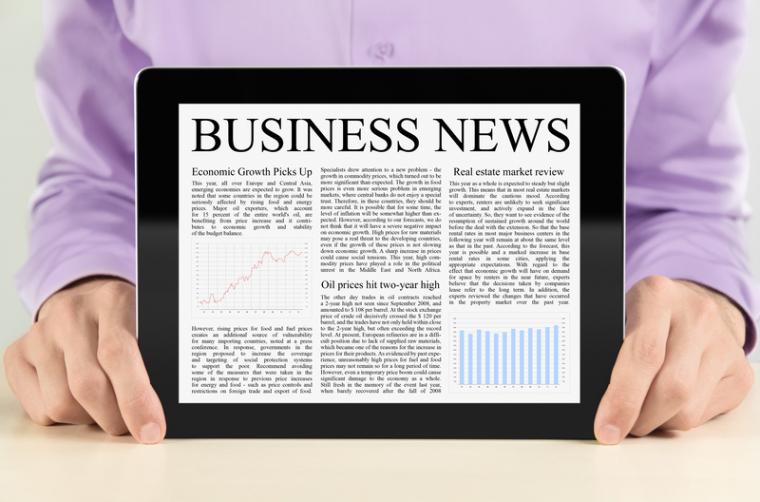
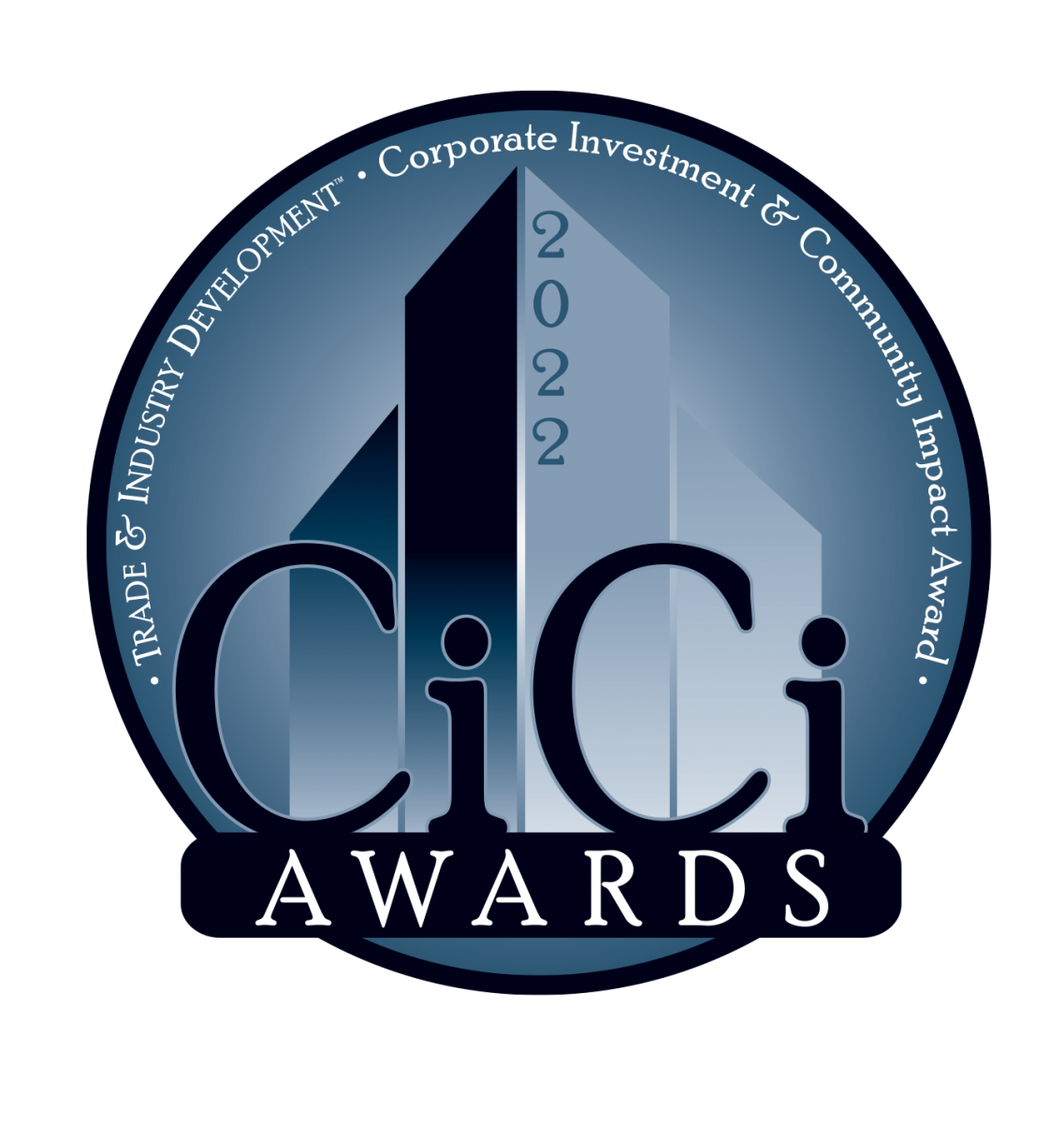
The collective capital investment of our 14 winning projects totals over $4.1 billion, and these initiatives will create nearly 10,000 new jobs and save more than 441 existing jobs. In many cases, the jobs created and the revenues generated are helping to stabilize communities in need of employment and infrastructure improvement for their residents, particularly during the era of COVID-19 and the economic uncertainty it has wrought. Also, success breeds success — many community leaders emphasize that the addition or expansion of a business will help to attract similar businesses and even more investment, and create thousands more indirect jobs.
These are just a few of the inspirational stories behind our 2022 CiCi Community Impact winners. None of these projects, of course, would have been possible without the hard work of community leaders, local and state economic developers, along with the visionaries at the companies themselves. Read more about how the transformation of a company’s location can make a huge difference in their communities.
FUJIFILM Diosynth Biotechnologies
Wake County, North Carolina
FUJIFILM Diosynth Biotechnologies is a Denmark-based contract development and manufacturing organization (CDMO) specializing in biopharmaceuticals. In March 2021, the company announced plans to build the largest end-to-end cell culture CDMO biopharmaceutical manufacturing facility in North America in Holly Springs, North Carolina. The facility, which is expected to be completed by spring 2025, will bring 725 high-quality jobs for scientists, quality control workers and supply chain experts. The development will join the company’s other Wake County facility in Morrisville.
The $2 billion project represents the largest life sciences investment ever announced in the state. The new facility will offer large-scale cell culture manufacturing of bulk drug substances as well as commercial scale, automated fill-finish and assembly, packaging and labelling services.
In addition to being the largest end-to-end cell culture CDMO biopharmaceutical manufacturing facility in North America at its completion, the FUJIFILM Diosynth project will serve as a model for sustainability. It will target 100 percent clean energy use, implementation of cutting-edge waste disposal and recycling and a 45 percent reduction in the volume of CO2 emitted across the entire product lifecycle compared to 2014. The company was partly attracted to the site because of Holly Springs’ reclaimed water system that can be used at the site. In addition, the facility will build strong connections with the local community, including K-12 system, to serve as a resource for environmental learning.
The total economic impact is also significant. The project is expected to infuse $2.6 billion into the Wake County economy with $1.6 billion of that going directly into the Holly Springs economy by the end of 2025. After the facility opens, the town will benefit from an additional $422 million economic impact annually, which will enhance the diversification of Holly Springs’ tax base.
The company’s investment was met with funds from several discretionary incentive programs, including approximately $24.6 million from the state, $55.5 million from Wake County and $45 million from Holly Springs. It will also earn $1.8 million in workforce credits.
“We are passionate about the tremendous value that this new facility will bring to our partners in producing life-impacting therapies,” said Martin Meeson, CEO of FUJIFILM Diosynth Biotechnologies. “To build what will be the largest end-to-end cell culture CDMO facility in North America requires commitment and partnership. “We are delighted to have received the strong support from the town of Holly Springs and the state of North Carolina. This is building for the future, both in infrastructure and in talent, as part of the vibrant North Carolina biotech hub.”
Louisiana Green Fuels
Caldwell Parish, Louisiana
In April of 2021, Louisiana Green Fuels, a subsidiary of Strategic Biofuels, LLC, announced plans to develop a renewable diesel plant near Columbia, Louisiana, the parish seat of rural Caldwell Parish, with an investment of more than $705 million. The new plant has been projected to create 76 direct jobs, with an average salary of $68,000, plus benefits. Louisiana Economic Development estimates the project will result in 412 indirect jobs in Caldwell Parish and the surrounding region. At press time, the company was completing the feasibility and financing phases, anticipating a final investment decision by late 2022.
The announcement was the first of two carbon sequestration projects to be announced in Louisiana in 2021, but what set Louisiana Green Fuels apart was its location. Caldwell Parish is the sixth smallest parish by population in Louisiana. More than 19 percent of the population falls at or below the poverty rate. Not only does Louisiana Green Fuels provide the potential for much needed economic activity and jobs; the renewable fuels plant will bring green energy jobs to the rural Louisiana parish.
The renewable diesel refinery will rely upon wood waste and forest thinnings as the feedstock for the gasification process that produces renewable diesel fuel. Caldwell proved to be an ideal location for three reasons: the geology is well-suited for carbon capture and sequestration, it is near Louisiana’s forestry sector, and Louisiana is taking a leading role in carbon-capture technology, supported by legislation. A project that employs locals in a rural setting and is a key step in Louisiana’s carbon reduction plans makes Louisiana Green Fuels an exceptional win for Caldwell Parish.
The company is expected to receive the services of LED FastStart (with a private sector value of $1.3 million). Additionally, the state is providing the company with a performance-based grant of up to $4 million. In addition, Louisiana Green Fuels is expected to make use of the state’s Quality Jobs and Industrial Tax Exemption programs.
“Caldwell Parish is the ideal location for our Louisiana Green Fuels plant,” said Dr. Paul Schubert, CEO of Strategic Biofuels. “It combines the required forestry waste feedstock for fuel production and the right geology for carbon sequestration within the State of Louisiana’s visionary legislative framework, which has been further strengthened by the Climate Initiative established by Governor Edwards. We are especially thankful for his signature on the recent $200 million tax-free bond allocation, which substantially advances the financing for this project.”
E & J Gallo Winery
Chester County, South Carolina
In June 2021, E&J Gallo Winery announced it would build a new production facility and distribution center in Chester County at a 650-acre rural site near Interstate 77 in the corridor between Charlotte, North Carolina, and Columbia, South Carolina. While the company operates primarily on its home site in Modesto, California, it wanted to expand to the East Coast, where two-thirds of its customers live and where major ports will aid in the shipping of products overseas more efficiently while Gallo works to reduce its carbon footprint.
Gallo’s initial $423 million investment is expected to create 496 new jobs in the next eight years. The company has said its long-term vision includes raising its stake to $1 billion and more than 1,000 jobs over the next three decades.
The Coordinating Council for Economic Development has approved job development credits related to this project. A $16 million Rural Infrastructure Fund grant was also awarded to Chester County to assist with costs. Also, the South Carolina Department of Commerce received authorization for $8 million in bonds to offset costs of off-site mitigation under the Economic Development Bond Act.
Chester County was hit hard by the collapse of the textiles industry in recent decades and is now recovering. E&J Gallo plans to pay its workers an average of $21 an hour, about $4 more than the local average, which will contribute to a broader economic boom in the county as Charlotte’s growth moves south and Columbia’s moves north.
The company’s effect on quality of life and opportunity also will extend into the recreational and environmental realm. Land donated to the state to mitigate wetlands loss is part of a plan to create a state park adjacent to a long-dammed riverway that is expected to soon see water flow again – in cooperation with Duke Energy – in a project that will create kayaking and other opportunities.
Gallo also is working with the Clemson Extension Service to study the feasibility of growing grapes in Chester and surrounding counties through which the Catawba River flows, bringing new business opportunities and connectivity to those areas, as well as advances in viticulture that could be shared far beyond the region.
“We could not be more appreciative of the collaboration and support shown by the state of South Carolina, the South Carolina Department of Commerce, and those in Chester County along with all of the public and private entities who have embraced this project throughout the planning process and have welcomed us to the community,” said Ernest J. Gallo, CEO of E & J Gallo Winery.
Great Lakes Cheese
Abilene, Texas
Great Lakes Cheese (GLC) is an award-winning manufacturer and packager of natural and processed bulk, shredded and sliced cheeses. In May 2021, the company announced plans to expand into Abilene, Texas thanks to the extensive efforts on the part of The Development Corporation of Abilene (DCOA) to attract the project. The company projected a total capital investment of $184.5 million through 2030 to build a new manufacturing and distribution facility to serve the state and surrounding areas.
The project required a 75-acre greenfield site to house the company’s planned 286,500-square-foot facility, which is expected to create 510 jobs by 2030. The facility will require a wide variety of jobs including engineers, managers, supervisors, assembly line workers, warehouse workers and machine workers. GLC began construction in 2021 and the facility is expected to become fully operational by 2022. Operating at full capacity, the plant will generate approximately $33,624,991 in annual payroll, with an average wage of $60,000, which is $15,000 greater than the county’s average wage. The GLC project will accomplish one of the county’s long-term objectives of raising the average wage of the community. As a result of the higher wages, local existing industries are expected to raise their wages to remain competitive.
The total incentive package to win GLC’s commitment to Abilene was a $36.6 million. The DCOA Board of Directors approved a $33.3 million incentive package that was comprised of a $30 million cash incentive and a $3.3 million in-kind incentive of land and betterments. In addition to the DCOA’s incentive package, the City of Abilene waived primary development fees. The DCOA also applied for and received a $3 million Texas Enterprise Fund (TEF) Grant and a $50,000 Veterans Grant through the Office of Texas Governor Greg Abbott.
According to a study commissioned by the DCOA from Impact DataSource, LLC, the GLC will contribute an estimated $13,451,805 in city taxes, $8,669,001 in county taxes, and $17,380,765 in school taxes in Abilene over a 10-year period.
“This groundbreaking marks the beginning of our generational commitment to Abilene,” said Dan Zagzebski, CEO of Great Lakes Cheese. “Great Lakes Cheese’s expansion into Texas represents our dedication to provide exceptional service to our customers. We look forward to investing in this great community and our Abilene employee-owners.”
Oshkosh Defense
Spartanburg, South Carolina
Oshkosh Defense, a subsidiary of Oshkosh Corporation, announced plans to establish new operations in Spartanburg County in June 2021. The $155 million investment is expected to create more than 1,000 new jobs. Founded in 1917, Oshkosh Defense is a tactical vehicle manufacturer that specializes in designing and manufacturing a diverse portfolio of heavy, medium, light and highly protected vehicles and technologies for clients around the world.
Located at the Flatwood Industrial Park in Spartanburg, Oshkosh Defense’s new operations will support the U.S. Postal Service Next Generation Delivery Vehicle (NGDV) program. The company will manufacture zero-emission battery electric vehicles and fuel-efficient low-emission internal combustion engine vehicles that will replace USPS’ existing fleet of delivery vehicles. This electric vehicle production operation will change the landscape of EV manufacturing and capabilities throughout South Carolina. Production of the NGDVs is expected to begin in 2023.
The project reinforces South Carolina’s position as an automotive manufacturing leader. Additionally, it underscores the state’s prioritization of electric vehicle production and sustainable manufacturing.
To help attract the project, the South Carolina Coordinating Council for Economic Development approved job development credits. Spartanburg County was also awarded a $9 million Set-Aside grant to assist with costs related to the project.
When all USPS delivery vehicles are updated to the NGDV model, every vehicle in the fleet will be South Carolina-made. This long-term production process will create and maintain jobs for several decades to come, as well as creating opportunities for prolonged service partnerships with existing and potential suppliers. Such a long-term, innovative production project will have a reverberation effect on the automotive industry in South Carolina, as well as the entire Southeast.
“We’re proud to bring this historic undertaking to Spartanburg County,” said Oshkosh Corporation EVP and Oshkosh Defense President John Bryant. “South Carolina has a skilled workforce and a proven history in advanced automotive manufacturing – it’s the perfect place to produce the NGDV. More importantly, we know the people of the Upstate take pride in their work and their community. What we build together here will reach every home in the country.”
SafeSource Direct
Broussard, Louisiana
In the earliest days of the COVID-19 pandemic, the recommended personal protective equipment, or PPE, was limited in availability, with most supplies originating overseas. As the demand grew globally, the U.S. found itself in a difficult position. The shortage forced medical personnel to wear the same protective masks and surgical gowns for significantly longer than recommended.
SafeSource Direct, a joint venture of Trax Development and Ochsner Health, was founded in part to address these shortages. Last year, SafeSource announced plans to manufacture PPE at a new 400,000-square-foot manufacturing facility located in St. Martin Parish, Louisiana, and a retrofitted 80,000-square-foot manufacturing facility in Lafayette Parish. The facilities will manufacture some of the most needed PPE, including surgical tie masks, bouffant hair covers, shoe covers, isolation gowns, procedure masks, N95 masks and nitrile rubber gloves.
Both sites, though in different parishes, fall within the city limits of Broussard, Louisiana. SafeSource is investing a total of $150 million in the two sites, with $73 million for the Lafayette Parish site and $77 million for the St. Martin site. The projects will create a combined 1,221 new direct jobs and result in an estimated 992 indirect jobs.
The company will receive the services of LED FastStart (with a private-sector value of $9.6 million). Additionally, SafeSource will receive $10.5 million in performance-based grants. The company is expected to utilize the state’s Quality Jobs and Industrial Tax Exemption programs.
The 1,221 direct jobs that will be created come at a good time for a community in need of a boost. Several of Acadiana’s strategic industries were hit hard by the pandemic. Like many communities across the nation, the Acadiana region faced increasing unemployment. The May 2021 announcement by SafeSource was welcome news that many residents in Lafayette and St. Martin parishes were eagerly awaiting.
“COVID-19 brought to light our nation’s dependence on foreign countries, primarily China, for PPE,” said Justin Hollingsworth, SafeSource Direct’s CEO. “By manufacturing right here in Lafayette and St. Martin parishes, and selling directly, SafeSource Direct will be positioned to eliminate the lag times, uncertainty and frustration that plague international manufacturing and shipping. Our hope is that these facilities will lay the foundation for more independently sustainable health systems in the U.S.”
Smith & Wesson
Maryville, Tennessee
In October of 2021, firearms manufacturing company Smith & Wesson Brands, Inc. announced plans to relocate its headquarters and other major operations from Springfield, Massachusetts to Maryville, Tennessee. The project will be located in Partnership Park North in Blount County.
Smith & Wesson manufactures a wide array of handguns (including revolvers and pistols), long guns (including modern sporting rifles, bolt action rifles and shotguns), handcuffs, suppressors, and other firearms-related products for sale to a wide variety of customers, including firearm enthusiasts, collectors, hunters, sportsmen, competitive shooters, individuals desiring home and personal protection, law enforcement and security agencies and officers, and military agencies in the U.S. and throughout the world.
In addition to its headquarters, Smith & Wesson will relocate its distribution, assembly, and plastic injection molding operations to Tennessee. The project represents an investment of approximately $125 million and will create 750 new jobs. In moving to Tennessee, the company is joining a significant economic cluster: Tennessee ranks number one in the nation for employment in the small arms and ammunition sector, with employment increasing by 54 percent over the last five years.
In making the announcement, Smith & Wesson indicated that strong support from the State of Tennessee and Blount County, combined with the quality of life, outdoor lifestyle and low cost of living in the Greater Knoxville area, left it with no doubt that Tennessee was the ideal location for a new headquarters.
“Tennessee is known by the brands that call our state home, and Smith & Wesson adds an enormous boost to our portfolio,” said TNECD Commissioner Bob Rolfe. “We know that Smith & Wesson could have chosen anywhere in the world to relocate its operations and headquarters, and the fact they chose Tennessee underscores our state’s business-friendly environment and highly skilled workforce. The magnitude of this project will have a lasting impact on our state for years to come, and we appreciate the company for its significant investment in East Tennessee.”
The company will take advantage of the PILOT program (Payment In Lieu of Tax). Smith & Wesson will pay the Industrial Development Board of Blount County 40 percent of taxes that it would otherwise be charged for in Partnership Park North from January 1, 2024 to December 3, 2030. In 2030, the company will be eligible to buy Partnership Park North property and facilities for $1.
The Lion Electric Company
Joliet, Illinois
Illinois is poised for growth in the electric vehicle sector, with industry experts predicting EV jobs to double by 2024. In 2017, Rivian Automotive established an EV manufacturing facility in the central Illinois community of Normal, creating a significant number of jobs. Now, Illinois will expand its EV footprint further.
The Lion Electric Company, incorporated in Quebec in 2008, designs, develops, manufactures and distributes all-electric medium and heavy-duty urban vehicles. The company employed 417 people in its headquarters facility in Saint-Jérôme, Quebec as of the Spring of 2021. The Saint-Jérôme plant, the company’s sole operating plant, has an annual production capacity of up to 2,500 vehicles.
In 2020, Lion began a search for a location for a large-scale facility in the U.S. In May 2021, the company announced that it had selected Joliet for its first-ever U.S. manufacturing facility and the largest plant of its kind in the country. A minimum of $70 million will be invested to build a new 900,000-square-foot facility dedicated to the production of medium and heavy-duty electric vehicles in the U.S. The facility is expected to come online in the second half of 2022, setting into motion an annual production capacity of 20,000 zero-emission vehicles each year. The operation is expected to create 745 jobs in 2024, climbing to 1,418 jobs by 2025.
According to Lion Electric, the Joliet site was chosen because Illinois’ climate change policies align well with the electric vehicle market, and because the area has a ready supply of talent. The location provides excellent access to the company’s supply chain, which is concentrated in the Midwest, as well as a transportation network that provides ease of access to customers in the four corners of the country.
Lion qualified for the State of Illinois’ primary business attraction program, the EDGE incentive program. All in all, the Lion Electric program qualified for a total of more than $26 million in economic incentives from the state, Will County and the City of Joliet.
“This significant expansion into the U.S. market will not only allow us to drastically increase our overall manufacturing capacity of electric trucks and buses but to also better serve our customers, while adding critical clean manufacturing jobs that will form the backbone of the green economy,” said Marc Bedard, CEO and Founder of Lion. “I also want to acknowledge the crucial role that P33 and Intersect Illinois, civic groups committed to developing a long-term roadmap for the local tech industry, played in connecting Lion with the Chicago area’s business and civic community to help further commercial traction, as well as engagement with key workforce and supplier partners.”
Ellume
Frederick, Maryland
Frederick County is largely rural, but it has been building itself a reputation as a center for life sciences and pharmaceutical companies. This is good news for the community, as the industry brings significant jobs and investments.
In May of 2021, Australian digital diagnostics company Ellume announced that it will establish its first U.S. manufacturing operation in Frederick County, creating more than 1,500 new jobs by the end of 2022. Ellume, based in East Brisbane in Queensland, Australia, will lease about 200,000 square feet in two new buildings to accommodate demand for its diagnostic products targeting infectious diseases.
The Ellume COVID-19 Home Test was the first rapid self-test for COVID-19 detection authorized by the U.S. FDA for asymptomatic and symptomatic use without a prescription. With the CDC reporting that at least 50 percent of COVID-19 cases are transmitted asymptomatically, Ellume’s test is expected to play a crucial role as one of the only diagnostic tools authorized for non-prescription use as a screening tool in the U.S.
The company signed a $231.8 million agreement in February 2021 with the U.S. Department of Defense, in coordination with the U.S. Department of Health and Human Services, to accelerate domestic production of its COVID-19 home tests and support ongoing U.S. pandemic preparation and response. The Frederick facility will be the cornerstone of this production.
In addition to the hundreds of jobs the project will bring, the potential for Ellume’s growth in the U.S., especially with the ongoing coronavirus pandemic, is significant, which could mean more jobs and expansion at the Frederick location in the future.
“We look forward to building the foundation for Ellume’s long-term vision in the U.S. and recruiting the highly skilled talent in Maryland’s Biotech Corridor needed to fuel our flagship U.S. facility,” said Jeff Boyle, PhD, president of Ellume U.S. “Frederick is the ideal location for Ellume as we continue to work closely with the U.S. government in delivering COVID-19 tests to communities across the country. The facility will serve as a foundation for Ellume to support the domestic response to the COVID-19 pandemic and better prepare the U.S. for future public health crises.”
SCHOCK GmbH
Henry County, Virginia
Founded in 1924 and headquartered in Regen, Germany, SCHOCK GmbH is the inventor of quartz composite sinks. In 2021, the company announced plans to invest $85 million to establish its first U.S. manufacturing operation in Henry County, an operation that is expected to create 355 new jobs. The project represents the company’s first production site outside Germany, as well as a major economic boost for an economically distressed region. (Henry County’s unemployment rate is 7.6 percent.)
SCHOCK GmbH will occupy the Lot 8 Shell Building, a 95,500-square-foot facility on 14.7 acres in Patriot Centre Industrial Park. SCHOCK will complete its operation in phases. Phase one will be completed over a five-year period, during which the company will establish the manufacturing capability to produce quartz composite kitchen sinks in its new Virginia location. The Patriot Centre Industrial Park’s shell building was established specifically to attract high-paying jobs to the Martinsville and Henry County communities, and this project represents the fruition of these efforts.
Governor Northam approved a $1.7 million grant from the Commonwealth’s Opportunity Fund to assist Henry County with the project. The company is eligible to receive state benefits from the Virginia Enterprise Zone Program, administered by the Virginia Department of Housing and Community Development. In addition, support for SCHOCK’s job creation will be provided through the Virginia Talent Accelerator Program, a workforce initiative created by the Virginia Economic Development Partnership in collaboration with the Virginia Community College System and other higher education partners.
The program, which launched in 2019, accelerates new facility start-ups through the direct delivery of recruitment and training services that are fully customized to a company’s products, processes, equipment, standards, and culture. All program services are provided at no cost to qualified new and expanding companies as an incentive for job creation.
“For SCHOCK, this expansion is very special — it’s our first production site outside Germany,” said SCHOCK CEO Ralf Boberg. “The facility will serve the strongest growth market for our product category and allow us to meet demand for colored kitchen sinks with local ‘Made in the USA’ products. We are thrilled to have found the ideal location in Henry County. As an industrial business hub, the region has a well-qualified and dedicated workforce — one of the key success factors for us as a company — and its geographic location and interregional infrastructure are perfect for our needs.”
FFD GA Holdings
Macon-Bibb County, Georgia
FFD GA Holdings is a majority-minority-owned business that specializes in medical cannabis cultivation. FFD was one of six companies that had medical marijuana licenses approved by the Georgia Access to Medical Cannabis Commission after House Bill 324 was passed in 2017. Last year, the company chose Macon-Bibb County as its Georgia home, the third state in which it will build a facility.
FFD will build a 50,000-square-foot, state-of-the-art, GMP-certified medical cannabis cultivation and production facility that will invest $50 million into the local economy and bring 100 jobs to the area. FFD’s presence in Macon-Bibb County — the heart of the state — will allow quick distribution and utilization of a product that will help thousands with conditions including seizures, cancer and Parkinson’s disease.
The application process was a rigorous one that had the FFD team delve into every detail, especially safety. FFD met with local police and fire departments to ensure public safety was a high priority. Constant monitoring, with 360-degree camera coverage, plus secure access and a sophisticated product tracking system will be implemented to eliminate opportunities for diversion or theft.
FFD has a business model that invests in the community where it plants roots. Along with being 87 percent owned by Georgia residents, FFD has programs designed to donate revenue to local charities, governed by a board of community leaders, excluding members of the FFD team. This will ensure that Georgians will direct funding to deserving organizations that are most in need.
“FFD has assembled an impressive team of business, cannabis experts, and security professionals,” Robert Fountain, Chairman of the Macon-Bibb County Industrial Authority, told the Georgia Access to Medical Cannabis Commission in 2020. “This team is exceptionally qualified with management and operational expertise and is a trailblazer in medical cannabis research and educational initiatives.”
Jeremy Fort, CEO of FFD, noted that the FFD team is a mix of local Georgians who know and love the state, plus best-in-class medical marijuana and pharmacy operators.
“Our team is eager to bring such a powerhouse group to provide excellent and safe medication to patients around Georgia,” said Fort. “We will be a partner in the community, supporting charities throughout the community. We plan to work with healthcare, veterans, substance abuse and academia.”
AMPAC Fine Chemicals
Petersburg, Virginia
AMPAC Fine Chemicals (AFC), a manufacturer of active pharmaceutical ingredients (APIs) in the U.S., last year announced plans to invest $25 million to expand its existing operation in the City of Petersburg. Virginia successfully competed with California and Texas for the project, which will create 156 new jobs.
AFC is a major collaborator in the new U.S. government-funded partnership with Phlow Corporation, Medicines for All Institute and non-profit drugmaker Civica Inc. Through this partnership, Phlow executed a $354 million contract with the U.S. Biomedical Advanced Research and Development Authority (BARDA) to produce essential medications using advanced manufacturing processes from the Medicines for All Institute based at the College of Engineering at Virginia Commonwealth University (VCU).
As part of this initiative, AFC will expand the former Boehringer Ingelheim chemical plant, purchased in 2016 and in operation since 2019. In January, Governor Northam announced that Civica Inc. would invest $124.5 million to establish a new facility adjacent to Phlow’s future operation and AMPAC’s existing facility. The Civica plant will convert active pharmaceutical ingredients from AMPAC and Phlow into vials and syringes of finished medications for use in hospitals.
AMPAC’s investment will further advance the pharmaceutical cluster that has emerged in Petersburg with Phlow Corp., Civica Inc., and AMPAC, which all share a vision for American-based manufacturing of essential medicines. As of August 2021, more than $500 million has been invested and 350 jobs have been created by Phlow, Civica and AMPAC.
By co-locating with each other on Normandy Drive in Petersburg, the three companies can share resources such as utilities and shorten transportation costs to produce an entire product at one site, resulting in significantly less cost than if they were located in separate areas of the country. Petersburg’s pharmaceutical cluster is set for more growth, and marketing efforts are underway to bring even more businesses into this economically distressed city and contribute to its resurgence.
“Of our three AMPAC locations, Virginia offers an enabling environment for developing and sustaining the growth in capacity and infrastructure demanded for the pharmaceutical industry,” said Dr. William DuBay, AMPAC Global Vice President of Research and Development. “Our growing relationship with the Commonwealth, VEDP, the City of Petersburg and others, including VCU, Phlow, and Civica, is a cornerstone of our vision for American-based manufacturing of critical pharmaceutical ingredients.”
Frozen Foods Express Transportation Services, Inc.
Bates County, Missouri
Over the past several years, the community of Butler, Missouri has experienced the closing of a shelving manufacturing facility, layoffs of a major insurance industry employer and the closure of the only locally owned grocery store. The announcement in January 2020 of the closure of the Russell Stover facility, which had been an anchor in the city’s small industrial park since 1990, was a particular blow that led to the loss of 10 jobs. Each of these events began to cultivate a sentiment that Butler was slowly losing its economic vitality.
One of the facilities closed by Russell Stover in Butler, however, was a cold storage distribution center that attracted the attention of Texas-based Frozen Foods Express Transportation Services, Inc. Owned by KLLM Transport Services, FFE concentrates on its core business which is temperature-controlled LTL (less-than-load). FFE is the largest asset-based temperature-controlled carrier in the U.S., with 17 locations throughout the country providing cold storage and break bulk services.
FFE was running out of space at its facility in Gardner, Kansas, and the Russell Stover building in Butler provided plenty of room for growth and a workforce eager to return to work. FFE saw an opportunity to expand its presence by purchasing the building and adding 60 new employees. This was wonderful news to the Butler community, which was still reeling from the loss of Russell Stover.
Not only did FFE make improvements to the building and add 60 new jobs to the community, it provided the people of Butler with an outstanding opportunity to earn extremely competitive wages. The projected wages are 142 percent of the Bates County average. Butler is a rural community, and many residents drive long distances for work. This project provided people with high-quality jobs closer to home. FFE employees earn an income that allows them to live comfortably in Butler.
In addition to boosting morale in a community that desperately needed positive news, there are many additional economic benefits that come with this announcement. FFE brings great paying jobs that start at nearly $10,000 more than the median per capita income in Bates County. In addition, the company invested millions to upgrade the interior of the building as well as to restore the exterior and add landscaping to the property. It hired local contractors for these projects and worked with other local businesses to meet its start-up needs. The company has already proven to be a supporter of the region’s schools and community events.
“We are very excited about expanding our operation into the Butler region,” said Jim Richards, President and CEO of FFE Transportation. “We look forward to working closely with the community and being a great partner.”
City of Pharr, Texas Nursing Program
Hidalgo County, Texas
Like many communities, the City of Pharr and the Pharr Economic Development Corporation found that regional area hospitals were suffering from a significant shortage of nurses and other health practitioners during the COVID-19 pandemic. It had become apparent that many high school graduates and current university students in the region were unable to afford the cost of further education.
The COVID-19 pandemic highlighted the already present nursing shortages in the region, with hospitals in the area struggling to provide an adequate amount and level of healthcare to patients in need of it. As many adolescents in the area live in poverty or have other obstacles standing between them and higher education, with quite a high percentage of students at the University of Texas Rio Grande Valley’s (UTRGV) being first-generation students, studying nursing was out of reach for many who would have wished to. To relieve the shortage, the City of Pharr embarked on an ambitious program to help bridge the gaps.
Through funding from the CARES Act, the city will expand the UTRGV School of Nursing facilities in Pharr to allow a significantly higher number of students to graduate, bolstering both the staffing at local hospitals and medical facilities and the local economy once the facilities are completed. Not only will this have a major impact on handling COVID-19 issues in the future, but residents will receive better, more efficient medical care.
The Pharr EDC Foundation was able to fund 129 scholarships for students in Pharr. Not only will this help to increase and diversify the student body at UTRGV, bringing many underserved students’ perspectives to university, it will have a positive benefit for the local economy, preparing more students to fill employment gaps or engage in entrepreneurship in the area.
In 2021, Dr. Reymundo Ramos, the vice president for Student Success at UTRGV, was quoted as stating that more than 60 percent of students at UTRGV are first-generation students; doubtless affording the opportunity to even more students to graduate with professional degrees will encourage others to apply themselves in school and seek higher education, improving their lives along with the lives of those students and families directly affected.
“We are grateful to the City of Pharr for its generosity and thank Mayor Hernandez for his support of the UTRGV School of Nursing,” said UTRGV President Guy Bailey. “Together, we can help attract and retain the best and the brightest students as we further expand the Valley’s healthcare services.” T&ID
Related Agencies
- Wake County Economic Development
- Economic Development Partnership of North Carolina
- Caldwell County Economic Development
- Louisiana Economic Development
- Chester County Economic Development
- South Carolina Department of Commerce
- Development Corporation of Abilene
- Texas Economic Development Corporation
- OneSpartanburg Inc.
- Blount Partnership
- Maryland Department of Commerce
- Frederick County Office of Economic Development
- Martinsville-Henry County Economic Development Corporation
- Macon Bibb County Industrial Development Authority
- Georgia Department of Economic Development
- Missouri Department of Economic Development
- Pharr Economic Development Corporation