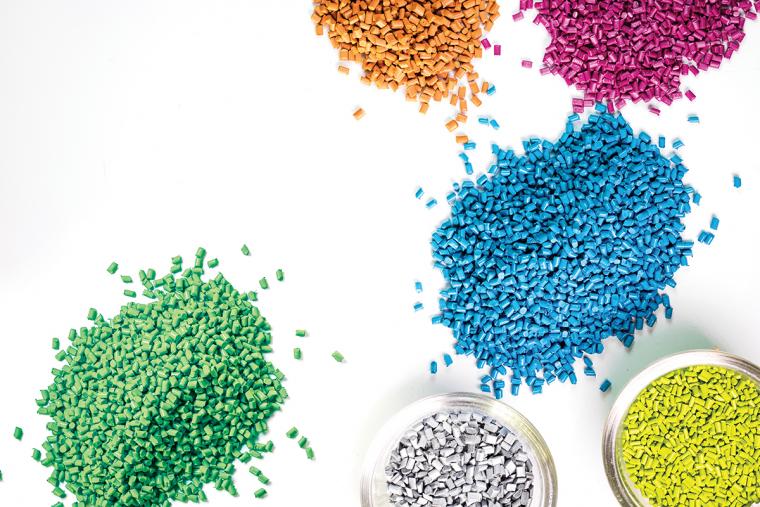
Since their first practical utilization in the 19th century, plastics are now involved in everything from food, cars, homes and everywhere in between. With a multitude of uses and an extensive list of feedstocks, plastics play a pivotal role in the American economy.
The manufacturing and processing of the plastics industry, which consists of multiple components, is key to economic development for many American communities. Where these facilities are today and where they’ll be in the future are critical to the future landscape of the nation’s economy, especially as the demand for skilled talent and access to raw materials becomes more prevalent than it is even today.
Critical factors for locating a plastics facility are often led by talent and feedstock access, along with site readiness, energy costs and infrastructure, transportation, proximity to consumers, economic development incentives and environmental regulations, among other vital aspects.
Economic Impact of Plastics
As a diverse and robust sector, the plastics industry is one of America’s largest in employment and total value. According to a 2016 study produced by the Plastics Industry Association (PLASTICS), the plastics industry accounted for 954,000 jobs and $418.4 billion in shipments in 2015. If suppliers are also considered, the total impact increases to an employment of 1.75 million and $571.5 billion in annual shipments.
The plastics industry, despite being hit hard by the 2008-2009 recession, has also seen vast growth over the past three decades. Since 1980, real plastics manufacturing shipments have grown at an annual rate of 2.4 percent, while employment in the industry has grown at 0.3 percent annually. Today, the plastics products portion of the sector was the eighth-largest industry in the country.
Texas, California and Ohio lead the nation in plastics industry jobs with each home to more than 74,000 employees. Michigan and Illinois round out the top-five states, with 68,200 and 50,900, respectively. Indiana has the highest concentration of plastics employment compared to all other U.S. states.
Dynamic Industry
Over the years, the main uses of plastics have evolved greatly. The primary channel for plastics is still manufacturing as companies purchase plastic materials to be processed into a final product. However, a shift is occurring for the ultimate downstream destination of plastic products, which is now led by the services sector.
The services sector, which is namely health services, wholesale and retail trade and food services, among others, accounts for more than one-third of the industry’s downstream consumption, according to the PLASTICS study. Approximately 30 percent goes to non-durable goods, while roughly 27 percent goes to durable goods, including transportation equipment and furniture. The remaining plastic products are consumed by the construction sector at nine percent.
Location Strategy
With today’s competitive and dynamic American economic landscape, decision makers must evaluate a long list of factors to ultimately choose a location for investments. It’s no different when it comes to locating a plastics manufacturing and production facility. These facilities have unique requirements that rely on a long list of key factors for success, all which must be understood and analyzed ahead of making a final site decision.
As previously mentioned, the critical factors, which are among thousands of data points to be reviewed, include:
• Workforce availability
• Labor costs
• Access to raw materials/feedstock
• Site readiness
• Energy costs and infrastructure
• Transportation
• Customer proximity
• Economic development incentives
• Environmental regulations.
With all the factors involved in site selection, no aspect is more extensively studied today than workforce availability. If a workforce doesn’t exist that meets the needs of the project, the long-term success of the business is at risk. Plastics require a workforce that has certain skillsets which must be identified and discovered, and can’t be found everywhere in the United States.
At the outset, businesses must have confidence in the local workforce when evaluating a new location. For the plastics industry, operations require employees with adequate experience and training in skilled trades, engineering and production backgrounds, among other core functions to the business. When narrowing a site search to a short list of locations, due diligence is often done through extensive labor analytics. With further analysis, the decision makers will be armed with the understanding of local workforce dynamics today as well as into the future.
Nevertheless, industry leaders are continuing to see challenges finding all the required skillsets for their operations. Much of that difficulty lies in finding and recruiting talent in the skilled trades, which often includes machinists, welders, electricians, technicians, process engineers and designers, among others. These challenges are across the board when it comes to manufacturing today, not just limited to the plastics industry.
Community leaders and economic developers are working with local businesses and academic institutions to directly address these workforce issues, many of which can directly support the plastics industry.
With many companies turning to internal training to upgrade employee skills, communities and academic institutions are developing programs to support the plastics industry. Administered by the Rhode Island Department of Labor and Training, state leaders have developed a tax credit for businesses investing in plastic process technician apprentices or machine tool and metal trade apprentices. Capped at 50 percent of actual wages paid or $4,800, whichever is less, companies can enroll qualified workers into an eligible apprenticeship program while being a full-time employee.
A joint initiative was developed earlier this year in Indiana, the state with the highest concentration of plastics industry employment, led by Ivy Tech Community College Southwest. Directly targeting gaps in advanced manufacturing, the program provides students an hourly wage while they complete a number of core classes and onsite work at a manufacturing company. Ultimately the program, which was established utilizing funds from the Indiana Department of Workforce Development, will provide students with soft skills training, OSHA certification and Manufacturing Skills Standards Certification.
Access to Raw Materials & Feedstocks
America is abounding with natural resources, helping the United States become the economic powerhouse it is now. Great success of the American plastics industry can be tied directly back to the discovery and development of fossil fuels. The fossil fuel of choice for the industry currently is natural gas, accounting for approximately 90 percent of production.
Reliable, low-cost natural gas has helped ensure the economics and has reduced risks for the plastics industry in America. First, natural gas is critical in providing the required power for facilities from coast to coast. As noted, power is not the only feature of natural gas for the industry, as the vast majority of polymer development is natural gas. Low-cost, reliable access to natural gas is certainly an advantage for American producers competing against other major players in the global market.
Core to the site selection search is often ensuring access to natural gas. Not only is market availability critical to site effectiveness, but also direct connection to transmission lines. The latter is vital for businesses considering industrial investments, not just for plastics facilities. If not currently in place, economic developers and local utility companies are often keen to support development of direct connectivity, possibly at little or no cost to the company.
Energy Costs and Infrastructure
Access to affordable and reliable energy is another key factor to ensure a successful site decision. The United States is a dynamic energy nation with varying sources powering businesses and homes. Electricity rates and sources are dependent on several factors, including geographical location, state regulatory standards and grid access.
As many facilities are operational 24 hours a day, a reliable source of energy is required. It is vital to ascertain all details of the site as communities vary in the delivery of electricity and fuel source.
Electricity rates contrast greatly between particular sites in the United States, even when considering locations within the same state. Validating the anticipated costs, and if possible, securing rates, will provide critical insight to the long-term impacts the site will have on the company’s bottom line. Utility providers may also be able to support by providing businesses with reduced rates, becoming commonly known as Economic Development Rates.
Logistics and Supply Chain
Movement of goods to and from a plastics production facility is core to long-term operational success. Transportation infrastructure must meet the unique and specific supply chain requirements for the facility.
The nation’s interstate highway system is the primary mode of transportation for the plastics industry. Proximity to the interstate system provides for vital cost savings and operational efficiencies pivotal for the industry. More than half of the nation’s plastic resins shipments travel on the interstate highway system daily.
Freight rail is also still core to the plastics industry, where over 100 million tons of plastic resins are moved annually. In total, over 30 percent of the shipments are moved over freight rail. Direct connectivity, or at least close proximity to rail, remains critical to the plastics industry, and the dependence is expected to continue into the future.
Economic Development Incentives
A site evaluation needs to be comprehensive of all the factors discussed in this article, among many more vital aspects to review. Economic development incentives are another key influence on a site decision for the plastics industry. Financial and technical support through a public private partnership can often be that ever-important final piece to making a location work and providing the confidence needed for the business.
Manufacturing projects are still of the most attractive for community leaders and economic developers to pursue, with many of the support programs built specifically for the industry. When conducting a site selection evaluation, economic development incentives need to be understood and valuated.
Public-private partnership opportunities for the plastics industry vary from state to state, and even further from community to community. Programs also come in many different forms, such as tax credits, property tax abatements, and cash grants, with some being fully discretionary in nature. An exhaustive review of the incentive opportunities is critical for the site selection process – not only for the potential value, but also understanding the possible risks, too.
Economic development incentive opportunities for the plastics industry can come from multiple levels of government, including federal, state and local jurisdictions, as well as, utilities, regional authorities and other relevant entities.
At the state level, program opportunities range across the country, mostly dependent on the state’s industry and workforce priorities, tax structure, financial status and political support, among other factors. One of the common economic development incentives deployed by state governments are sales and use tax exemptions for manufacturing equipment. Utilizing these exemptions, companies can avoid significant costs upfront when purchasing equipment for facilities.
Locally, communities in the United States have a number of tools and resources to attract manufacturing investment. A frequently utilized economic development instrument is a property tax abatement. These abatements, which come in many different forms, can be that key incentive to ensure the success of a project.
Conclusion
Accounting for 954,000 jobs and $418.4 billion in shipments annually, the American plastics industry remains a vibrant and robust force for the nation’s economy. As the industry continues to diversify, and input costs, like natural gas, continue to be stable, the plastics industry has a bright future for years to come.
As industry leaders embark on locating a new plastics facility, there are a multitude of factors that must be evaluated and understood. The vital site selection factors for locating a plastics facility are often led by talent and feedstock access, along with site readiness, energy costs and infrastructure, transportation, proximity to consumers, economic development incentives and environmental regulations, among other vital aspects. T&ID