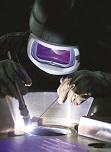
If metalworking is an art, a science or a combination of both, it is clear that the manipulation of metals for tools, weapons, utensils, structural elements and currency has held civilization’s interest for most of recorded history. It is suggested that copper jewelry may date as far back as over 8,000 B.C. No doubt, our fascination with precious metals such as gold and silver has shaped countless events throughout time.
Today, the metalworking industry is a complex array of interrelated activities that collectively cut, form or join metals to create large-scale structures, assemblies or individual parts. In the U.S., the Fabricated Metal Manufacturing sector, as defined by the North American Industrial Classification System (NAICS), had a year 2011 value of shipments of $323 billion or nearly six percent of all manufacturing output.
Since the industrial revolution, the working of metals has been a mainstay of American manufacturing and despite the plethora of new space-age materials, the process of metalworking does not appear it will lose steam any time soon. From the most intricate casting for medical devices to the massive steel plates for mega ships, the metalworking art is clearly a dominant component of the global manufacturing environment.
Defining the Metalworking Industry
Following the NAICS hierarchy for the Fabricated Metal Manufacturing sector (332), there are eight sub-sectors that comprise the industry:
-
Forging & Stamping (3321)
-
Cutlery & Handtool Manufacturing (3322)
-
Architectural and Structural Metals Manufacturing (3323)
-
Boiler, Tank & Shipping Container Manufacturing (3324)
-
Hardware Manufacturing (3325)
-
Spring and Wire Manufacturing (3326)
-
Machine Shops, Turned Product; Screw, Nut & Bolt Manufacturing (3327)
-
Other Fabricated Metal Product Manufacturing (3329).
In turn, each of these sub-sectors contains further classification in more industry detail, resulting in 36 detailed industry descriptions at the six-digit level of NAICS detail. As ancillary industries, Foundries (3315) and Machinery Manufacturing (333) are often included under the metalworking industry umbrella. And, in one of the industry’s most visible applications, Motor Vehicle Metal Stamping (336370), the body parts for the millions of automobiles on the road today effectively demonstrate the technical prowess of the metalworking industry. Although motor vehicle stamping is a metalworking activity, it is classified under NAICS as a sub-category of Motor Vehicle Parts Manufacturing (3363). Given the difficulty in estimating total employment in the metalworking industry by the inclusion or not of motor vehicles, aerospace, machine manufacturing and electrical/appliances, the focus of this article will be centered on Fabricated Metal Manufacturing (332).
According to Steve Kline of Gardner Business Media Inc., the metalworking industry has witnessed a mild contraction for most of 2013. This contraction is due to poor business conditions at facilities with fewer than 50 employees, but facilities of 50 or more employees have demonstrated growth in 2013. Mr. KIine points out that capacity at metalworking shops was at approximately 77 percent for year 2013 which is welcome news for the industry whose 2009 low of nearly 62 percent was its lowest in almost 50 years.
In 2012, the US Census Bureau’s County Business Patterns indicate that the nation’s 55,377 establishments in the Fabricated Metal Manufacturing sector (332) had an average employment of 25 persons. Productivity averages for the industry equate to $253,750 in annual shipments per employee, or about half of the productivity per employee figure for the total U.S. manufacturing sector.
As shown in the table, productivity in the metalworking subsectors of NAICS 332 ranged from a high of $419,625 for Boiler, Tank and Shipping Container Manufacturing (3324) to a low of $184,350 for Machine Shops (3327).
Fabricated Metal Manufacturing (332) is present in all 50 U.S. states and states with traditional manufacturing strength continue to exhibit industry leadership in this sector as well. The following 10 states collectively represent more than half of the nation’s output in shipment values:
Unexpectedly, the states exhibiting the highest employee productivity differ from the above list. The five leading states are, in order, Arkansas, West Virginia, Oklahoma, Ohio and South Carolina. Conversely, the states showing the lowest productivity output are Idaho, New Mexico, Delaware, Vermont and Oregon. Value added, or the true measure of employee output exclusive of the costs of raw materials, averaged at about 52 percent of total shipment value for all U.S. states.
Employment and Wages
As the 10 leading states have significant market share of the industry, their employment pattern follows a similar course. California, Texas and Ohio rank first, second and third respectively for jobs, which is a slight variance to their value of shipment ranks, but all 10 of the leading states from the table above are the predominant employment centers for fabricated metal manufacturing. Collectively, these 10 states account for nearly 60 percent of the 1.274 million positions within the industry.
Employment industrywide has indicated cyclical responses to economic conditions over the past five years, with a loss of 312,325 jobs between 2008 and 2010. The rebound by 2012 has meant 103,494 of those lost positions have been regained to a level of 1.38 million employed persons. Wages, on the other hand, have recovered faster, but are showing a softening as employment grows. The following chart helps to clarify these trends.
In 2012, hourly wages ranged from a low of $18.72 in Montana to a high of $30.53 in Alaska. The median wage value for the industry is $23.24 per hour. Unionization is prevalent in the industry, but wage patterns in right-to-work states do not differ that appreciably from unionized states. Of the 24 right-to-work states, hourly wages for Fabricated Metal Manufacturing (332) averaged $22.50 in 2012, as opposed to $24.53 per hour for labor-oriented states, indicating only a $2.03 per hour differential.
Operational Variations
Given that metalworking often involves a large amount of electric power for machinery operation, locations that can benefit from lower industrial power rates can provide enhanced operational savings. According to the US Energy Information Administration (USEIA), the seven lowest-cost states for industrial electricity in 2014 are as follows:
On the other hand, the seven most expensive states for industrial power are:
Transportation plays another key role in metal products, as proximity to raw materials as well as delivery to end users may impact bottom-line profitability. The Primary Metals Manufacturing (331) sector represents the source of raw materials for Fabricated Metal Manufacturing (332), and the six states that collectively produce more than 50 percent of all primary metals shipments are Indiana (12.6 percent), Ohio (11.2 percent), Pennsylvania (11.0 percent), Texas (6.5 percent), Kentucky (5.1 percent) and Illinois (5.1 percent). The location of production facilities that can effectively deliver to major population centers throughout the U.S. most are often affected by the transportation economy of access to raw material sources. Rail is especially important to the industry for the entire supply chain.
The Effects of Offshore Competition
While many industrialized nations have the capability to effectively compete with the U.S. for metal fabrication, China consistently emerges as the No. 1 location for offshore production. Chinese manufacturing has made continuous process improvements that offer significant cost solutions. Products manufactured in China offer a considerable advantage, including access to many types of the materials needed, the labor that is required and the ability to meet production levels.
Thee US Census Bureau reveals that between 2001 and 2011, the trade deficit with China eliminated or displaced more than 2.7 million U.S. jobs, over 2.1 million of which (76.9 percent) were in manufacturing. These lost manufacturing jobs account for more than half of all U.S. manufacturing jobs lost or displaced between 2001 and 2011.
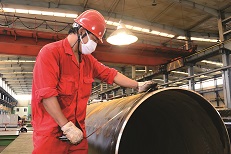
According to the Precision Metal Forming Association (PMA), tariff and non-tariff barriers target American manufacturers, making it more difficult for small businesses in particular to navigate the hurdles put in place by trading partners. This, combined with illegal subsidies and the rise of State Owned Enterprises (SOE), makes it difficult for Americans to globally compete. PMA estimates that a quarter of a million domestic jobs have been lost since 2000 due to the rise of Chinese counterfeit products practices.
Location Guidance for Metalworking Industries
Attempting to establish universal location guidelines for siting facilities in the Fabricated Metal Manufacturing (332) sector as a whole is impossible — it’s just too wide a net with too many variables to be considered. However, some basic essentials are necessary for any company in the metalworking arena and therefore their location consultants to consider when contemplating expansion or relocation strategies.
-
Benchmarking — evaluate production processes, IT operation, sales, HR, accounting and other business activities. Determine inefficiencies that exist within the organization and isolate those that may be relative to economic geography.
-
Technology — assess not only shop floor equipment that integrates design with tooling, but determine if useless or legacy paper trails within the supply chain exist that slow communication between firm, customers and vendors. Proximity to universities with centers of excellence in manufacturing technology will be helpful in crafting new strategies for improving enterprise-wide technology efforts.
-
Labor — skills shortages and an aging workforce are commonplace in the metalworking industry. Examine markets that have competent labor supply and be prepared for new learning, knowledge management and other challenges especially for newer-generation workers with different attitudes toward performance, compensation technology, etc.
-
Operational efficiencies — proximity to raw material sources, distance to end-point delivery, efficient transportation networks — these are necessary ingredients to any manufacturing operation. Especially in metalworking, attempting to select locations that can provide optimum operational effectiveness will reduce the impact of shrinking margins from rising offshore competition.
-
Business analytics — combine business performance analytics with external market data to determine growth or diminishment within the customer’s industry. Business analytics will predict future cost savings obtaining raw materials.
Looking Ahead
Quoting Baker Tilly, a leading accounting and advisory consultant, the metalworking industry is amid a structural change. Productivity and revenues are rising while the number of companies is in decline. New techniques are necessary to drive increased scale, productivity, market penetration and specialization. Flexibility to respond to regional and global opportunity represents the future for most metal fabricators.
Location recommendations must ultimately rely on the company’s ability to meet customer demands. That may mean relocation to a point closer to serve the existing base or seeking out untapped market potential that can provide technological efficiency and customer responsiveness. Increasingly, tomorrow’s site selectors will take on more of the role of management consultants to adequately provide in-depth market guidance to their clients striving to stay ahead of the competition in an industry undergoing fundamental change.