time required to get a new production plant up and running. Project timelines that were once over two years have shrunk to 12-18 months from concept to completion – sometimes even shorter. A recent BLS & Co. client wishing to relocate from an outdated facility into a more efficient and automated one had a project timeline of nine months and was fortunate to find an existing, quality building that could accommodate its operation.
As the inventory for existing buildings has dwindled, Greenfield sites that are shovel ready have become very attractive for advanced manufacturing projects. A shovel ready (or ready to go) site has invested in industrial-grade road and utility infrastructure to the site. Excess utility service capacity must also be available to support new users with reliable and affordable energy – especially as it relates to electricity to power all that automated equipment.
A shovel ready site owner has also invested in environmental, civil engineering and legal due diligence to identify site issues that must be mitigated. Preferably, an independent audit has also been conducted by a third party with engineering and site selection expertise to ensure a quality site for development.
States such as Tennessee, Ohio and South Carolina currently offer such programs to evaluate sites for shovel ready status. These programs allow a prospective purchaser to shave months from the construction timeline, and save on site development and infrastructure costs.
Speed to Market is Key
Implementing business-friendly policies and regulations that consider cost and speed to market concerns of advanced manufacturers are essential to supporting the growth of the industry.
According to NAM, a manufacturer’s compliance cost8 with government regulations is $20,000 annually per employee. That same cost rises to $35,000 each year per employee for small manufacturers. State and local governments that layer regulations that exceed federal standards increase these compliance costs and discourage new investment.
Regulatory reform, which lowers the costs of compliance for U.S. manufacturers while still achieving the intended regulatory outcome, would free up capital for manufactures to reinvest into new technologies, hire more workers and increase wages for employees. Reducing federal corporate tax burden would also improve the U.S. business climate and help level the playing field with foreign competitors.
At the state level, Indiana, Georgia and Colorado9 have worked to lower state income tax liability by adopting a single sales factor apportionment formula. The formula incentivizes companies to invest in future property and job growth, but doesn’t penalize them with increased taxes related to property and payroll value.
Flexible Incentives Support Capital Investments
With millions of dollars invested in equipment, advanced manufacturing projects tend to be more capital-intensive than job-intensive and, as a result, are not well-served by long-standing incentive programs that solely emphasize job creation.
Some states have begun to proactively address this disconnect via tax credit incentives equal to a percentage of qualified investment (including the value of leases). For example, North Dakota, which has seen a flurry of investment in oil and gas over the past few years, has developed an Automation Tax Credit10 that allows a company to claim a state income tax credit valued at 20 percent of the total purchase or lease cost of automated machinery and equipment. Indiana offers a similar tax credit called the Hoosier Business Investment (HBI) Tax Credit11equal to 10 percent of qualified capital investment.
Other capital investment incentives include free or discounted land and cash grants for site development and utility extensions. Personal property tax exemptions and abatements – as well as sales tax exemptions on manufacturing machinery and equipment, goods and utilities and construction materials – are extremely attractive to manufacturers focused on minimizing a project’s upfront costs.
Finally, flexible incentive regulations that allow companies to perform business actions such as signing a lease or hiring new employees without forfeiting potential incentives can be just as important as the financial incentives themselves.
Conclusion
Advanced manufacturing is the definition of modern-day manufacturing in the U.S. and is vital to the economy and growth of the country. Looking ahead, new technologies, such as 3D printing or additive manufacturing, will continue to impact and transform the industry. Understanding and reacting to the industry’s modern-day needs – especially related to skilled workforce and speed-to-market considerations - will support its growth for many decades to come.
Resources:
1 http://www.nam.org/Newsroom/Top-20-Facts-About-Manufacturing/
3 https://www.bcg.com/documents/file84471.pdf
4 https://www.brookings.edu/interactives/the-hidden-stem-economy-key-findings/
5 http://www.georgiaquickstart.org/industry.php?id=Advanced%20Mfg
6 http://www.opportunitylouisiana.com/faststart
8 http://www.nam.org/Issues/Regulatory-Reform/
9 http://www.taxadmin.org/assets/docs/Research/Rates/apport.pdf
11 http://iedc.in.gov/incentives/hoosier-business-investment-tax-credit/home