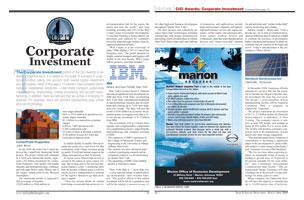
Corporate Investment
The Corporate Investment portion of the CiCi Awards is relatively straightforward. It is based on the scale of a project in a particular location, taking into account both overall capital investment and job creation. Most of this year’s 15 winners have achieved prominence in established industries – intermodal transport, automobile manufacturing, shipbuilding, metals processing and aircraft manufacturing. In addition, there are winners that are active in emerging industries. For example, there are winners representing solar power and nanotechnology.
CenterPoint Properties
Joliet, Illinois
In July 2008, the Joliet City Council approved the CenterPoint Intermodal North project. The project, which will culminate in a 3,600-acre intermodal facility, represents a $2 billion investment by CenterPoint Properties. This facility will handle domestic and international cargo containers and will make Will County, Illinois one of the largest inland ports in the Western Hemisphere. The intermodal facility is expected to deliver a range of benefits:
• $290 million to $344 million in new wages annually
• $601 to $765 million in operations economic impact annually
• $1.1 billion in construction economic impact
• 6,900 to 7,400 operations jobs
• 5,900 construction jobs
• 20 years of taxes at the park could net $138 million in taxes for Joliet and local school districts alone.
A similar facility in nearby Elwood already has achieved a vital boost for that community, with village revenues going up nearly 10-fold and annual wages in the village increased more than 50 percent.
In recent years, Illinois has moved to second in the nation in grain export volume, due in large part to the Elwood integrated logistics center. Considering more than 44 percent of Illinois grain is sold for export, access to transportation is essential for the region’s farmers to get their products to market.
"Joliet has always drawn its vitality from being a crossroads that serves as a vital transportation hub for the region, the nation and now the world," said John Greuling, president and CEO of the Will County Center of Economic Development. "Long-haul trucking is being phased out nationally and replaced by containers moved by trains through modern, clean integrated industrial facilities."
“Will County is at the crossroads of trade,” Mike Mullen, CEO of CenterPoint Properties said. “The global demand for freight container transport and logistics will double in the next decade. Will County will be poised to meet that demand.”
IBM
Albany and East Fishkill, New YorkNew York Governor David A. Paterson announced significant new investments by IBM and New York State, accelerating New York State’s international leadership in nanotechnology research and development and creating up to 1,000 new high-tech jobs Upstate. The State will provide a total of $140 million in economic development grants, leveraging more than a 10-to-one private investment of $1.5 billion from IBM.
The investment will go toward three separate and complementary components of a comprehensive project, supporting the nanotechnology chip computer activities of IBM:
• The expansion of IBM’s operations at the College of Nanoscale Science and Engineering at the University at Albany (Albany NanoTech)
• The creation of a new, advanced semiconductor packaging research and development center at a to-be-determined in Upstate New York
• The upgrading of IBM’s East Fishkill facility in Dutchess County.
“New York State is … more than ever … a clear national leader in nanotechnology development,” said Governor Paterson. “The positive effects of this critical investment will be felt for a generation, and will be the catalyst for other high-tech business development throughout Upstate New York.”
The three projects will collectively advance “nano-chip” technologies, including cutting-edge chip design, demonstration and testing which all takes place at Albany NanoTech. Nano-chips each carry billions of transistors, and applications include high-end personal computers and laptops; high-performance servers and supercomputers; virtual reality and advanced electronic games; medical devices and components; ultra-fast telecommunications devices; and “sensor-on-a-chip” systems for anti-terrorism and “soldier-in-the-field” remote monitoring and sensing.
Senator Joseph L. Bruno said, “Over a decade ago, we in state government developed an ambitious plan in which we sought to combine the resources of government, higher education and business to attract investment and job creation in the high tech sector. Today's announcement is the culmination of these efforts.”
Hemlock Semiconductor
Clarksville, TennesseeIn December 2008, Tennessee officials announced a project that has the potential to become the largest corporate capital investment the state has ever seen. The project, a polycrystalline silicon manufacturing facility, will be located at Commerce Park, a megasite in Clarksville, Tennessee.
The project represents an investment of $1.2 to 2.5 billion dollars by Hemlock Semiconductor, a subsidiary of Dow Corning. The company expects to employ at least 500 people, and perhaps as many as 900 within five to seven years. The facility will produce a primary component used in the manufacture of solar panels and other energy equipment.
“This announcement shows Tennessee’s commitment to becoming a significant player in the development of ‘green collar’ jobs related to clean energy technologies,” said Tennessee Governor Phil Bredesen.
“We live in a time when a growing reliance on sustainable forms of energy is leading to growth rates of 30 percent to 40 percent annually for the solar industry,” said Community Development Commissioner Matt Kisber. “This announcement means Tennessee will play a leading role in the growth of solar technology for many years to come.”
When complete, the Clarksville facility will have the capacity to manufacture up to 10,000 metric tons of polycrystalline silicon annually but is being designed with the capability to manufacture up to 34,000 metric tons. The plant will occupy the entire 1,215-acre megasite, and the company plans to acquire an additional 947 acres adjacent to the site for additional build-out and to provide buffer space.
“This huge success proves that going through the diligent megasite certification process gives a community a strong advantage,” said John Bradley, senior vice president, economic development, Tennessee Valley Authority. “Community leaders have been working towards this day for two and a half years.”
“Tennessee’s business climate coupled with a superb site in Clarksville, a strong, productive workforce and an excellent location in proximity to our supply chain and customers made this the right decision,” said Hemlock Semiconductor President and CEO Rick Doornbos.
Volkswagen Group of America, Inc.
Chattanooga, TennesseeVolkswagen Group of America, Inc. announced it would build a U.S. automotive production facility in Chattanooga, Tennessee, where it will produce a car designed specifically for the North American consumer and invest $1 billion in the economy. With the new plant, Volkswagen will bring about 2,000 direct jobs to the area. A University of Tennessee study estimates that another 9,477 jobs will be created in the region through construction and supplier activity.
The announcement is an important element of the company’s growth strategy, which involves a tripling of the company’s U.S. customer base in the next decade. “The U.S. market is an important part of our volume strategy and we are now very resolutely accessing that market,” said Prof. Martin Winterkorn, CEO of Volkswagen AG. “We will be selling 800,000 Volkswagens in the U.S. by 2018, and this new site will play a key role.”
The company will build the facility in the Enterprise South Industrial Park, located 12 miles northeast of downtown Chattanooga. The 1,350-acre site is 100 percent owned by the City of Chattanooga and Hamilton County and is certified as an industrial megasite by the Tennessee Valley Authority.
“We started with a vision of transforming an idle Army facility into the source of thousands of family-wage jobs,” said Hamilton County Mayor Claude Ramsey. “Over the last 14 years, I’ve worked with four different city mayors as well as county commissioners, city councilmen and countless others in overcoming barriers and objections to that plan. Today, we stand with our new friends from Volkswagen to make a historic announcement that will create new opportunities for our community for years to come.”
BMW Manufacturing Corporation
Spartanburg, South CarolinaIn March 2008, BMW and the South Carolina Department of Commerce announced that BMW would invest an additional $750 million in its Upstate South Carolina operations, adding a new 1.2 million square foot assembly facility, which will be sited north of an existing factory. The investment, the largest ever announced for the Spartanburg County factory, increases investments of the BMW Group in its South Carolina operations to $4.2 billion.
The new facility will be ready after a three-year construction project, and will employ an additional 500 workers. The expanded Spartanburg plant will manufacture three vehicles, the BMW X3 Sports Activity Vehicle, the X5 Sports Activity Vehicle, and the X6 Sports Activity Coupe. By 2012, production will increase from 160,000 to 240,000 units.
“The boost in the production capacity at BMW Manufacturing will positively impact the logistics, supplier and distribution networks that support the manufacturing processes,” said Josef Kerscher, president of BMW Manufacturing. While the supplier network may grow, existing supplier companies will ramp up operations to provide automotive parts for the higher production levels, doubling parts container traffic and significantly increasing exports through the Port of Charleston.
“BMW’s expansion in South Carolina will have a tremendous impact on the region and the entire state. We expect to see new suppliers come to the state and existing suppliers grow as a result of this announcement and that means new jobs and lots of new supplier jobs all over South Carolina, said South Carolina Secretary of Commerce Joe Taylor. “BMW is truly the nucleus of a job-creating machine.”
Canon Virginia, Inc.
Newport News, VirginiaVirginia Governor Timothy M. Kaine announced that Canon Virginia, Inc. would invest a total of more than $600 million as part of its “Vision for the Future” program. The investment will be used to expand Canon Virginia’s operations in Newport News, including the construction of a new manufacturing facility. It will also enhance the repair and refurbishing operations for select Canon products. These developments involve the planned creation of more than 1,000 new jobs.
In addition, Canon will invest to expand its Industrial Resource Technologies, Inc. (IRT) subsidiary, owned by Canon Virginia and Canon U.S.A., in Gloucester County. IRT recycles toner cartridges and reclaims cartridge materials. This part of the expansion plans is expected to create additional jobs.
“Canon’s planned total investment and creation of more than 1,000 jobs is spectacular news for Virginia,” said Governor Kaine. “Canon Virginia has been a significant corporate partner to Newport News and the Commonwealth for 23 years and employs nearly 1,500 Virginians. A key driver of the expansion decision was the development of a workforce pipeline to recruit and train the many new employees, and the Virginia Community College System stepped up to the plate to provide a solution for Canon in the Hampton Roads region.”
Headquartered in Newport News, Canon Virginia, Inc. serves as the lead manufacturing support center for Canon U.S.A. “We are excited about this tremendous opportunity to grow and expand our operations in Virginia,” said Mr. Takayoshi Hanagata, president and CEO of Canon Virginia Inc. and IRT. “We appreciate the outstanding support of our many partners at the Commonwealth of Virginia, the City of Newport News and Gloucester County who are assisting in making our vision for growth in Virginia a reality.”
Spirit AeroSystems, Inc.
Kinston, North CarolinaNorth Carolina Governor Mike Easley announced that Spirit AeroSystems, Inc. would open a manufacturing plant at the state-owned Global TransPark in Kinston. Plans call for investment of more than $570.5 million and the creation of 1,031 jobs during the next six years.
Spirit AeroSystems supplies commercial airplane assemblies and components to prominent manufacturers such as Airbus, Boeing, Gulfstream, Cessna and Hawker Beechcraft.
“[This project] not only shows that eastern North Carolina can successfully compete in today’s global marketplace, but that North Carolina continues to be a leader in the aerospace industry more than 100 years after the Wright Brothers made their historic first flight at Kitty Hawk.”
State grants from the One North Carolina Fund and Job Development Investment Grant program and a grant from the non-profit Golden LEAF Foundation to the Global TransPark Authority helped make the project possible.
“The State of North Carolina met our requirements for financial incentives and this location offers a strong industrial base, a runway, port access, a growing labor force and an excellent technical training system,” said Spirit President and CEO Jeff Turner.
The Global TransPark, a 2,400-acre industrial/airport site, was designed in the mid-1990s to attract industry to help the area transition from a tobacco-based agricultural economy to industrial manufacturing. Spirit’s long-term plans call for the Global TransPark facility to serve as a composite manufacturing Center of Excellence, using advanced technology in its production processes.
Incentives extended to Spirit are tied to performance targets. If the company meets all of its performance targets, the benefits from the incentives could be worth more than $67 million. In addition, Golden LEAF – a nonprofit organization that uses money from the master settlement with cigarette makers – is providing a $100 million grant to the Global TransPark Authority to pay for construction of the initial buildings for Spirit.
SSAB
Axis, AlabamaAlabama Governor Bob Riley announced that SSAB, a global steel producer, decided to locate a new heat treating facility in Axis, creating 180 jobs. The new facility, where production will commence in 2011, represents a $460 million capital investment. It serves to expand an existing SSAB plant in Alabama’s Mobile County. At this plant, SSAB already employs 400 full-time workers, as well as 350 contract workers.
"SSAB could have gone anywhere in the world to locate this new plant," said Governor Riley. "That they picked Mobile only goes to show that Alabama can not only produce anything in the world in a high-quality fashion, but that we also have one of the best workforces in the country."
The heat treatment facility will produce quenched and tempered steel plate, which is used throughout the manufacturing and construction sectors in applications where properties such as strength, hardness and toughness are required beyond those available in commercial grades. The expansion will quadruple the Axis plant’s capacity to make quenched and tempered steel plate, producing 440,000 tons a year of the high-end product.
Neal Wade, executive director of the Alabama Development Office, said, "This is a very significant project for Alabama and underscores the importance of the steel industry in our state. We won this because of the great partnership between the state, local governments and the state port authority."
American Titanium Works LLC
Laurens and Greenville Counties, South CarolinaSouth Carolina Governor Mark Sanford and Thomas Sax, CEO of American Titanium Works (ATW), announced that ATW would build a world-class titanium mini-mill facility in Laurens County, South Carolina. American Titanium Works LLC will invest an estimated $422 million and plans to employ 320 people at its new facility.
ATW also announced that it will establish its applications development and engineering technical center in Greenville County at the Clemson University International Center for Automotive Research (CU-ICAR) campus. ATW’s Tech Center will create 40 applied engineering jobs that will specialize in prototype development and fabrication techniques for multiple industry sectors.
"Highly efficient, rolled titanium holds great promise for the Department of Defense and other industries, because of the metal’s strength and light weight," said U.S. Senator Lindsey Graham. "ATW’s Tech Center in Greenville County and manufacturing facility in Laurens County will play an important role in developing new titanium applications and partnerships in a variety of industries. We are proud to have them in the Upstate."
By producing melted and rolled titanium products through innovative processes, ATW will reduce the costs and lead times associated with traditional titanium production, thus making the product desirable to a broader range of industries including defense, industrial, commercial, consumer and emerging markets.
“ATW’s production of rolled titanium in South Carolina presents tremendous opportunity to grow existing industries in our state and attract new industries and investors from throughout the world. We welcome ATW to South Carolina and look forward to a long and mutually beneficial relationship with them in the years ahead,” said Joe Taylor, South Carolina Secretary of Commerce.
AREVA Newport News, LLC
Newport News, VirginiaAREVA and Northrop Grumman Shipbuilding, a sector of Northrop Grumman Corporation, will invest $363.4 million to partner in a joint venture to manufacture equipment and pressure vessels for the nuclear industry and to provide nuclear engineering services. The new company, AREVA Newport News LLC, will be established in Newport News. It will create 540 new production and engineering jobs.
“This joint venture project is tremendous news for Virginia,” Governor Timothy M. Kaine said. “Both AREVA and Northrop Grumman are stellar companies with strong reputations and a solid presence in Virginia.” AREVA’s presence in Virginia dates to 1957. Today, Lynchburg, Virginia hosts the company’s largest U.S. operations with more than 2,000 employees and the headquarters of AREVA NP Inc. Northrop Grumman Corporation has 16 primary locations in Virginia employing more than 35,000, making it the largest technology/manufacturing private employer in the Commonwealth.
A joint venture between two top Virginia companies who worked together in conjunction with Governor Kaine and a team of economic development professionals underscores Virginia’s collaborative approach to economic development.
“We are establishing a world-class entity that fully supports the deployment of a fleet of U.S. Evolutionary Power Reactors made in America by Americans and for Americans,” said AREVA Inc. CEO Tom Christopher. “Here in Virginia, we have access to a great workforce for both the manufacturing and engineering expertise we need.”
“Our shipbuilders embrace the opportunity to apply their considerable skills and training to a growing U.S. energy sector,” said Mike Petters, corporate vice president and president of Northrop Grumman Shipbuilding. “[They will employ] the same dedication and commitment to domestic energy security that has been applied to national security.”
Spirit AeroSystems
Wichita, KansasSpirit AeroSystems selected its Wichita facility as the site where the company will design and manufacture the fuselage for the new Cessna Citation Columbus. To accommodate the manufacturing and testing of the Columbus fuselage, Spirit plans to build a new 375,000-square-foot factory. The facility will also provide additional capacity for existing products and other new programs.
Over the next five years, Spirit expects to invest approximately $260 million and create an estimated 700 jobs with a projected annual payroll of more than $42 million in the state of Kansas. “We said all along that our desire was to design and build the Cessna Columbus in Wichita,” said Jeff Turner, Spirit president and CEO. “Working together with state and local partners, we were able to close the business case for the Columbus and other new programs, enabling us to make this investment in the Wichita site. Through this partnership, we were able to combine Spirit investment, including customer program support, with state and local incentives to maintain and grow jobs in Kansas.”
Spirit AeroSystems has expanded production on current airplane programs and won multiple new contracts across the aerospace industry since its formation in June 2005. The State of Kansas and the Greater Wichita Economic Development Coalition played key roles in securing the additional work and resulting jobs for Wichita and Kansas.
The Kansas Department of Commerce and the Greater Wichita Economic Development Coalition worked closely with Spirit to secure the investment in the new facility. The Kansas Department of Commerce committed $14.5 million in funding to help secure the Spirit investment. The City of Wichita and Sedgwick County committed $3.2 million total, or $1.6 million each, and a 10-year property tax abatement.
Austal USA
Mobile, AlabamaIn Mobile, Alabama, Austal USA broke ground on its Modular Manufacturing Facility (MMF), which will be capable of constructing six large aluminum vessels such as the Navy’s Littoral Combat Ship (LCS) and/or Joint High Speed Vessel (JHSV) per year. The MMF, which will expand Austal USA’s existing Mobile operations, represents a $254 million investment. Once complete, the MMF will accommodate a workforce of up to 1,200 personnel.
Located on Dunlap Drive, just south of Addsco Road, the MMF facility will include 700,000 square feet of manufacturing space, 80,000 square feet of warehouse space, and 60,000 square feet of office space. In addition to the buildings, the site will provide new permanent parking spaces for Austal USA’s employees. The expansion will be constructed in two phases and will ultimately accommodate a total workforce of up to 1,200 personnel in the new buildings.
Besides providing direct employment, the MMF project will direct work to several Alabama-based contractors. Gray Construction, located in Birmingham, Alabama, is managing the construction for Austal and will oversee all activities related to completion of the site. S J & L, Inc., of Mobile, will perform the earthwork, grading, curbing, paving and associated wet utilities for the project. Other local contractors involved in the expansion effort have included Dees Engineering, which completed the site design, and Thompson Engineering, which performed the geotechnical testing.
Kumho Tire
Macon, GeorgiaKorean tire manufacturer Kumho Tire will locate its first U.S. manufacturing facility in Macon, Georgia. The new plant, which will create 450 jobs, represents an investment of $225 million. It will cover 1.3 million square feet, occupying a 127-acre site at the Sofkee Industrial Park in south Bibb County and will initiate production in October 2009.
This new facility will enable Kumho Tire to increase supply to U.S. automotive manufacturing sectors and further penetrate the North American market. “The U.S. is the largest tire market in the world,” said Sae Chul Oh, Ph.D., CEO and president of Kumho Tires Co. “Kumho Tire can reduce its freight costs and increase market share in the U.S. by having a manufacturing plant here in Georgia.”
“Georgia’s ability to attract Kumho Tire shows the strength of our workforce and our unparalleled transportation network,” said Georgia Governor Sonny Perdue. Besides citing Georgia’s strong workforce and unparalleled transportation network, local and state officials assembled a comprehensive incentives package valued at more than $35 million. The package included items such as site preparation, establishment of a Foreign Trade Zone, employment and training services, and job tax credits.
By any measure, the Kumho plant is a significant project. But it is even more significant in light of Macon’s loss, in 2004, of the former Brown and Williamson plant, which eliminated 1,200 jobs and had ripple effects across all of Middle Georgia. Kumho is the first major project for Macon since Brown and Williamson left. This project’s benefits are expected to spread beyond Macon, affecting the entire region.
Cessna Aircraft Company
Wichita, KansasCessna Aircraft Company will build the Citation Columbus plant in Kansas, creating an estimated 1,010 jobs with an annual payroll of $74 million. Research shows that each aviation job creates an additional 2.9 jobs, which means a total of nearly 4,000 new jobs in Kansas as a result of the new plant.
Cessna had indicated that its preference was to locate in Kansas, especially because of Wichita’s skilled work force, the National Institute for Aviation Research, and the new technical training school at Jabara Airport.
The new plant, an expansion of Cessna’s Wichita operations, represents an investment of $200 million. It is part of Cessna’s $780 million investment into development of the Citation Columbus, Cessna’s newest and largest business jet. The new plant will be a stand-alone facility that will house engineering offices and final assembly of this state-of-the-art $27 million business jet. Preliminary plans call for construction of more than 800,000 square feet of buildings and 14 acres of airfield pavement.
Local and state loans and bonds in support of the project totaled $45 million. This amount was augmented by an additional State package consisting of training dollars and other incentives. The package exceeded $70 million.
The Greater Wichita Economic Development Coalition worked closely with the State Department of Commerce and local partners to help secure financial incentives for the project, as well as the state response. “Cessna fully appreciates the partnership and support we have had at state and locally,” said Cessna Chairman, President and CEO Jack J. Pelton. “The economic development coalition, the Chamber, the City of Wichita and Sedgwick County all spoke with one voice and were seamless.”
Willard & Kelsey Solar Group
Perrysburg, OhioA former television components plant in the City of Perrysburg, Ohio, is being re-purposed to accommodate Willard & Kelsey Solar Group, LLC, a manufacturer of thin cell solar panels. Willard & Kelsey intends to locate its headquarters, research and development, and initial production operations at the location.
Willard & Kelsey, formed in November 2007, plans to invest $166 million in the relocation project, which is expected to create 400 new full-time jobs and retain 10 existing full-time jobs within three years of the project’s initial operations.
The project includes the acquisition of a 252,000-square-foot manufacturing facility. It will house four production lines for the manufacturing of a vacuum-coating, patented, proprietary system for the production of new thin cell solar panels.
Ohio was in competition with Kentucky, Florida and Mississippi for the project. To help attract the company, Ohio approved a $5 million Research & Development Investment Loan at an interest rate of 1 percent for the first year and 2 percent for the remainder of the five-year term. The loan is for the purchase of machinery and equipment to be located at its facility in the City of Perrysburg.
The company has been awarded a 60 percent credit for a 10-year term for the company’s relocation to Perrysburg. The value of the tax credit is estimated at approximately $3.5 million over the term, and the company would be required to maintain operations at the project site for 20 years.
Related Agencies
- Will County Center for Economic Development
- TVA Tennessee Valley Authority Department of Economic Development
- Chattanooga Area Chamber of Commerce
- Spartanburg Economic Futures Group
- North Carolina Global Transpark Authority
- Mobile Area Chamber of Commerce
- Laurens County Development Corporation
- Greater Wichita Partnership
- Macon Bibb County Industrial Development Authority