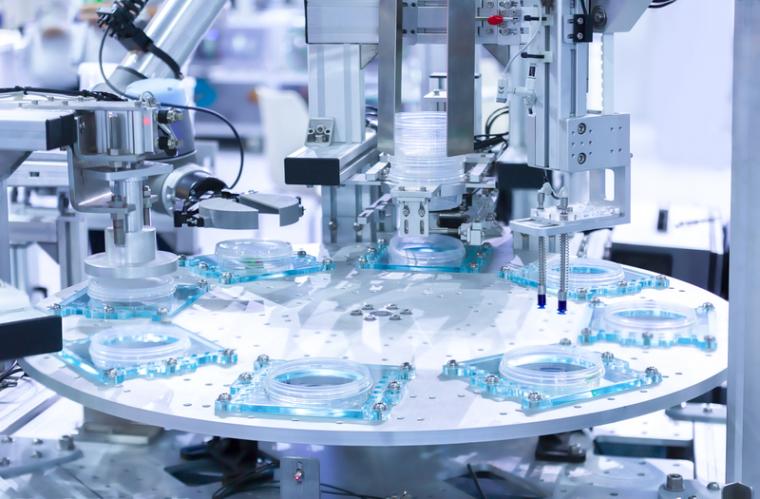
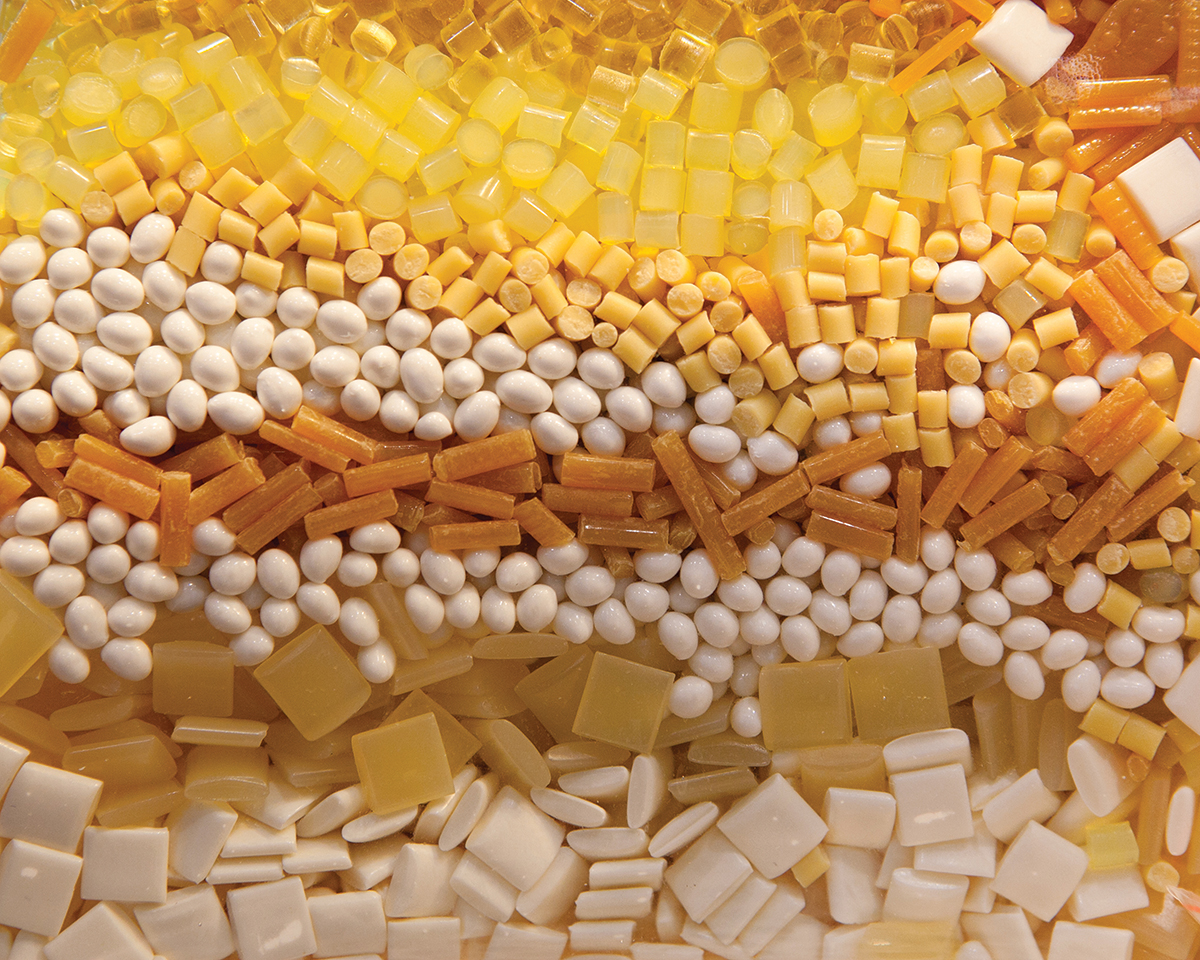
From manufacturing to processing, the American plastics industry has become a force from the national level down through local communities. A single plastics manufacturing plant can bring hundreds, if not thousands, of skilled, well-paid jobs to a community. In addition, plastics facilities bring a supply chain that has localized requirements, while also creating a vertical that reaches suppliers regionally and interstate.
Over the years, the leading location factors for the plastics industry have evolved, as has the rest of the economy. Varying dependent on the location, process and end product, the vital factors in finding the optimal site for a plastics facility include skill availability, market saturation, access to feedstock, energy costs and grid reliability, site readiness, infrastructure, consumer proximity, environmental regulations and economic development incentives, among others.
Now more than ever, industry leaders and company decision makers are deploying site selection strategies and forecasted data analytics to find that optimal site for their location decisions.
A Leading Contributor to the Economy
With a wide spectrum of processes and uses, America’s plastics industry is a leading contributor to the nation’s economy and a major employer across the country. How big is the impact of the robust industry on the American economy? According to a 2019 study by the Plastics Industry Association (PLASTICS), the industry advocacy organization, the plastics industry supports 993,000 jobs across the economy, which jumps up to over 1.7 million jobs when also accounting for suppliers. When it comes to annual dollar impact, the plastics industry reports more than $451 billion worth of shipments annually.
As the eighth largest industry in the U.S., the plastics sector is experiencing a 2 percent annual growth rate in overall value. Meanwhile, since 2012, shipments have increased by 1.2 percent annually, a true testament of the industry’s success after being challenged mightily in the last global financial crisis.
Overall, according to the PLASTICS study, employment growth for the industry has outpaced the larger manufacturing sector by a matter of 1.7 percent to 1 percent, respectively. Indiana is among the leading states with businesses in the dynamic plastics sector as 16 of every 1,000 workers are from the industry. More on the workforce element of the industry later.
Creating a Location Strategy Is Critical
No matter the scope and size of a project, there is a list of key factors that must be understood and assessed when making a critical location decision. When it comes to the plastics industry, developing a location strategy and conducting a site selection analysis is vital. Not only are the investments significant, the bespoke requirements for the industry must be thoroughly understood and thus evaluated empirically across the project.
As each project will have unique specifications and tailored metrics, the following are among the critical aspects to evaluate in a site selection process:
• Skills availability
• Talent pipeline
• Access to feedstock
• Energy costs and grid reliability
• Site readiness
• Infrastructure
• Consumer proximity
• Environmental regulations
• Economic development incentives
Skills Availability
The site selection industry has evolved immensely over recent decades, particularly when it comes to client metrics and priority weighting. No aspect has received more attention during that evolution than the workforce. In order to meet near- and long-term objectives, a business must ensure it will have the skills available to get the job done. The plastics industry requires a custom skillset distinct from many other sectors.
At a time when unemployment nationwide is 6.2 percent, and even lower in some regions, employers are struggling to find talent. Unfortunately, plastics industry leaders are finding themselves squarely in the crosshairs of these monumental challenges. As decision-makers begin to narrow their location options, conducting a labor analytics study is vital to understanding the true sustainability of skills within a market.
Successful operations within the industry require employees with training in skilled trades, experience in engineering and production occupations, and specific certifications. By undertaking labor analytics during the location strategy process, business leaders have the tools and data to understand the opportunity for finding and recruiting talent that will meet their workforce requirements in the near term, as well as into the future.
Understanding where the core plastics workforce is today across the U.S. presents as fascinating view of the dynamic industry. The Chicago area is the leading employment base for the plastics industry, with over 30,000 workers, followed by the Greater Los Angeles region, according to Bureau of Labor Statistics data. Following Chicago and Los Angeles, the largest industry employment bases are the New York City metroplex, Dallas-Fort Worth and Minneapolis-St Paul. Leading the way for the top five midsize markets are Grand Rapids (MI), Elkhart (IN), Rochester (NY), Akron (OH) and Greenville (SC).
When we look at the fastest growing workforces of the plastics industry, Elkhart (IN), Davenport (IA), Racine (WI) and Jefferson City (MO) are all seeing growth of more than 15 percent since 2015. Driven by several factors, these markets are all distinctively developing programs and initiatives to support the skills requirements of the industry.
Along with developing an understanding of the skills for each market, business leaders need to ascertain compensation costs for the required workforce. In fact, labor costs can equal more than 80 percent of the overall cost of operations.
As we consider and benchmark labor costs for the industry’s specific skill set, we actually find unique wage levels that may come as a surprise to many. Odessa (TX), Albany (NY), Fort Collins (CO) and Bridgeport (CT) are the highest-paying markets for the industry, with average wages over $32 per hour. These wages, which outpace those of the general workforce in each respective market, prove the uniqueness of the plastics industry. On the opposite side of the spectrum, according to BLS, Medford (OR), Greenville (NC), Johnson City (TN), Utica (NY) and LaCrosse (WI) are all below $19 per hour across the industry.
Talent Pipeline
Understanding the available skills in prospective markets is vital to any location strategy. However, looking at the figures of today only tells part of the story leaders need to know. Companies in the plastics industry must evaluate the talent pipeline to address the future skill requirements of the business.
Across the country, economic developers and academic institutions, in partnership with business leaders, are developing workforce training and skill development programs. These programs, which come in a number of different forms, are initiatives that work to develop the skills required for local businesses, as well as develop the trades needed for the future.
A great example of an academic institution supporting the skills of the industry comes out of the Badger State. Wisconsin has long been known as a strong engineering and manufacturing center with a diverse set of sectors across the state. Nevertheless, as we’re seeing around the world, finding top talent with core engineering skills can prove to be a challenge in today’s ultra-competitive war for talent.
In an effort to improve the local workforce, while supporting existing businesses and prospective companies, the University of Wisconsin-Milwaukee, a school with robust engineering programs, has created a Plastics Technology Certificate program. With a wide-ranging curriculum, the certificate program was created, as university literature says, to “develop a foundational knowledge of plastics, covers in-depth features of plastics design and helps you stay competitive in the industry.” Developed for engineering graduates, programs like this can drive the specific skills for communities and businesses alike to ensure a sustainable talent pipeline for the future.
Access to Feedstocks
Foreign investment in the U.S. is driven by several factors, such as customer market entry, business friendliness and skilled workforce. However, in many cases, the expansive availability of raw materials and direct access to natural resources are primary reasons to enter the American market. Without question, the monumental, sustained success of the American plastics industry is directly related to the discovery, development and availability of fossil fuels, primarily natural gas.
Having a reliable pipeline of natural gas at a low-cost and stable price point has helped the American plastics industry thrive and provides a significant advantage over major players in the global marketplace. Natural gas isn’t just a power source for the industry, but also is critical in the process for polymer development.
When locating a plastics manufacturing or processing facility, ensuring access to natural gas is vital. Even if a natural gas pipeline is in close proximity to a site, having a direct connection to transmission lines is critical for a successful location. This is an important element of any industrial site selection decision, which is occasionally overlooked. Creating that connection can prove to be more costly than expected as many aspects can come into play, including eminent domain and environmental hurdles. If connectivity does not exist for a site, utility companies and economic developers may have funding programs and financing tools that may be able to support the extension at little or no cost to the company.
Cost of Power
Along with natural gas connectivity, further reliable sources of energy at an affordable cost are important for locating a plastics facility. Rates for electricity, and the sources of energy, vary greatly across the country, even within the same state. Additionally, access to the grid and state regulatory standards, especially dealing with 24/7 operational facilities, are core aspects to understand when conducting a site selection study.
When it comes to power rates, costs can even differentiate greatly within a market. Evaluating the power load requirements, including potential seasonal shifts, is a first step to reviewing this aspect. Once understood, a financial model should be run for each prospective site to calculate potential costs.
To help offset these costs and encourage economic development, many utility providers are now equipped with tools to help with power costs for industrial users. Commonly known as Economic Development Riders, utilities may be able to provide businesses with a reduced rate if the industrial user is willing to commit to certain capital investment levels and power baseload increases, and in some cases, new jobs.
Effective Supply Chain
Central to long-term operational success for a plastics facility is the ability to move raw materials, processed elements and finished products to and from the site. Depending on the unique facility requirements, transportation connectivity is vital to meet supply chain considerations.
For the American plastics industry, the interstate highway system is the primary mode of transportation, so proximity to highway interchanges can deliver critical cost advantages and operational efficiencies, as well as risk mitigation in relation to alternative modes.
The other primary mode of transportation for the plastics industry is freight rail, where over 100 million tons of plastic resin shipments move on an annual basis, which equals about 30 percent of the industry. Altogether, the American freight rail system is a 140,000-mile network with nearly 600 freight railroads, according to the Association of American Railroads, but still, finding an industrial site today with direct rail connectivity can be a significant challenge.
Customer Proximity
The expectations and demands of the American consumer are rapidly evolving, and in some markets, accelerating beyond current industry capacities. To address this dynamic state, certain manufacturing sectors are finding themselves locating closer to the customer, similar to the trends of the early 20th century. Drivers for customer proximity include customization delivery frequency and timing requirements, among other key factors.
Demand for more specialization in the plastics industry is driving more innovation, which also is bringing many manufacturing and processing facilities closer to the ultimate customer. Industries like medical devices and automotive are examples of those which are driving plastics production facilities to specific regions of the country, especially to markets in the Southeast and Midwest.
Plastic Recycling
Over the past 50-plus years, single-use plastic products have been a vital part of our everyday lives. Being able to effectively and affordably recycle these goods will be the core of a sustainable future.
The burden of single-use recycling isn’t just on the shoulders of the American consumer, but is also on the plastics ecosystem to continue innovating potential reuses of the products. To do so, location can play a major role. Along with innovation, partnering with communities, government entities and academic institutions can be pivotal for developing recycling pipelines, supportive laws and regulations and critical research.
Government Support Programs
When conducting a site evaluation, another core element to the ultimate location decision is the potential for partnerships through credits and incentives. Driven by economic development and business support policies, credits and incentives come in the form of financial and technical support through a public private partnership, which can present that final aspect to prove out a prospective location and deliver the confidence the business decision-makers require.
Community leaders and economic developers are developing and deploying support programs that target manufacturing projects. Programs targeting the plastics industry vary from state to state, and from community to community. These potential partnership opportunities come in many different structures, which can include tax credits, property tax abatements, cash grants, tax exemptions, workforce training support and infrastructure funding, among other mechanisms. Many of these programs are offered in a fully discretionary nature.
Dynamic Future
Approaching one million jobs across the American plastics industry, the overall impact of the sector to the national economy is significant, to say the least. With innovation and diversification across the industry, doing due diligence during the site selection process is critical to ensure facilities are optimally located.
When undertaking a site selection study, the core factors of the search must be considered and evaluated specifically to the specific nature of the project at hand. Critical site selection factors to be reviewed, at a minimum, in every plastics facility project include skills availability, talent pipeline, access to feedstock, energy costs and grid reliability, site readiness, infrastructure, consumer proximity, environmental regulations and government support programs. T&ID